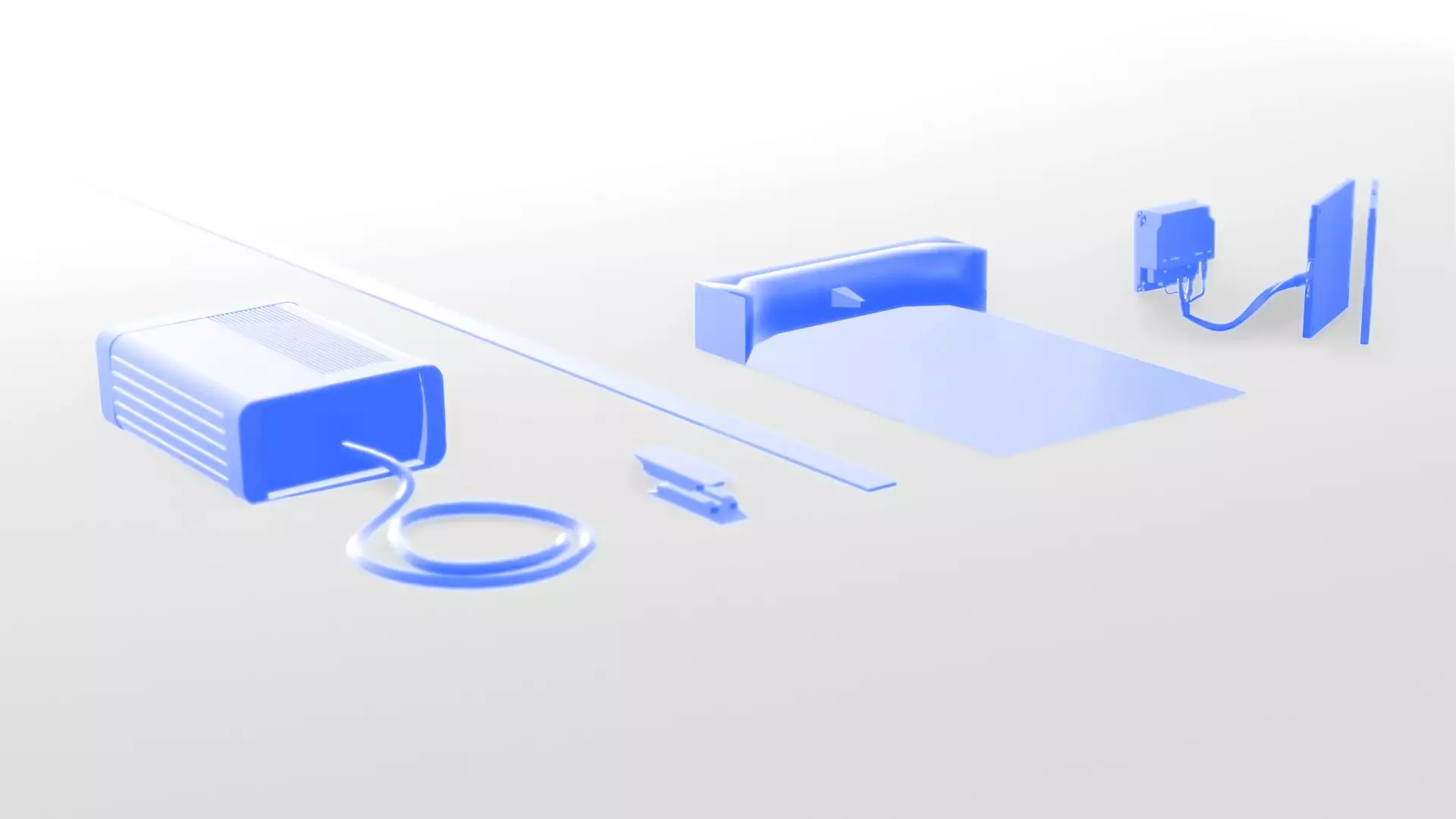
Batterieladetechnik Vergleich für industrielle E-Fahrzeuge
Welches Ladegerät ist der Schlüssel für mehr Produktivität?
