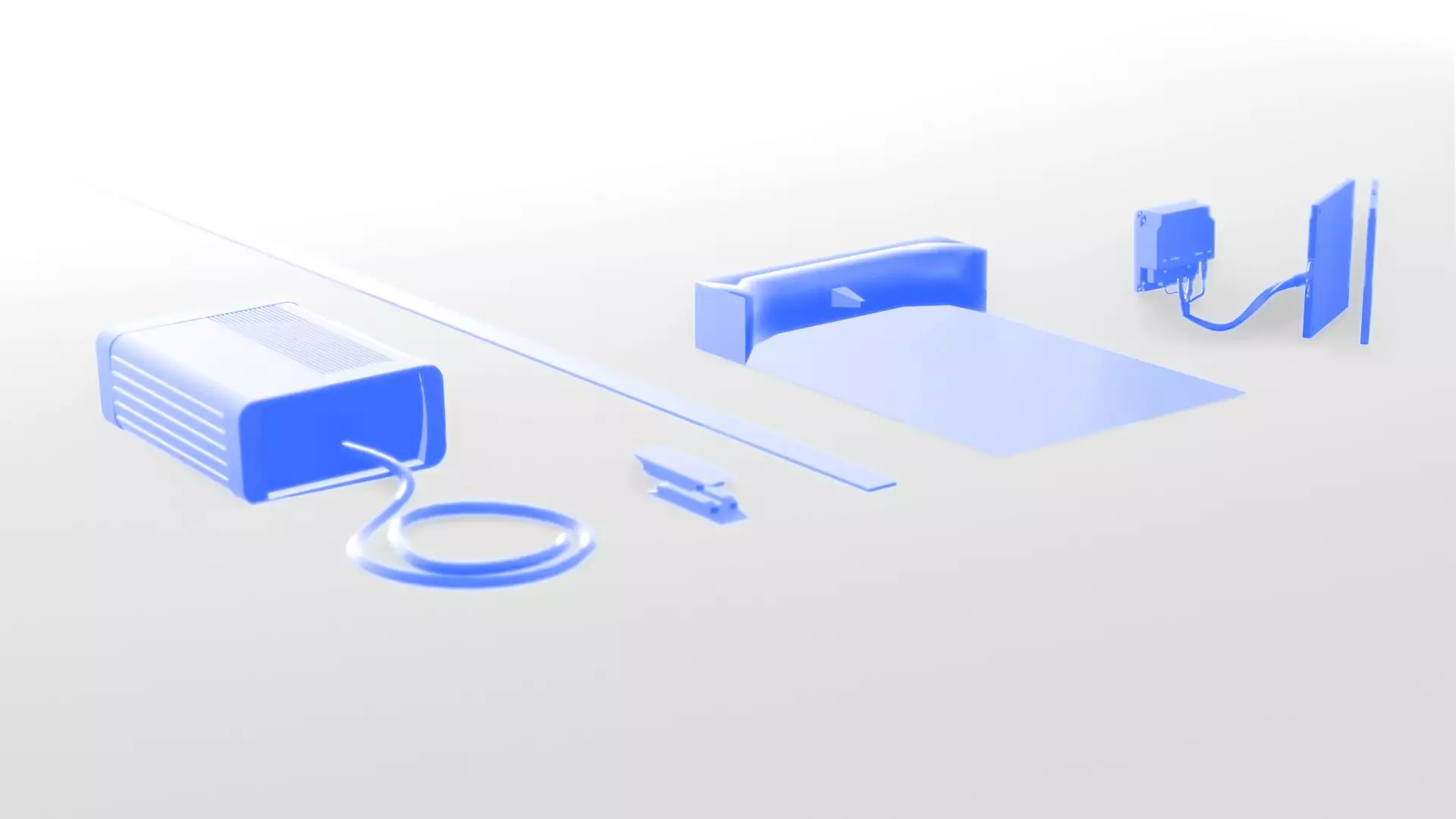
Battery Charging Technology Comparison for Industrial E-Vehicles
Which charger is the key to more productivity?
Whether forklifts, automated guided vehicles (AGVs), autonomous mobile robots (AMRs) or the classic “ant” – modern industrial trucks (AGVs) in industry and logistics are now predominantly equipped with powerful lithium-ion batteries. The technology has many advantages – but only if it is charged with the right battery charging technology. In this article, you will get an overview of which battery chargers are available, what advantages and disadvantages the individual systems have, and how you can use them to increase productivity.
What are the battery types and battery chargers?
Modern logistics infrastructures require above all performance – from the beginning to the end of a shift. Here, modern lithium-ion batteries impress with their performance, low maintenance requirements and long service life.
While lead-acid batteries are designed for 500 to 2,000 life cycles , modern lithium-ion EV batteries exceed these many times over. For example, an NMC (lithium nickel manganese cobalt oxide) battery lasts 3,000 to 5,000 life cycles. An LFP battery (lithium iron phosphate) around 7,500 life cycles and LTO batteries ( lithium titanate ) even more than 15,000 .
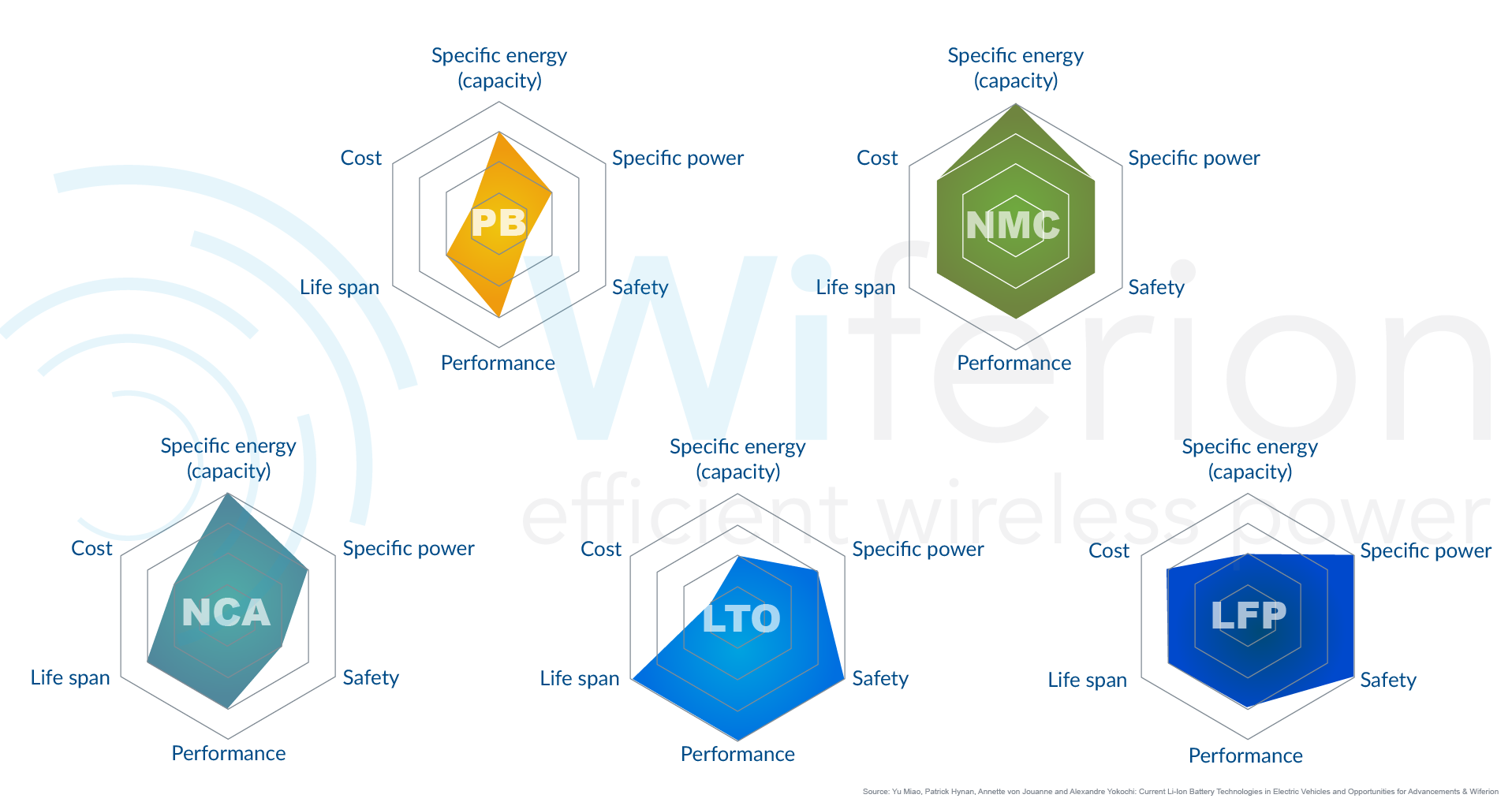
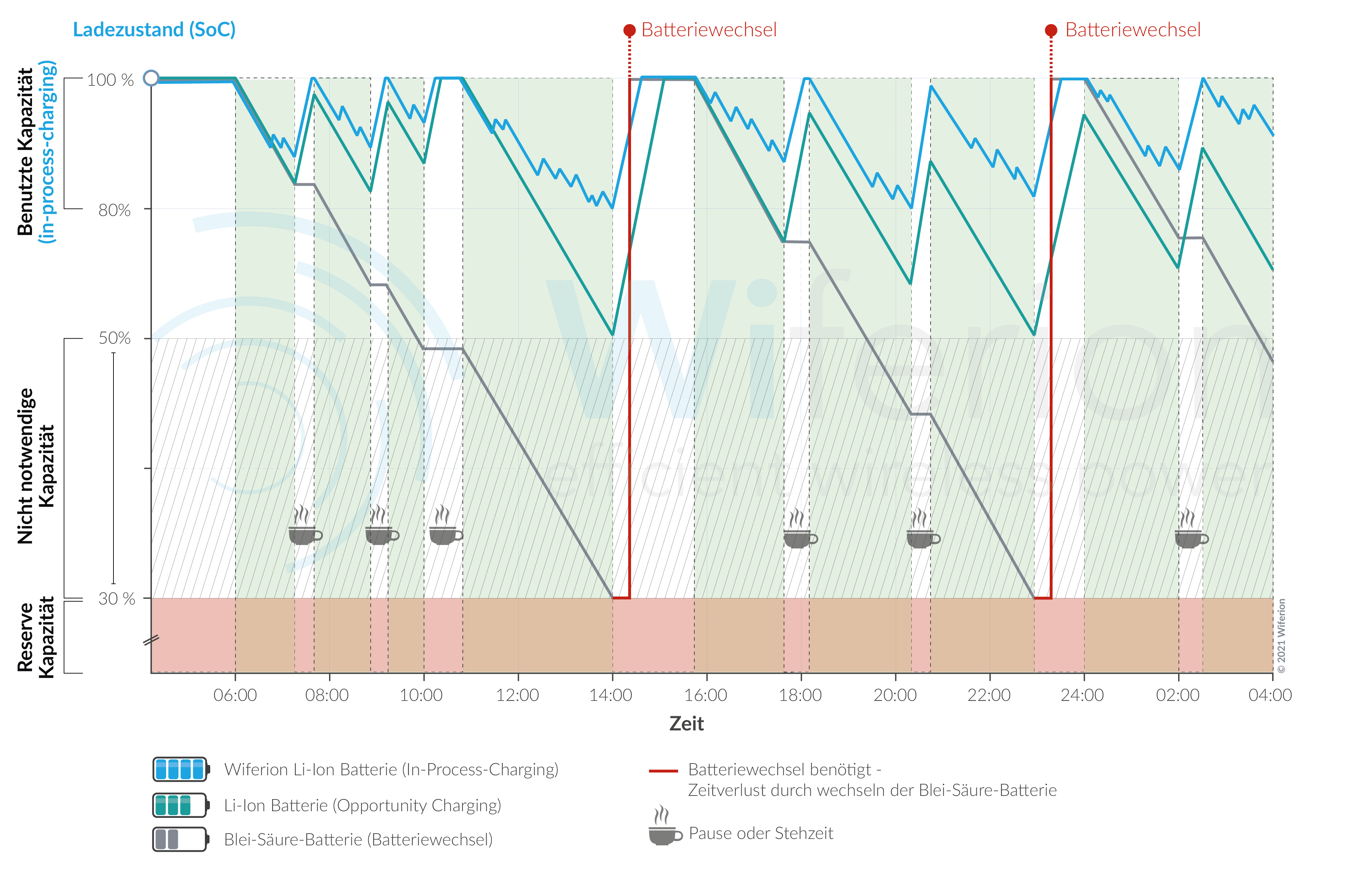
Total cost of ownership (TCO) of lithium batteries improves significantly
The service life also depends on the type of charge and care. For lithium, a distinction is made between full cycles and charge cycles. With lithium, the charging and final charging of the entire battery capacity counts as one cycle. The capacity of several charging steps is added up. With lead-acid batteries, on the other hand, each individual charging process is ONE cycle – even if only part of the usable capacity is charged or discharged.
This means that the energy storage systems even outlast the lifetime of the vehicles used and are therefore a particularly sustainable investment.
Cell technologies suitable for industrial applications, such as LFP and LTO, allow vehicles to be operated over their entire service life without battery replacement. The total cost of ownership (TCO) of lithium batteries is also significantly improved compared to lead-acid batteries.
In addition to their service life, the technologies’ charging capability is ideal for using short stops in the operating sequence to supply power. This eliminates the additional time previously required for charging operations and fully charging batteries.
Various chargers are available for charging the powerful batteries. These differ in terms of economy, maintenance requirements, flexibility as well as occupational safety. You can find out exactly how here in our battery charger comparison for different battery types.
See our big battery charger comparsion here!
Battery chargers with charging contacts
Wired battery chargers with plug connectors
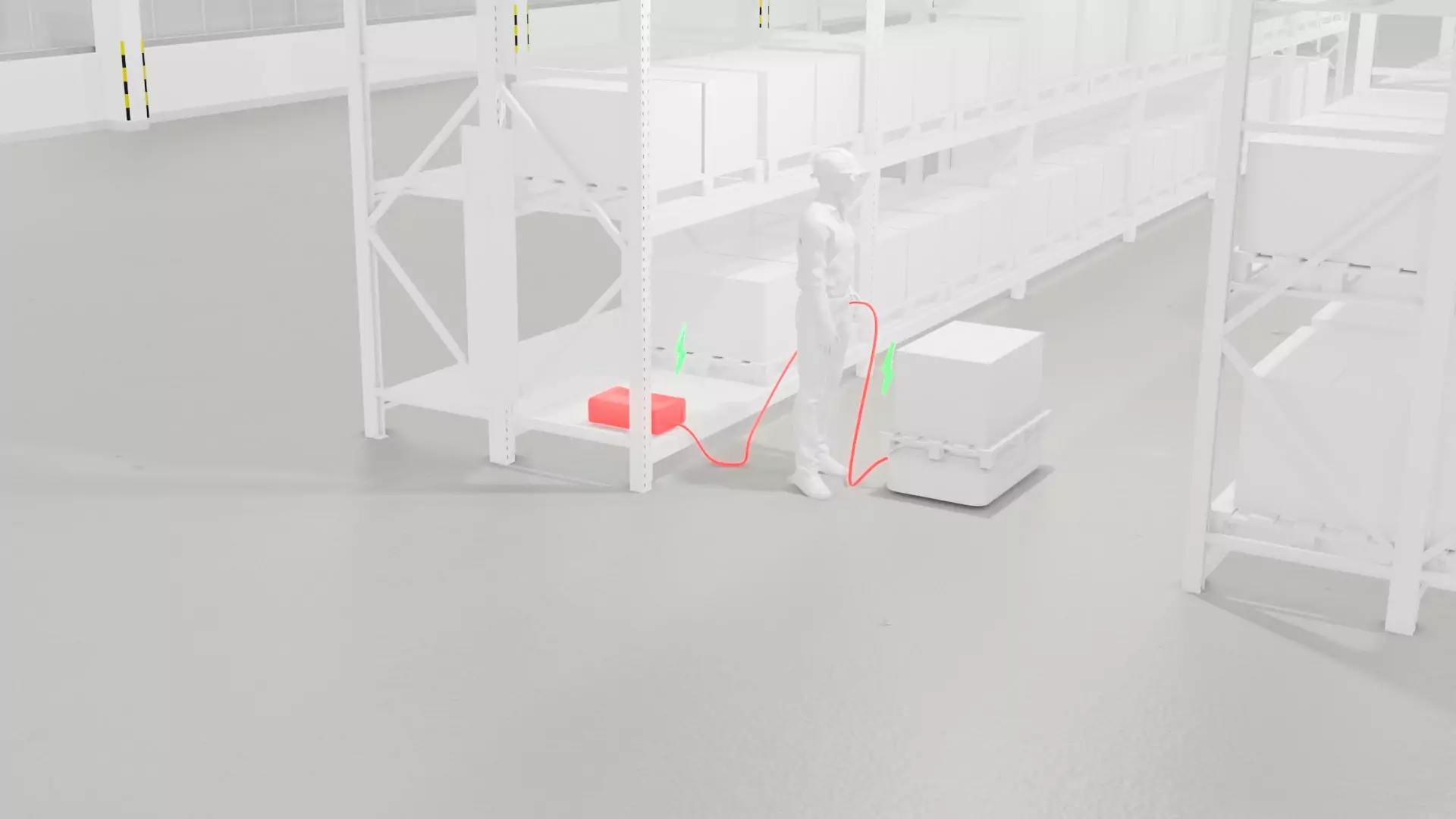
Plug connections are the classic industrial battery charger
Wired plug-in connections are the classic when it comes to charging batteries. Here, employees connect the vehicles to the battery charger when the energy level is low, and to the charger during longer breaks or after the end of the shift.
For occupational safety reasons, charging points are often not located in the immediate vicinity of production areas. The forklifts usually have to travel to charging zones that are further away. These are sometimes even located outside the production hall. The route through the warehouse does not add value. In addition, the vehicles are missing from the production process during the loading process until the battery is fully charged.