Ob Stapler, fahrerloses Transportsystem (FTS), autonome mobiler Roboter (AMR) oder die klassische „Ameise“ – moderne Flurförderzeug (FFZ) in Industrie und Logistik werden inzwischen überwiegend mit leistungsstarken Lithium-Ionen-Batterien ausgestattet. Die Technologie hat viele Vorteile – aber nur wenn sie mit der richtigen Batterieladetechnik geladen wird. In diesem Beitrag erhalten Sie eine Übersicht, welche Batterieladegeräte es gibt, welche Vor- und Nachteile die einzelnen Systeme haben und wie Sie diese produktivitätssteigernd einsetzen können.
.
Welche Batterietypen und Batterieladegeräte gibt es?
Moderne Logistik-Infrastrukturen benötigen vor allem Performance – von Anfang bis Ende einer Schicht. Hier überzeugen moderne Lithium-Ionen-Batterien durch Leistung, geringen Wartungsaufwand und langer Lebensdauer.
Während Blei-Säure-Batterien für 500 bis 2.000 Lebenszyklen ausgelegt sind, übertreffen moderne Lithium-Ionen-Batterien diese um ein Vielfaches. So hält eine NMC-Batterie (Lithium-Nickel-Mangan-Kobalt-Oxid) 3.000 bis 5.000 Lebenszyklen aus. Eine LFP-Batterie (Lithium-Eisenphosphat) rund 7.500 Lebenszyklen und LTO-Batterien (Lithium-Titanat) sogar mehr als 15.000.
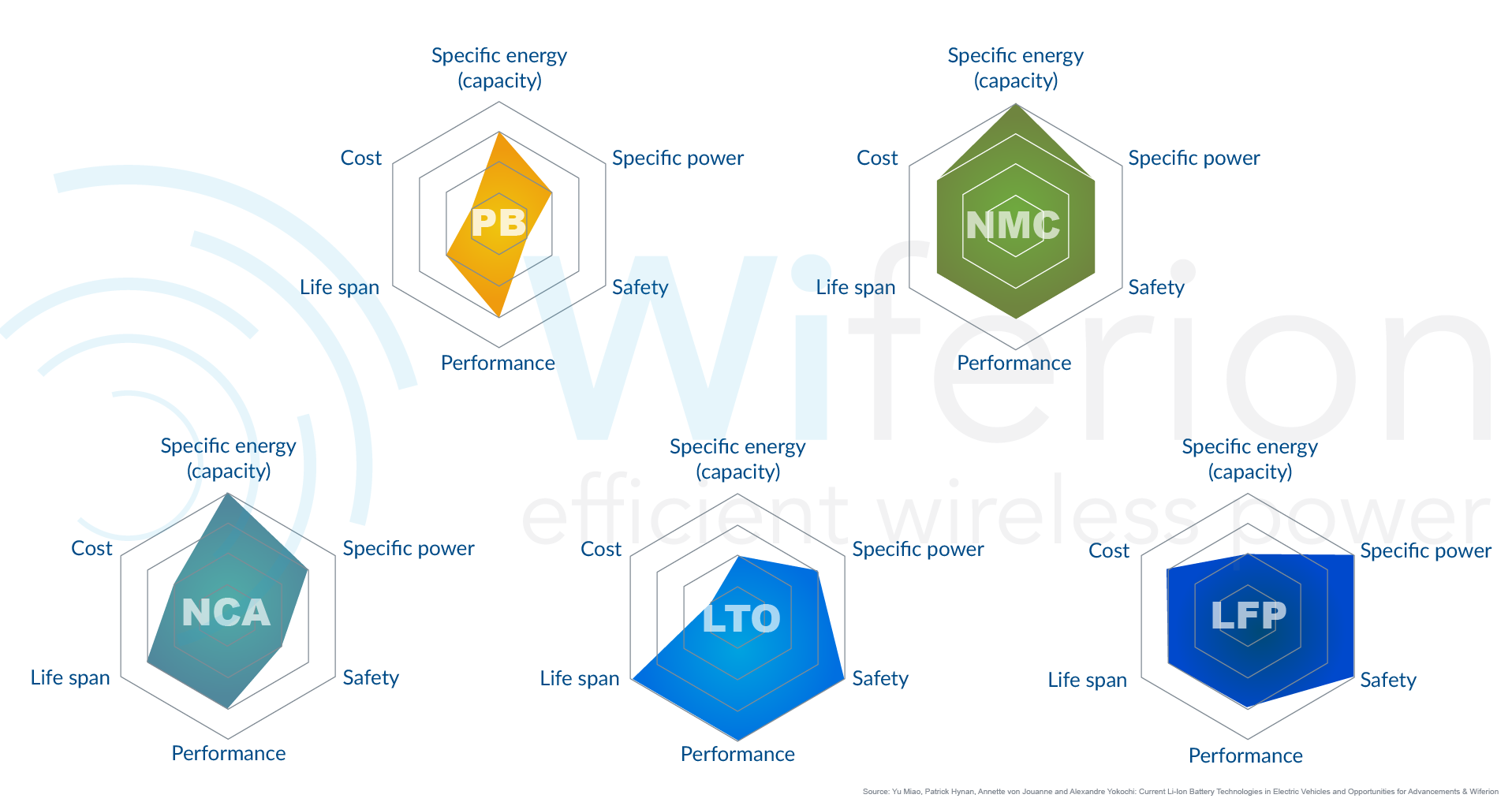
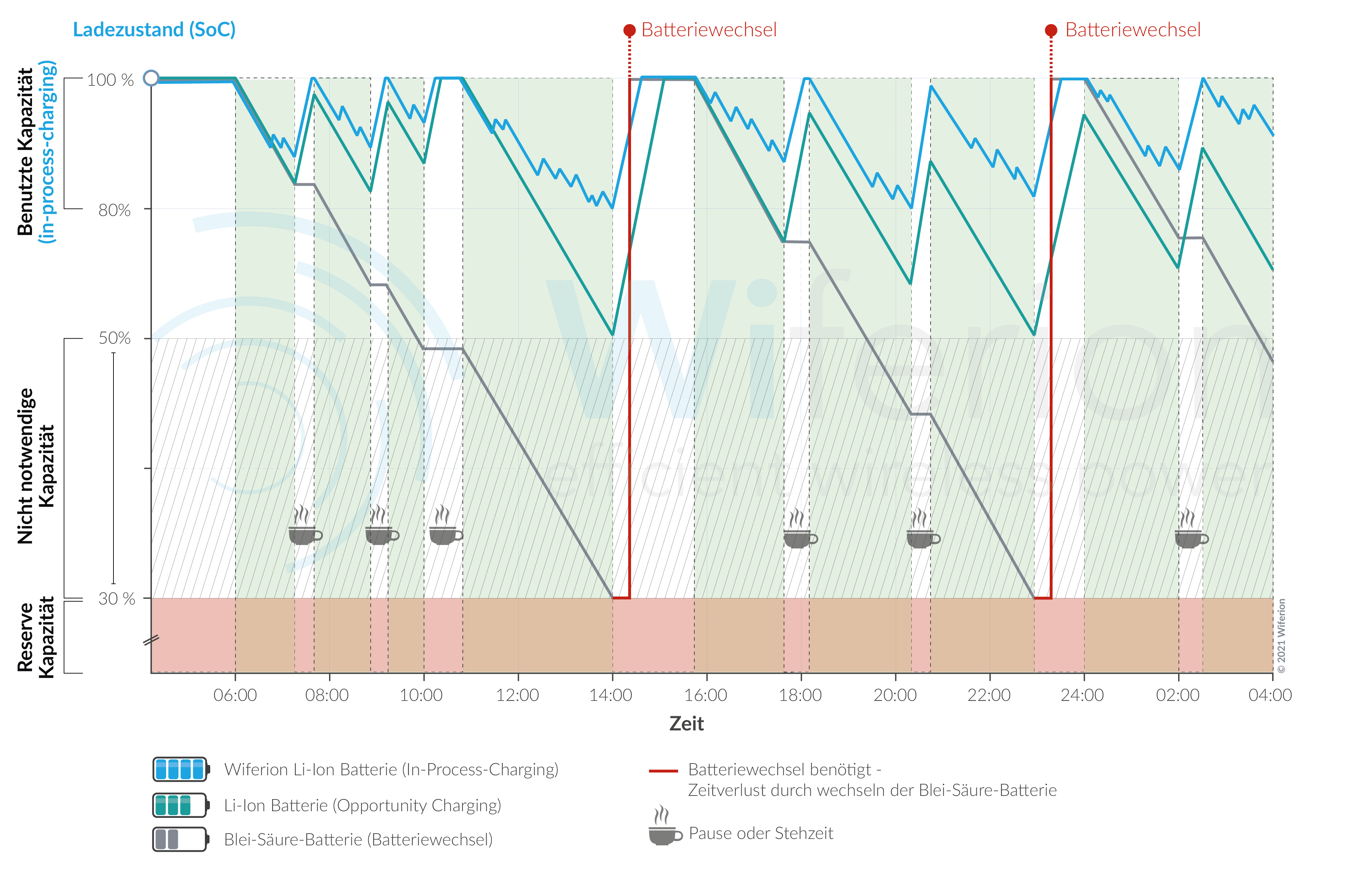
Die Total Cost of Ownership (TCO) der Lithium-Batterien verbessert sich signifikant
Die Lebensdauer hängt immer auch noch von der Art der Ladung und Pflege ab. Zu dem unterscheidet man bei Lithium von Vollzyklen und Ladezyklen. Bei Lithium zählen die Auf- und Endladung der gesamten Batteriekapaziät als ein Zyklus. Dabei werden die Kapazität bei mehreren Ladeschritten summiert. Bei Blei-Säure-Batterien hingegen ist jeder einzelne Ladeprozess EIN Zyklus – auch wenn nur ein Teil der nutzbaren Kapazität geladen oder entladen wird.
Damit überdauern die Energiespeichersysteme sogar die Lebenszeit der eingesetzten Fahrzeuge und sind daher eine besonders nachhaltige Investition.
Für die industrielle Anwendungen geeignete Zelltechnologien wie LFP und LTO erlauben es, FTS und Fahrzeuge ohne Batteriewechsel über die gesamte Lebensdauer zu betreiben. Auch die Total Cost of Ownership (TCO) der Lithium-Batterien verbessert sich gegenüber den Blei-Säure-Batterien signifikant.
Neben der Lebensdauer ist die Ladefähigkeit der Technologien ideal, um kurze Stopps im Betriebsablauf für die Versorgung mit Strom zu nutzen. Dadurch lassen sich die früher zusätzlich benötigten Zeiten für Ladevorgänge eliminieren.
Für die Aufladung der leistungsstarken Batterien stehen verschiedene FTS Ladegeräte zur Verfügung. Diese unterscheiden sich hinsichtlich Wirtschaftlichkeit, Wartungsaufwand, Flexibilität sowie Arbeitsschutz. Wie genau finden Sie hier in unserem Batterieladegerät Vergleich für verschiedene Batterietypen.