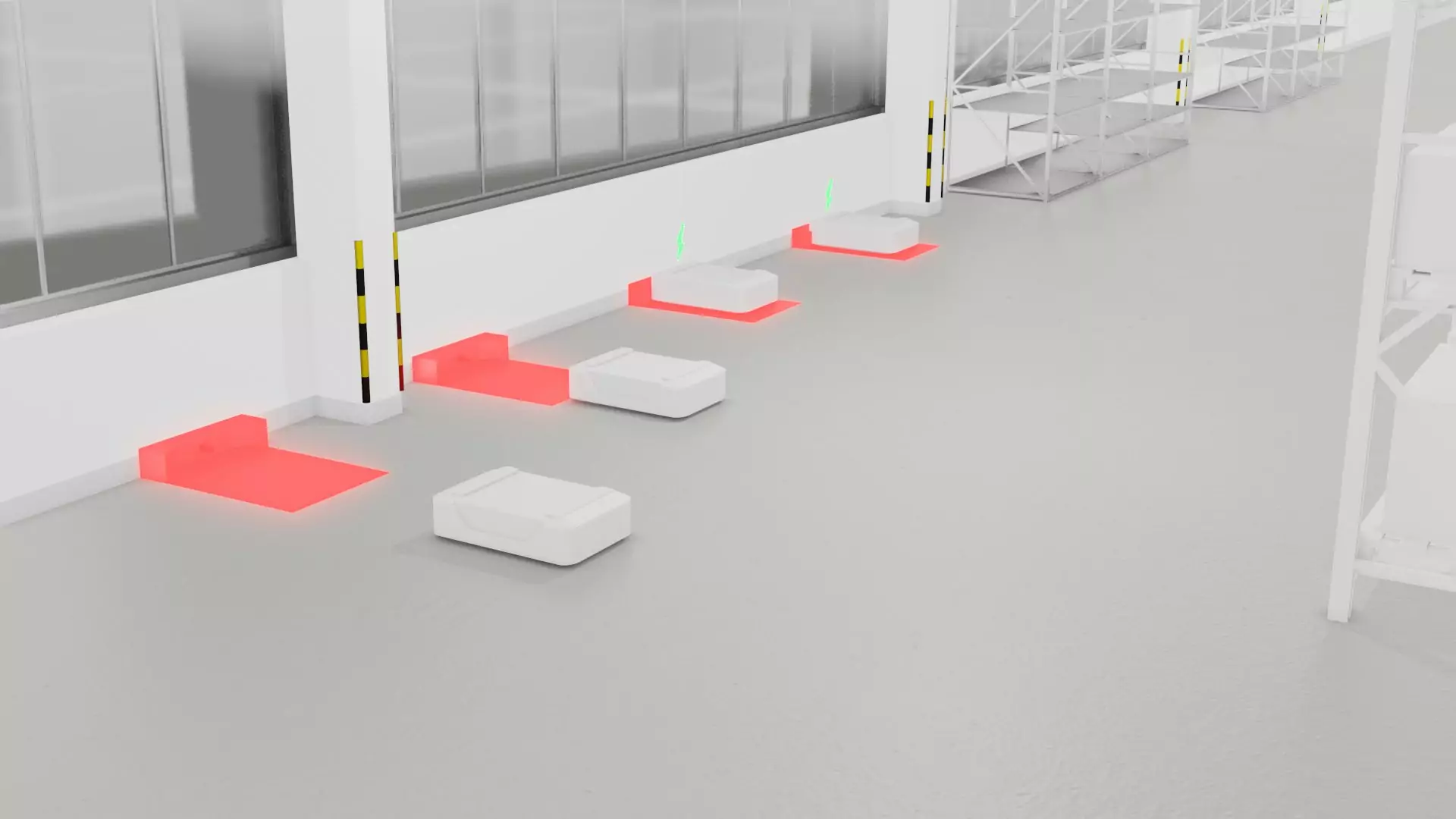
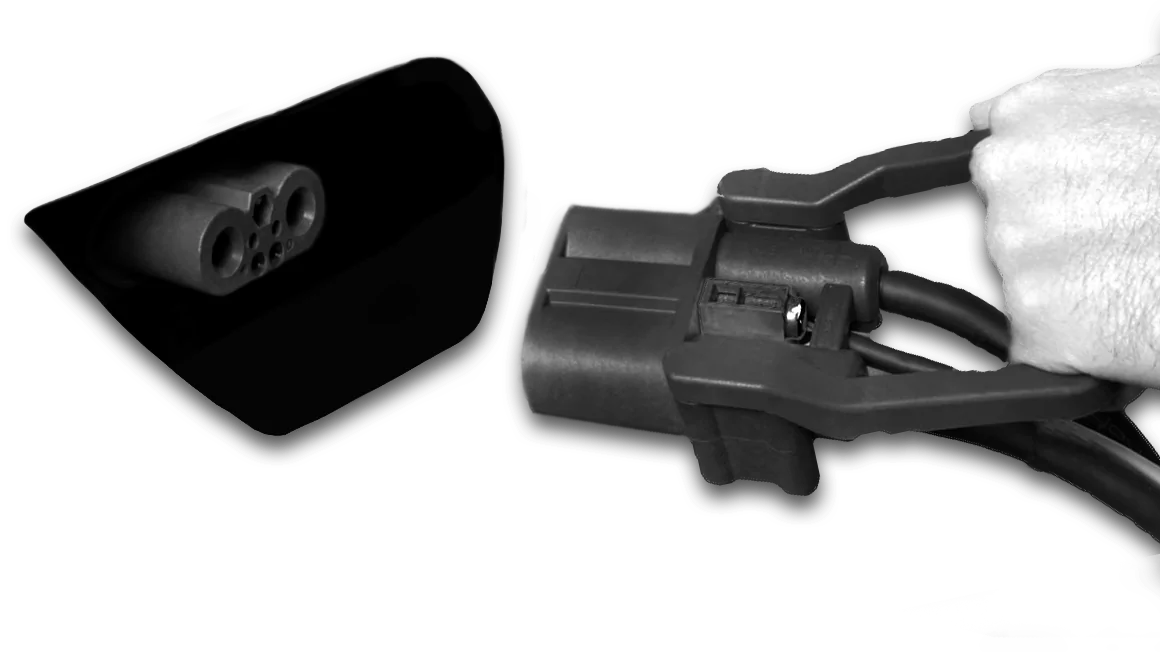
Damaged charging cables are cost drivers
Despite their supposed robustness, cable-based battery charging systems are high-maintenance and prone to failure. Improper use results in force damage and other safety issues such as broken pins and torn cable ends. Damaged charging cables must be replaced regularly, are often a hidden cost driver, and represent another potential hazard.
Employees also repeatedly forget to connect the plugs of cable chargers to vehicles. The result is an energy level that is too low for downstream tasks.
Forgotten plugs and longer charging phases
If automated charging concepts are implemented with this technology, the number of plug-in processes will increase, which means that this problem can be expected to gain further weight.
Since the vehicles are not supplied with power during operation, the energy level of the batteries drops continuously during operation and must be compensated for by longer charging phases. Therefore, the expensive batteries need to be much larger to ensure that the trucks always have sufficient energy.
In addition, the increased power costs of the peak loads hit when the entire fleet is recharged at the end of the shift.
Ultimately, cable-based charging concepts are difficult to automate and the industrial trucks, as well as automated guided vehicles (AGVs), are not productive during the charging process.
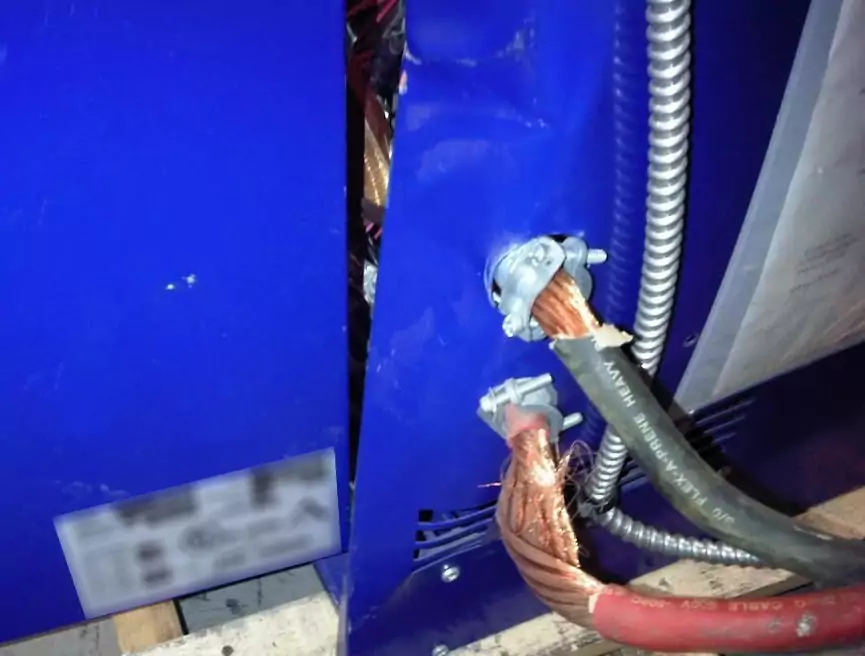
Advantages of cable charging
- High efficiency
- Relatively inexpensive in the investment phase
- Well-established technology
Disadvantages of cable charging
- High maintenance effort
- Difficult to automate
- Industrial trucks are missing in the workflow
- Requires large batteries
- Loading unit requires space and is therefore often not easy to distribute in the plant …
Interested in our battery charging technologies?
Contact us!
Contact us!
Battery chargers with charging contacts
Battery chargers with charging contacts
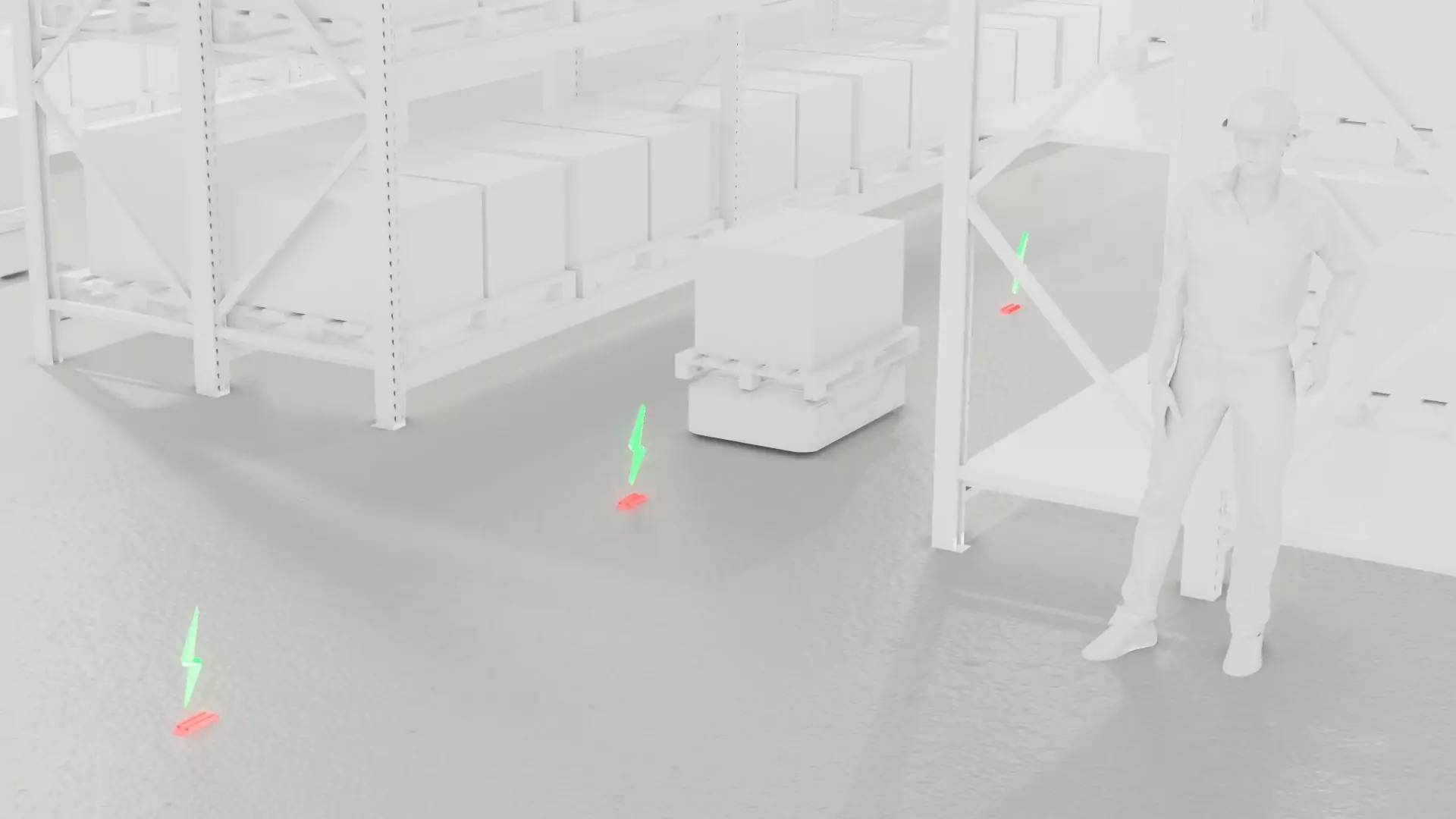
Large bill of material with sliding contacts
Sliding contacts are often used to supply power to the battery of AGVs or automated industrial trucks. Here, stationary charging contacts are permanently installed in the storage environment and a counter contact is mounted on the vehicles.
This concept as an AGV charger is often tempting because of its initial simplicity. However, if one considers the overall concept consisting of control for disconnecting the contacts from the voltage supply, a mechanical lowering device and the additional communication required for controlling the charging process, the complexity and thus the BOM (Bill of Materials) quickly increase.
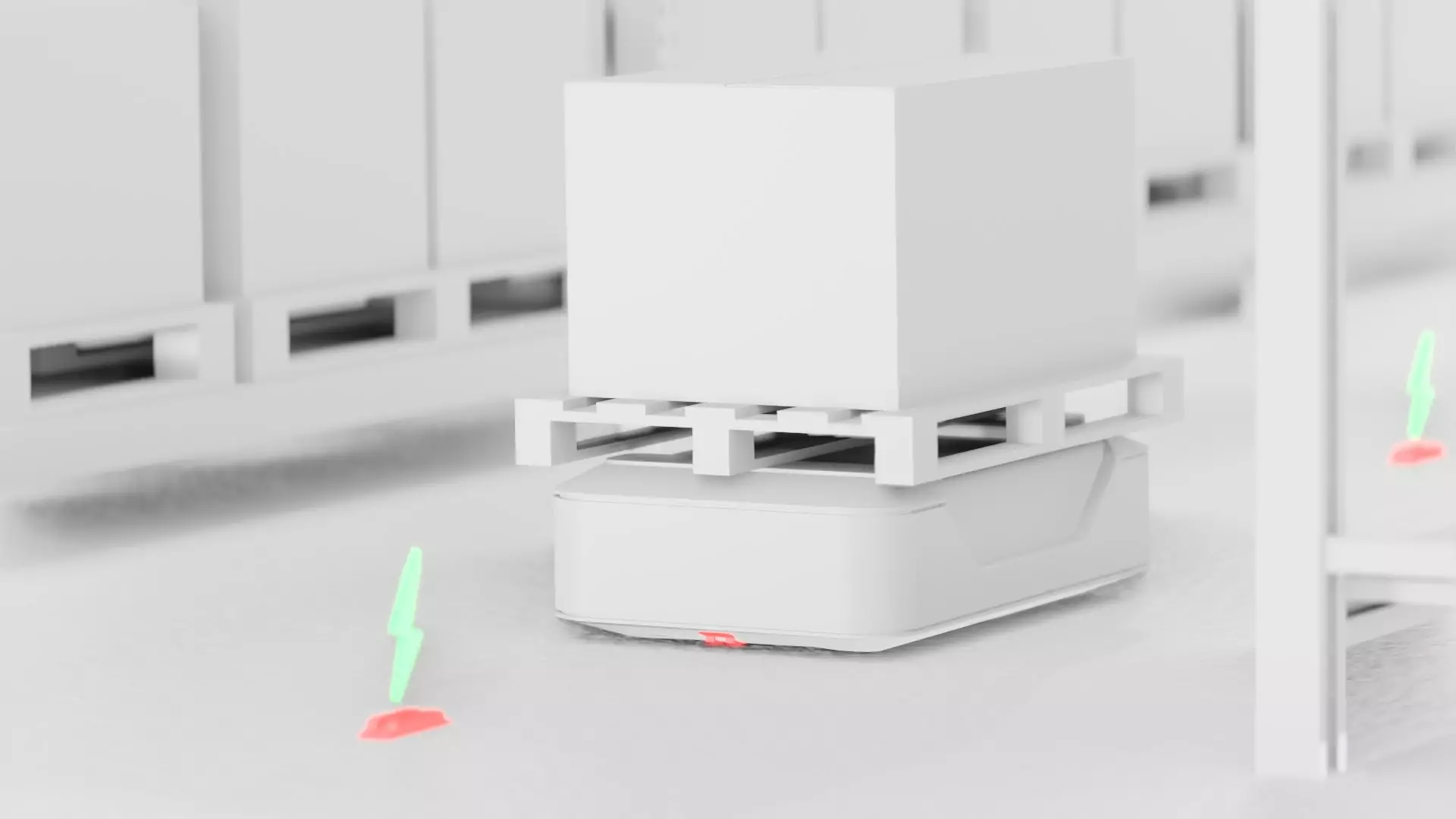
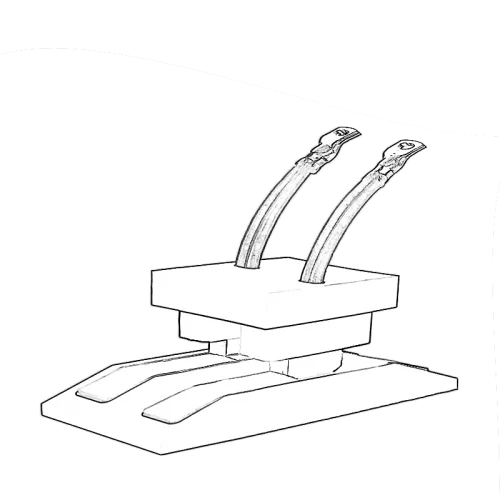
Positioning for charging contacts must be exact
Thus, the switching relays lead to problems again and again. For example, if the control is not correct or the “contacts” are stuck. If the charging system does not function correctly, sparking can occur after the charging process is complete.
It is also important for system availability that the positioning is carried out accurately for contact charging. How the contact process is set up determines whether oxide layers are removed before charging and burn-in can be avoided.
The designs of the charging stations are complex and expensive at higher currents
Ultimately, contacts are wear parts , which can lead to more expense for component changes in an opportunity charging concept. The continuous abrasion creates copper dust that pollutes the charging station and the production environment. The fine copper particles float in the air and pose a health hazard to employees who are permanently in the hall.
In production lines, charging contacts mounted on the floor are also a barrier and are frowned upon because of the risk of tripping for employees. For this reason, the charging point of the battery charging technology with sliding contacts is not installed in the immediate vicinity of the production areas for reasons of work safety .
The designs of these industrial battery chargers are complex and expensive at higher currents. This is because large energy transfers are only made possible by strong contact forces. These in turn have to be absorbed by the charging stations. This means that greater maintenance is required to ensure smooth operation . In the case of light vehicles, this also results in a limitation in the charging current for all types of batteries.