Kabelgebundene Batterieladegeräte mit Steckverbindungen
Kabelgebundene Batterieladegeräte mit Steckverbindungen
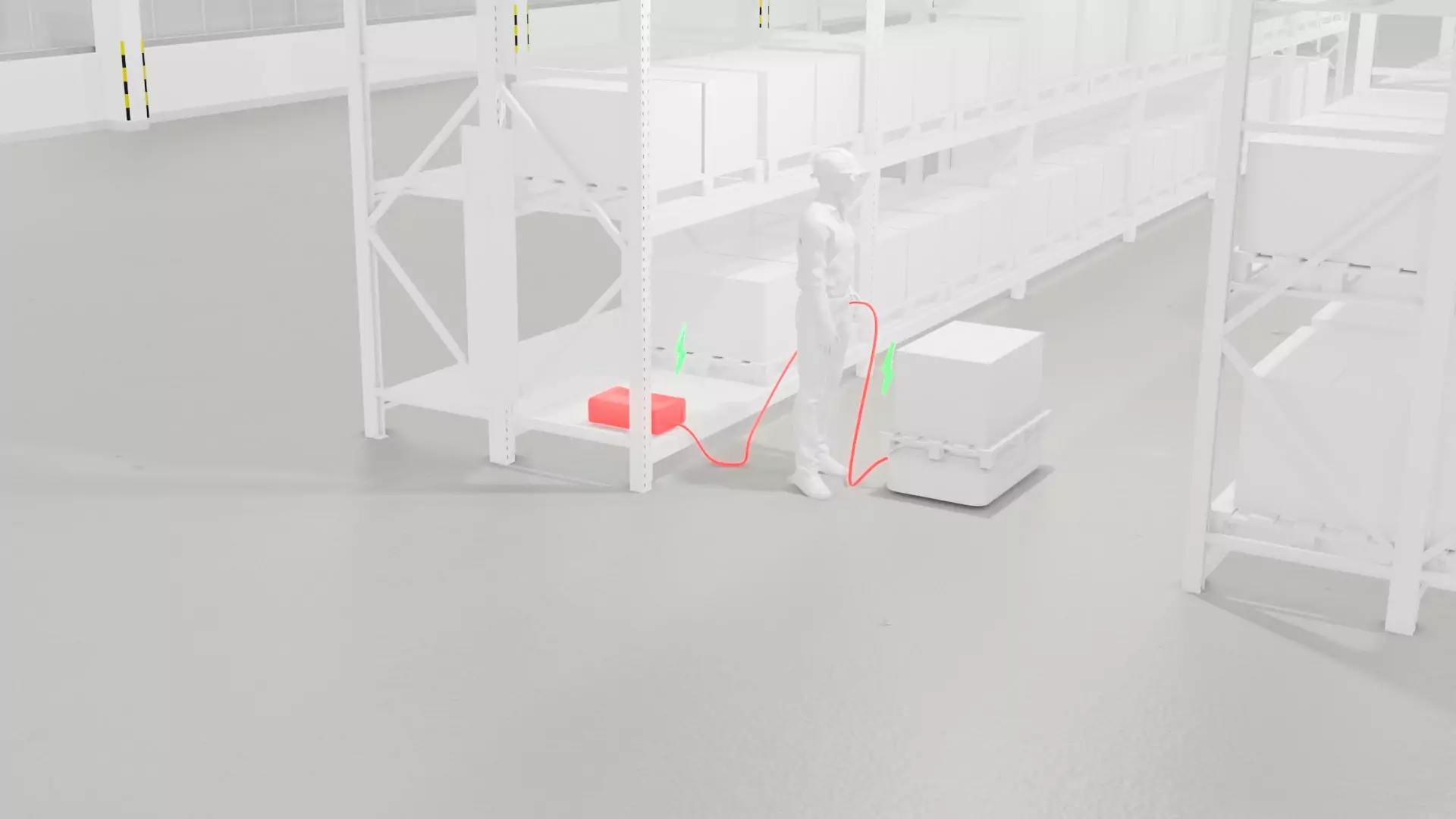
Steckverbindungen sind der Klassiker
Kabelgebundene Steckverbindungen sind der Klassiker, wenn es um Batterien aufladen geht. Dabei schließen Mitarbeiter die Fahrzeuge bei niedrigem Energiestand an das Batterieladegerät an, in längeren Pausen oder nach Schichtende an das Ladegerät an, bis die Batterie wieder aufgeladen sind.
Aus Gründen des Arbeitsschutzes befinden sich die Ladepunkte häufig nicht in unmittelbarer Nähe der Produktionsbereiche. Die Stapler müssen meist zu weiter entfernten Ladezonen fahren um leere Batterien zu verhindern. Diese befinden sich manchmal sogar außerhalb der Produktionshalle. Der Weg durch das Lager ist nicht wertschöpfend. Zudem fehlen die Fahrzeuge während des Ladevorgangs im Produktionsprozess.