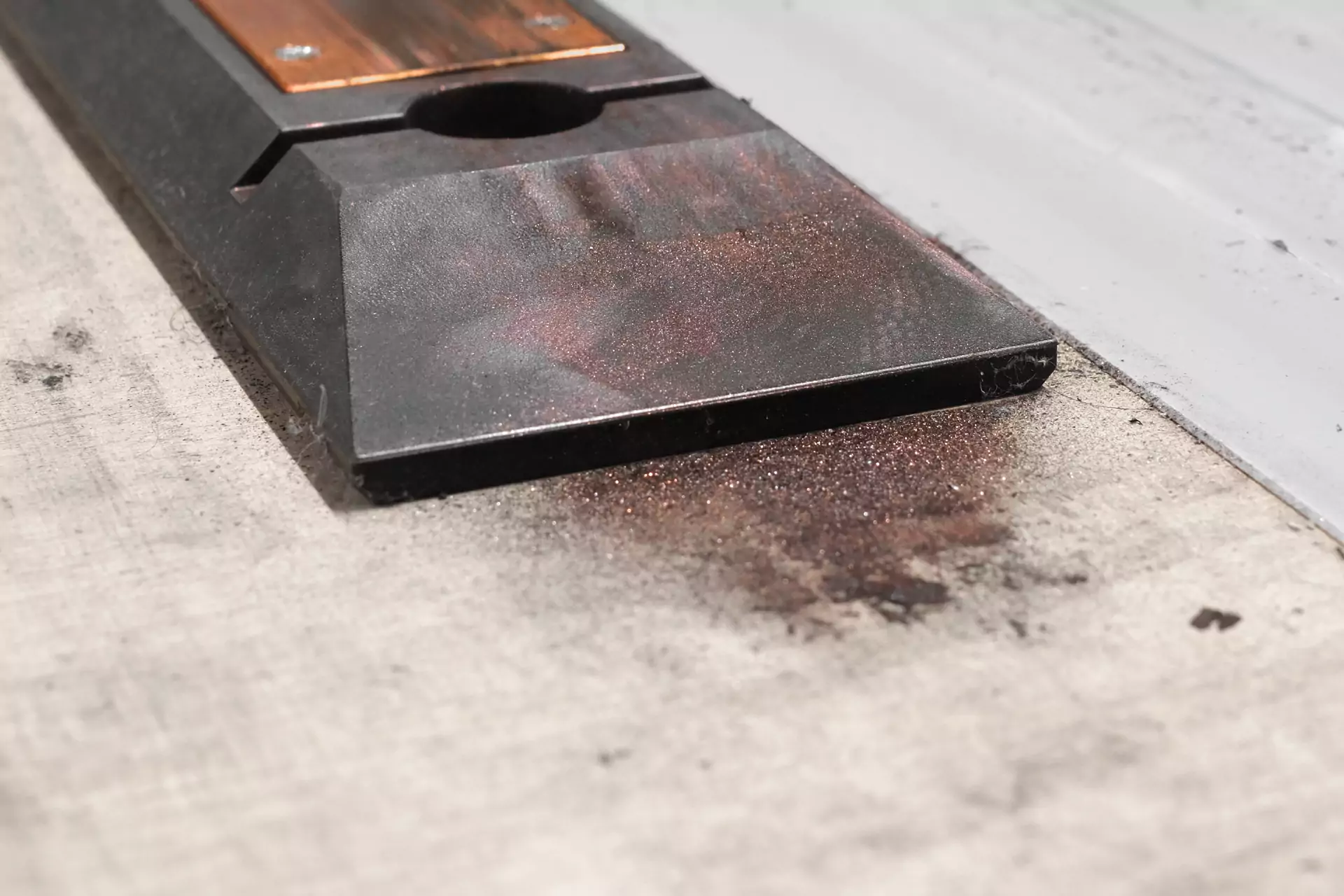
Advantages of charging with sliding contacts
- Can be automated
- Limited availabilities
- First integration simple
Disadvantages of charging with sliding contacts
- High maintenance
- Complex control necessary
- Interventions in the infrastructure
- Tripping hazard for employees
- Wear of the charging contacts
- Industrial trucks missing in workflow
- Precise positioning necessary
Interested in our battery charging technologies?
Contact us!
Contact us!
Battery charging technology with inductive conductor lines in the ground
Battery charging technology with inductive conductor lines in the ground
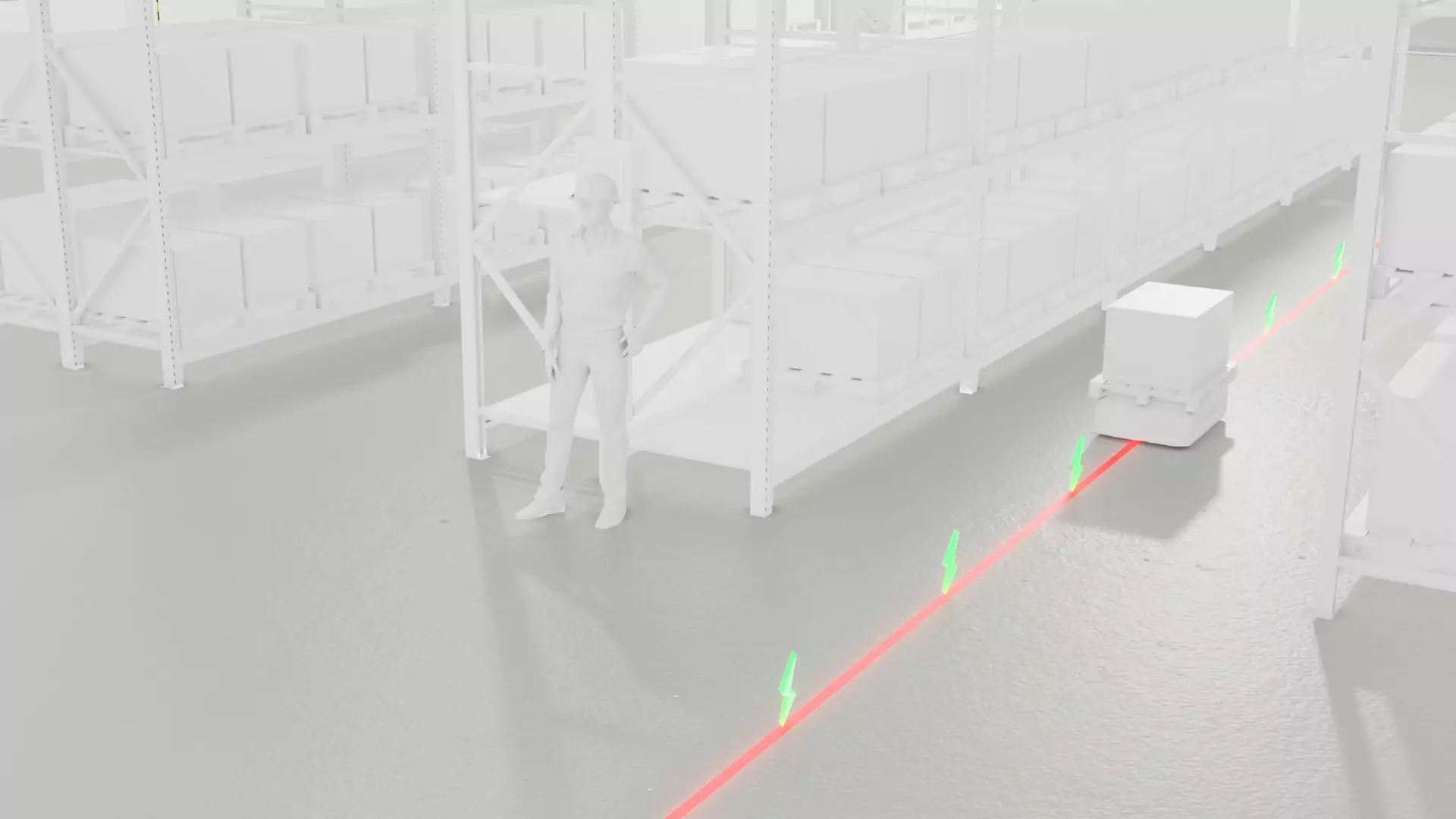
Extensive intervention in infrastructure necessary with inductor lines
Charging the battery via guideline systems is less common than charging via charging contacts due to its cost-intensive complexity. In this industrial charger, automated vehicles such as AGVs move along predefined routes with integrated power conductors.
Charging takes place inductively. However, extensive infrastructure intervention is required to install the conductors in the ground. The system is very costly and maintenance-intensive.
The conductors are integrated into the system in a project phase and are aligned and fixed to the feed point with the help of additional components along the routes. Extensive intervention in the infrastructure of the building fabric is necessary for the implementation.
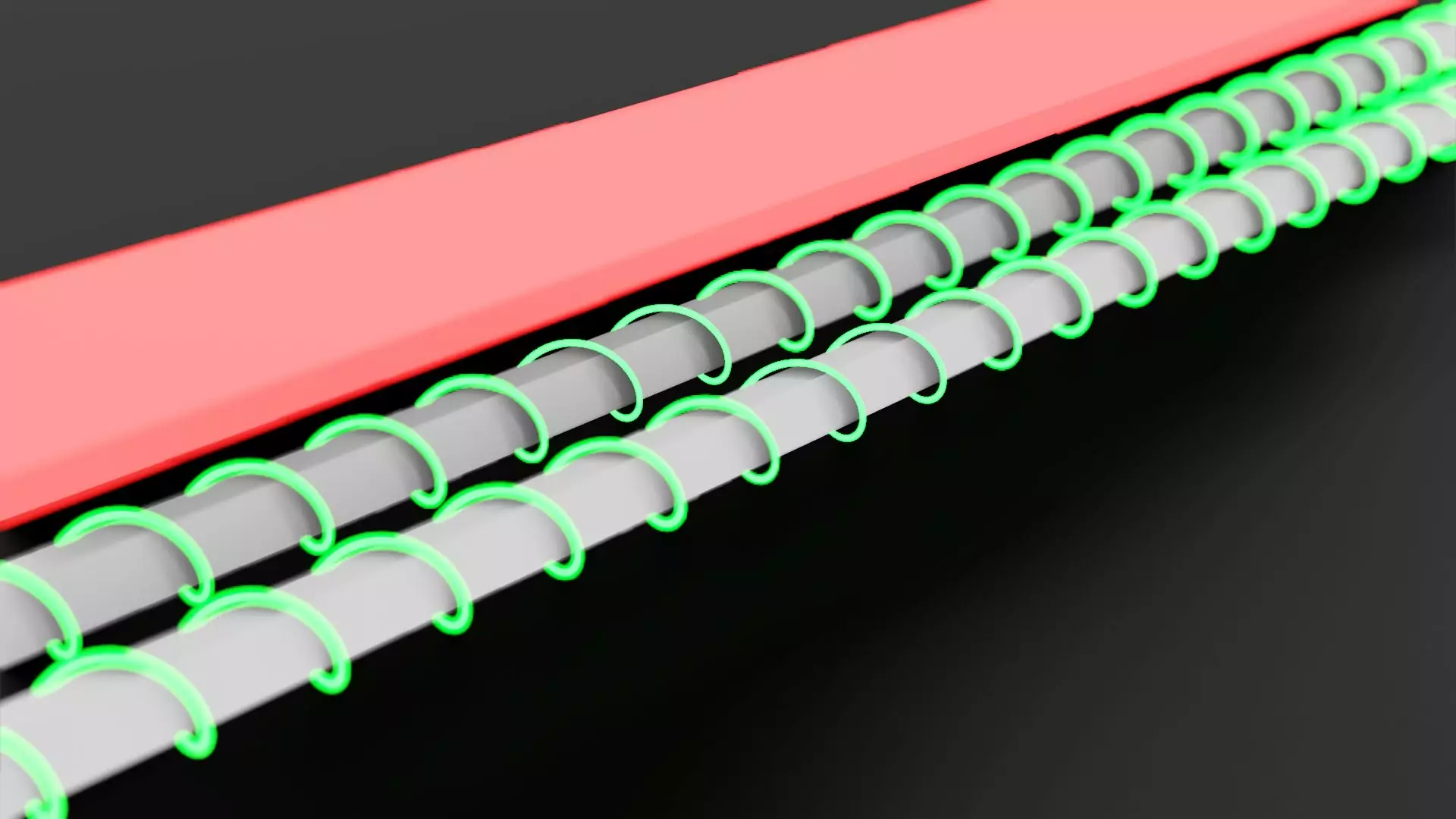
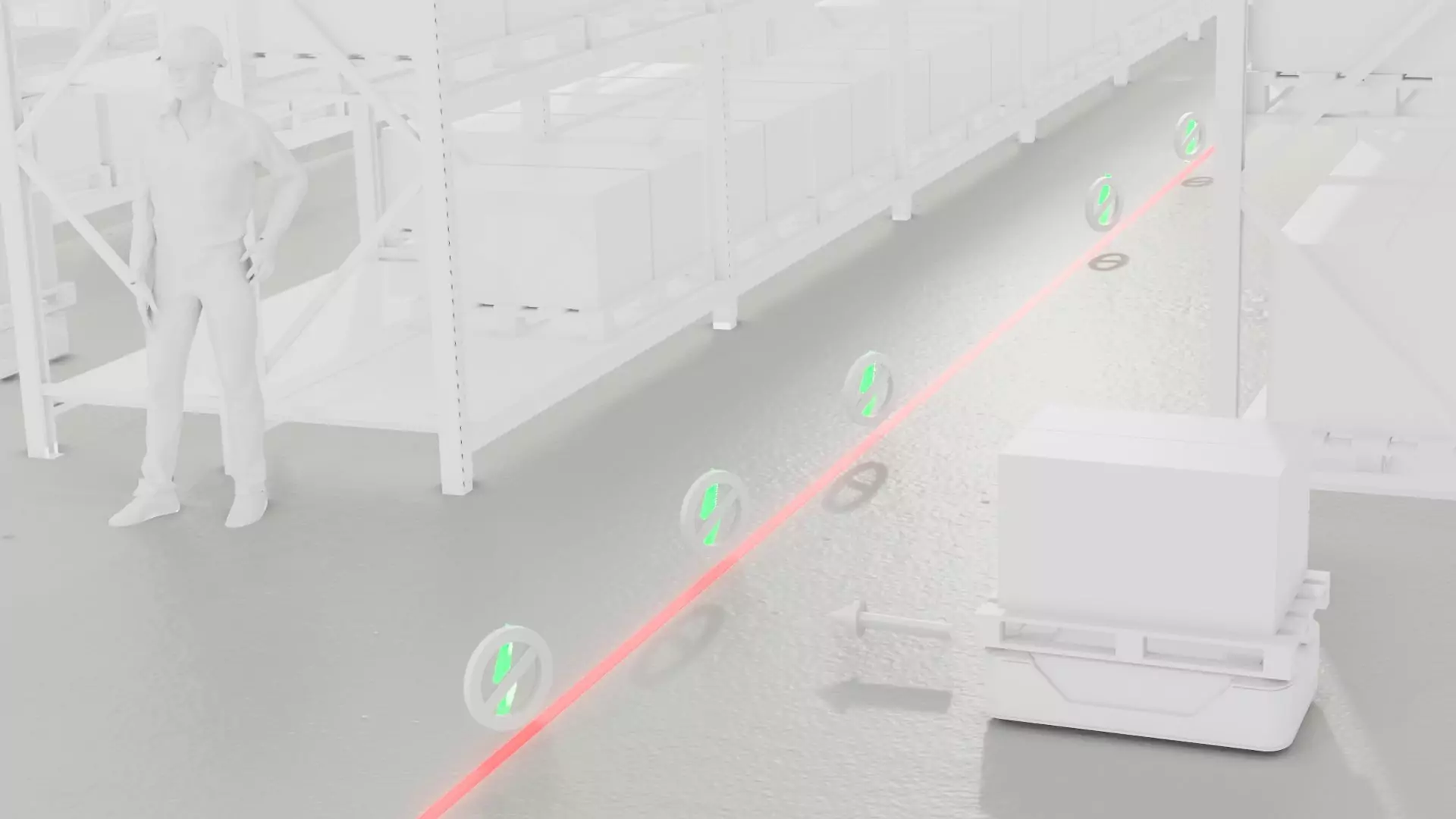
Conductor lines have a continuous magnetic field
For example, the hall floor has to be milled open so that the inductor lines can be installed. As a result, conductor line systems are very inflexible. The direction of travel of the AGVs is fixed. This can only be adapted to changing requirements with great effort. Every fleet expansion or route change becomes a challenge for the battery charger.
Line conductors generate a permanent magnetic field. When installing the chargers, a precise analysis of the infrastructure on site is necessary.
This is the only way to rule out any interaction with ground reinforcements caused by the permanent magnetic fields around the line. Otherwise, considerable losses will occur in the reinforcement and the ground will heat up. If the requirements for the work process change or the fleet is to be expanded, a new project phase becomes necessary.
Inductive conductor lines are permanently active and no communication between vehicles is possible
Since the conductors are distributed over a large area, however, it is not only the vehicles that move on the conductors. Some employees also have to operate on the conductors in the magnetic field during their entire working hours .
Communication between the conductor and the components in the vehicle is not possible due to the system. Therefore, the line currents must be maintained at all times, which limits the efficiency of the chargers.
However, in systems with discontinuous inductive lines, all vehicles are rarely on the line. The feed-in power is usually greatly oversized and the conductor systems are permanently active. Depending on the design and the number of vehicles used, good line charger systems have an overall efficiency of around 60% .
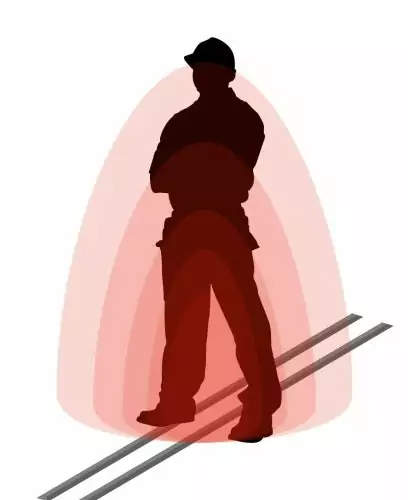
Advantages of charging with inductive conductor lines
- Automated charging process
Disadvantages of charging with inductive conductor lines
- Costly
- Complex planning and realization
- Poor efficiency
- Inflexible
- Interventions in infrastructure necessary
- Not without danger for some marginalized groups
Interested in our battery charging technologies?
Contact us!
Contact us!
Inductive point chargers
Inductive point chargers
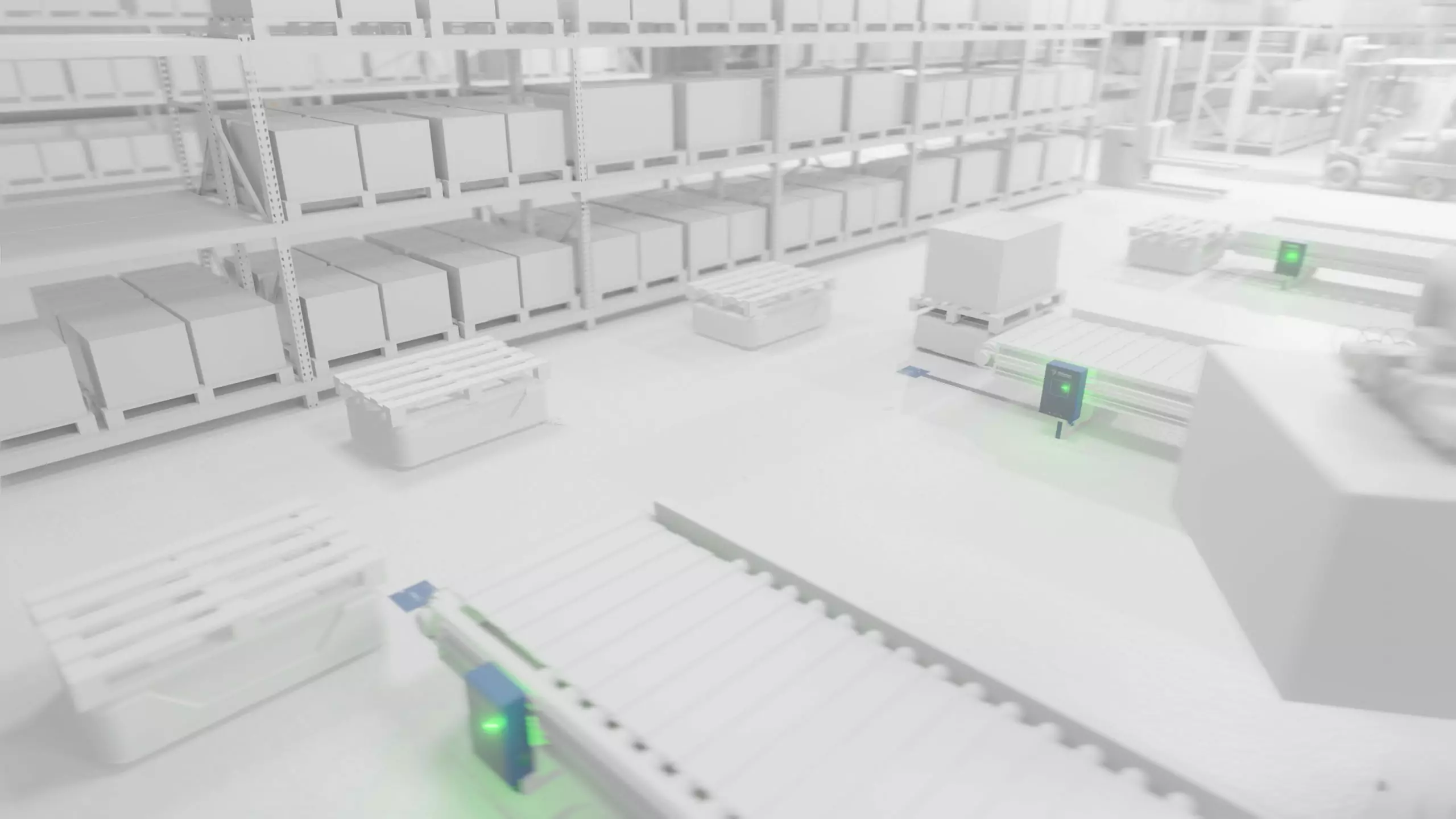
A new approach to battery charging for industrial trucks is inductive point charging systems. These are becoming increasingly popular for supplying power to industrial trucks and AGVs due to their numerous advantages. With wireless charger, energy is transferred automatically, highly efficiently and contactlessly according to the principle of magnetic induction.
Fully automatic charging of the vehicle battery
Instead of driving to a fixed battery charging station, the vehicles are temporarily charged automatically during their workflow at commonly frequented points in the warehouse with so-called “in-process charging”. The vehicles can thus perform their transport tasks in 24/7 continuous operation without interrupting the logistics processes for charging breaks. This eliminates unproductive downtime, which is why the availability of AGVs, AMRs and industrial trucks is increased by up to 30% .
As soon as a vehicle reaches the charging pad of an inductive point charger, the charging process starts automatically within 1 second. This means that the entire system is ready for operation in the shortest possible time. It does not matter whether it is a forklift, mobile robot or driverless transport system. Even the manufacturer or the installed battery does not matter, as long as the vehicles have receiving electronics.
One charging station can serve different batteries from 24 to 48 volts. Its immediately changes the charging mode depending on the vehicles needs. The charging characteristic on the vehicle is freely programmable and dynamically adapts to the respective battery status.
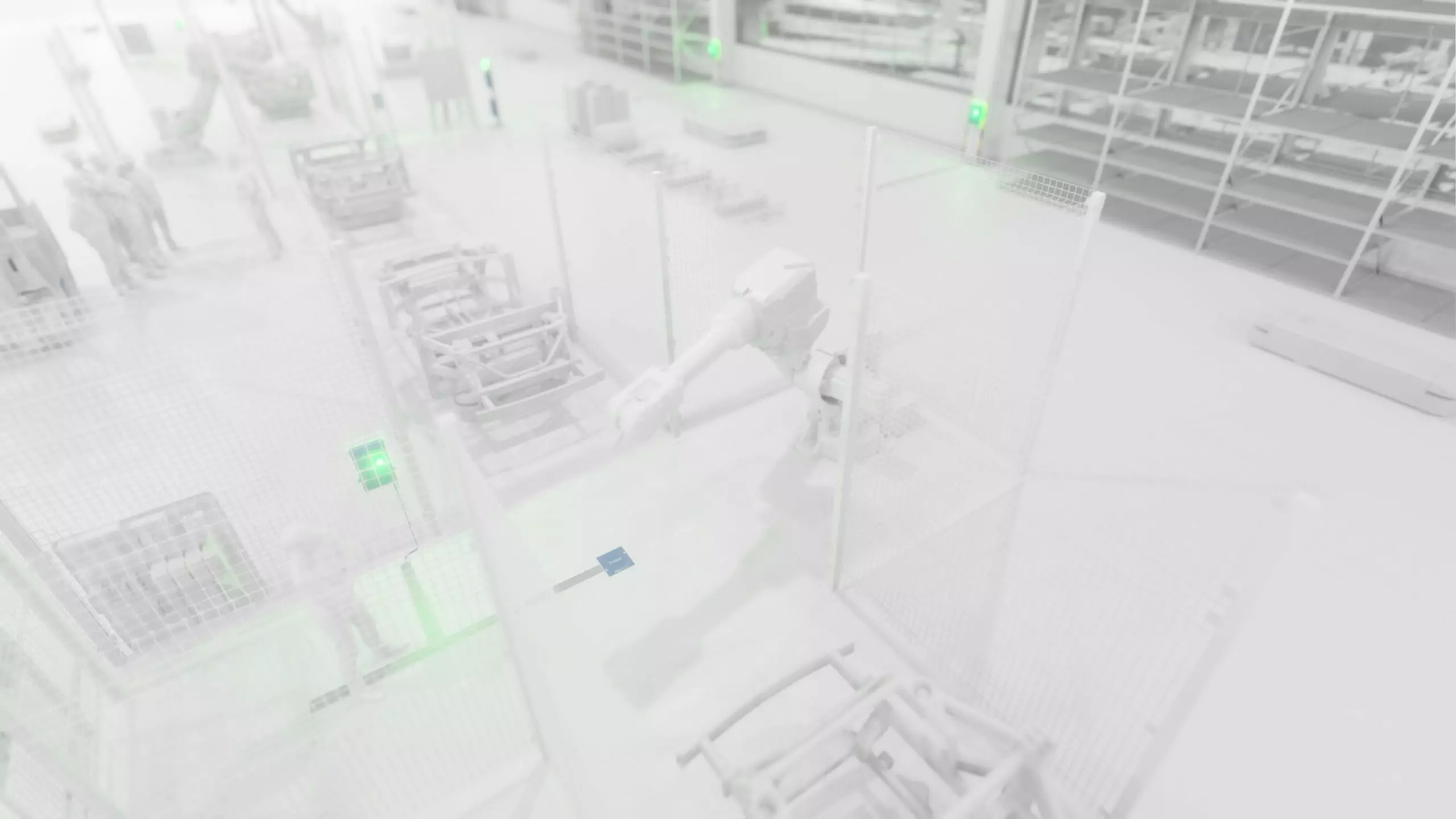
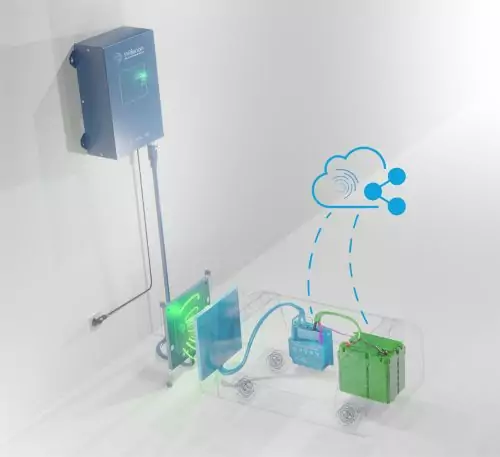
Easy installation and integration of the inductive chargers
Industrial inductive AMR chargers such as those from the German manufacturer Wiferion consist of a wallbox and a charging pad that can be flexibly installed at suitable locations in the logistics and production environment. The receiving electronics with receiver coil, mobile charging unit and energy storage unit are installed in the vehicle.
Advantages of inductive point chargers over conventional battery charging technology
What distinguishes inductive battery chargers: They only consume electricity when the charging processes are taking place. The efficiency of inductive fast charging systems is up to 93% ( Wiferion etaLINK ). This makes the efficiency just as efficient as that of the best wired chargers and significantly higher than the efficiencies of guideline systems.
Charging is fully automatic without contact. The charging process can be determined by the battery, so it is always operated at the optimum operating point and unwanted shutdowns, such as those caused by battery overtemperature, are avoided.
In contrast to battery chargers with plug-in or loop connections, there is no need for extra areas for industrial trucks, where the battery is charged . In addition, the vehicles are continuously productive and busy with value-adding tasks.
See here how SMA Solar Technology AG retrofitted their industrial trucks with the inductive charging systems and reduced their charging times:
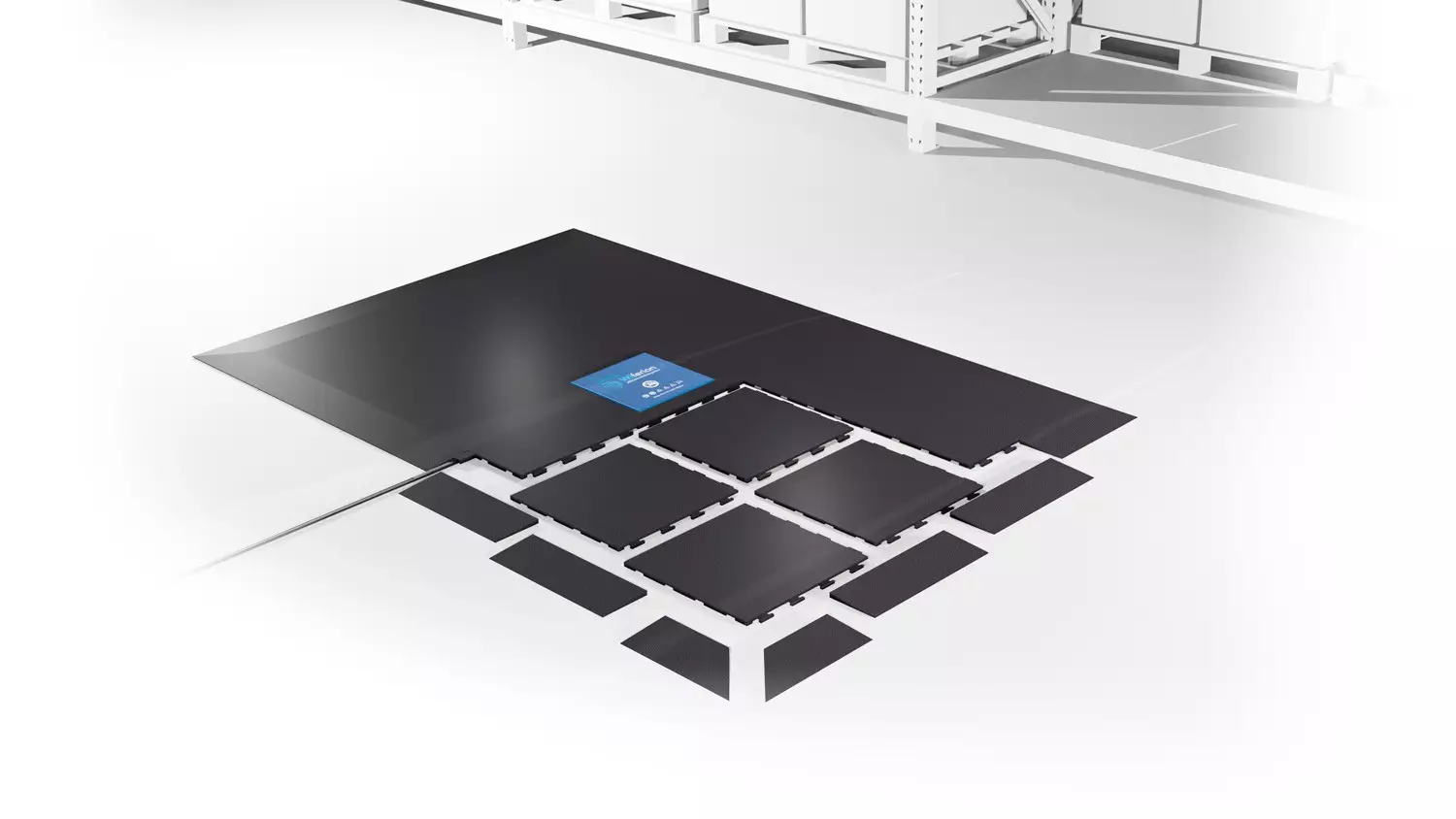
Vertical or horizontal installation of the inductive charging pads
As an inductive charger does not require mechanical sliding contacts, it is practically maintenance-free. Problems associated with conventional charging processes with oxidized plugs or broken cables are a thing of the past.
The components are only connected to each other via the magnetic field and are therefore suitable for long-term continuous use.
Inductive point charging systems are easy to operate and can be installed almost anywhere – on walls, on the floor, on driveways, at parking spaces or loading and unloading stations.
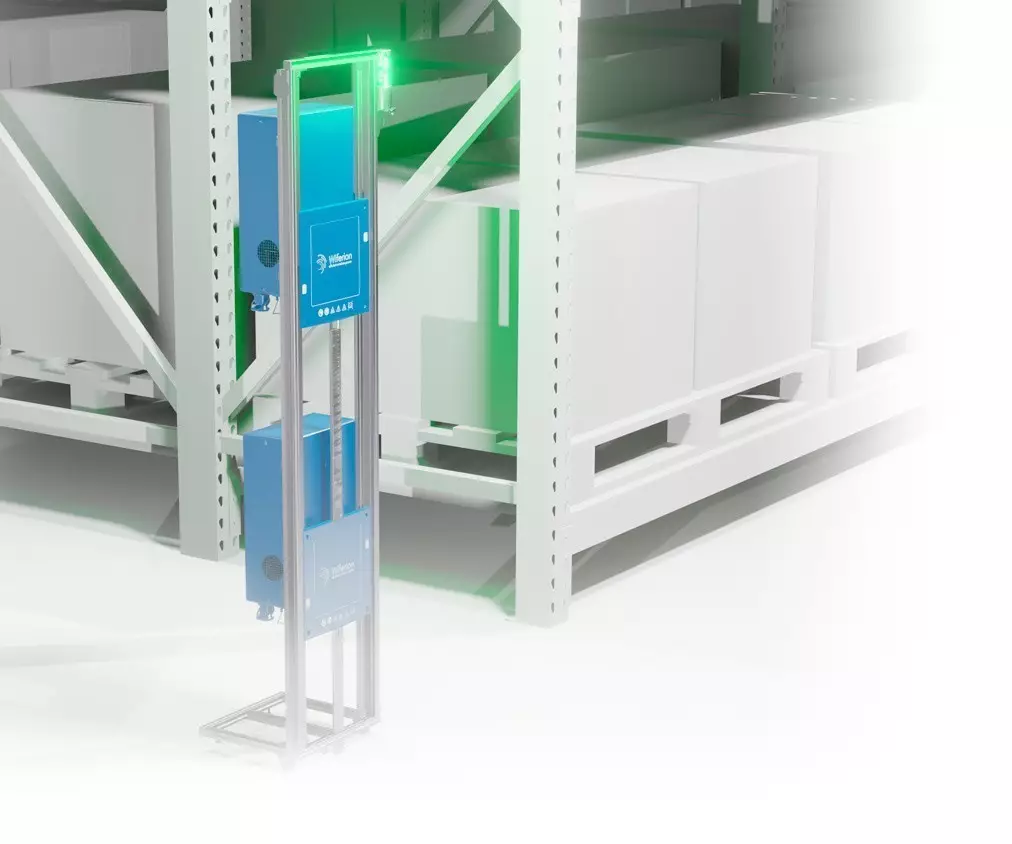
Safety and reliability increases with contactless, inductive point charging systems
For charging systems with plug-in and loop connections, complex peripheral circuits and protective devices must always be installed to ensure safety for employees and equipment. Since there are no open contacts with an inductive charger, occupational safety increases enormously.
In addition, the battery charging technology is weatherproof. Ambient conditions have no influence on the way it works. Moisture, dirt or dust cannot harm the system. It is an encapsulated system with IP 65 certification. This makes it possible for the first time to supply power to vehicles outdoors.
With conventional systems, integration into warehouse operations can often take weeks or even months. In contrast, implementing automation with wireless charging technology such as Wiferion’s does not require extensive infrastructure measures for most deployments.
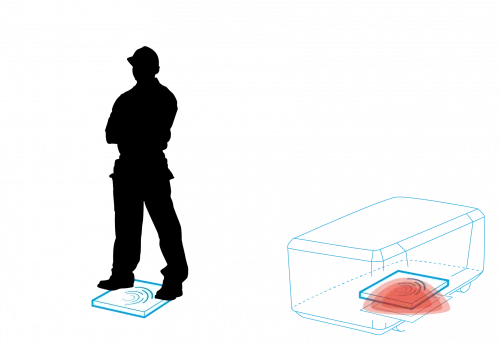
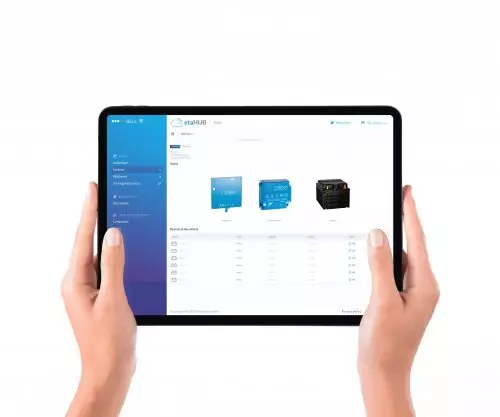
Flexible integration and readout of live vehicle data at any time
The automation solution with the modular battery chargers can be quickly adapted to changes in the process or new requirements. The charging unit and receiver coil can be installed on the vehicle within a very short time. Since mobile electronics and receiver coil are separate components, numerous attachment variants can be realized.
In contrast to conventional battery charging technology, inductive point charging systems offer for the first time the possibility to evaluate all relevant live information of the battery charge. With the aid of an integrated CAN interface, data such as energy levels, operating times and vehicle states can be retrieved in real time. Process reliability can thus be increased many times over.
Inductive AGV battery chargers with point charging are more expensive to purchase than wired charging solutions. However, these costs are quickly amortized due to the many advantages. Compared to solutions involving intervention in the infrastructure with sliding contacts and conductor lines, point charging systems are significantly less expensive.
Interested in our battery charging technologies?
Contact us!
Contact us!
Frequently asked questions about battery charging technology
Which AMR charger is the best?
Whether with cable, contact chargers, conductor line or inductive point charging – before you decide on a battery charger, you should check all available solutions. Each system has its advantages and disadvantages. Based on your specific requirements, experienced energy experts like Wiferion offer comprehensive advice.
Which charger is suitable for LiFePO4 and LFP battery (lithium iron phosphate)?
Inductive battery charging systems are generally suitable for all battery types. Since lithium-based batteries are designed for short-term opportunity charging with high currents, contactless battery charging technology is perfect for efficient power transfer.