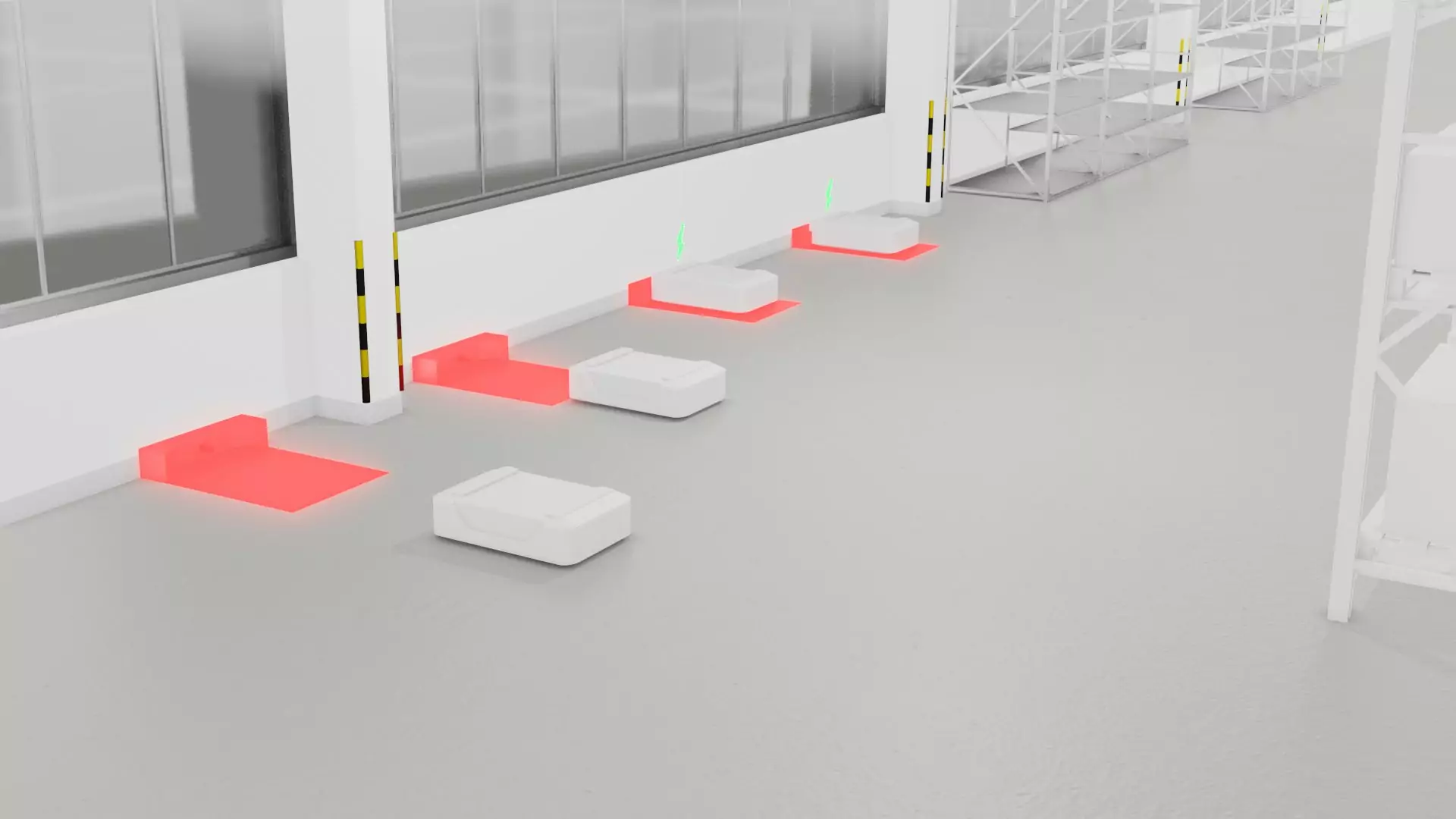
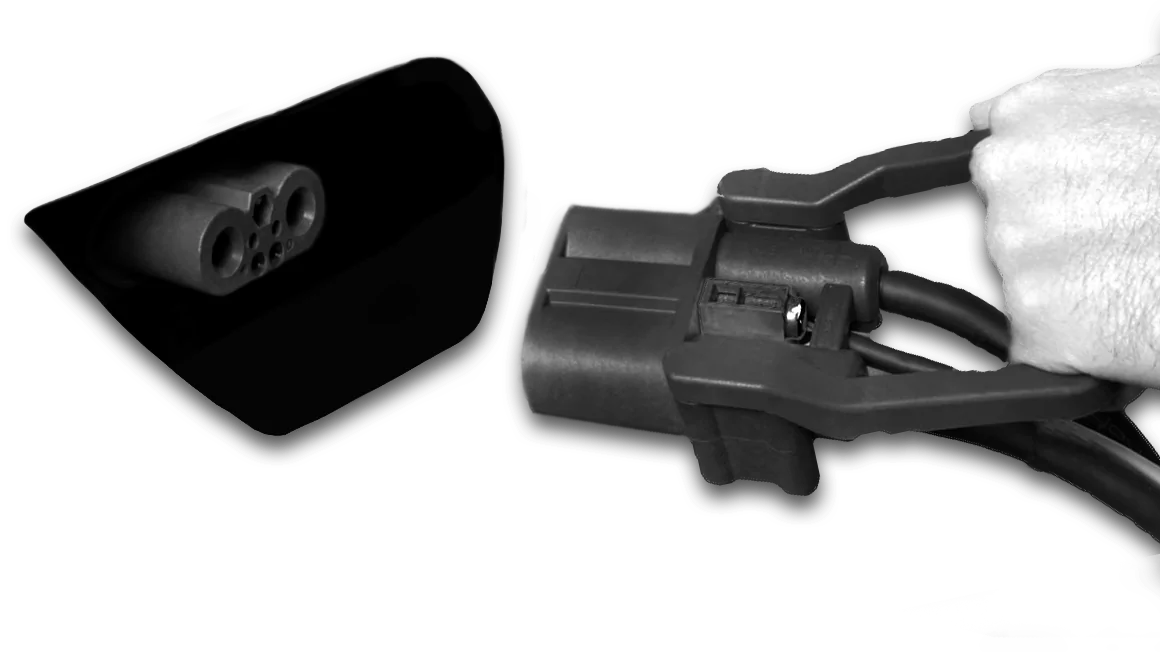
Beschädigte Ladekabel sind Kostentreiber
Trotz ihrer vermeintlichen Robustheit sind kabelgebundene Batterieladesysteme wartungsintensiv und störanfällig. Bei unsachgemäßem Gebrauch entstehen Gewaltschäden und weitere Sicherheitsprobleme wie abgebrochene Pins und abgerissene Kabelenden. Beschädigte Ladekabel müssen regelmäßig ausgetauscht werden, sind oft ein versteckter Kostentreiber und stellen ein weiteres Gefahrenpotential dar.
Auch vergessen Mitarbeiter immer wieder die Stecker der Kabelladegeräte an die Fahrzeuge anzuschließen. Ein zu niedriges Energielevel für nachgelagerte Aufgaben ist die Folge.
Vergessene Stecker und längere Ladephasen
Werden mit dieser Technik automatisierte Ladekonzepte realisiert, erhöht sich die Anzahl der Steckvorgänge, wodurch zu erwarten ist, dass dieses Problem weiter an Gewicht gewinnt.
Da die Fahrzeuge im Betrieb nicht mit Strom versorgt werden fällt das Energielevel der Batterien im Betrieb kontinuierlich ab und muss durch längere Ladephasen ausgeglichen werden. Deswegen müssen die teuren Batterien deutlich größer ausfallen, damit die Stapler immer über ausreichend Energie verfügen.
Zudem schlagen die erhöhten Leistungspreise der Lastspitzen zu Buche, wenn die gesamte Flotte nach Schichtende aufgeladen wird.
Letztlich lassen sich kabelgebundene Ladekonzepte nur schlecht automatisieren und die FFZ, als auch fahrerlosen Transportsystemen (FTS) sind während des Ladeprozesses nicht produktiv. Desweiteren für verschiedene Batterietypen auch jeweils ein eigenes Batterieladegerät benötigt.
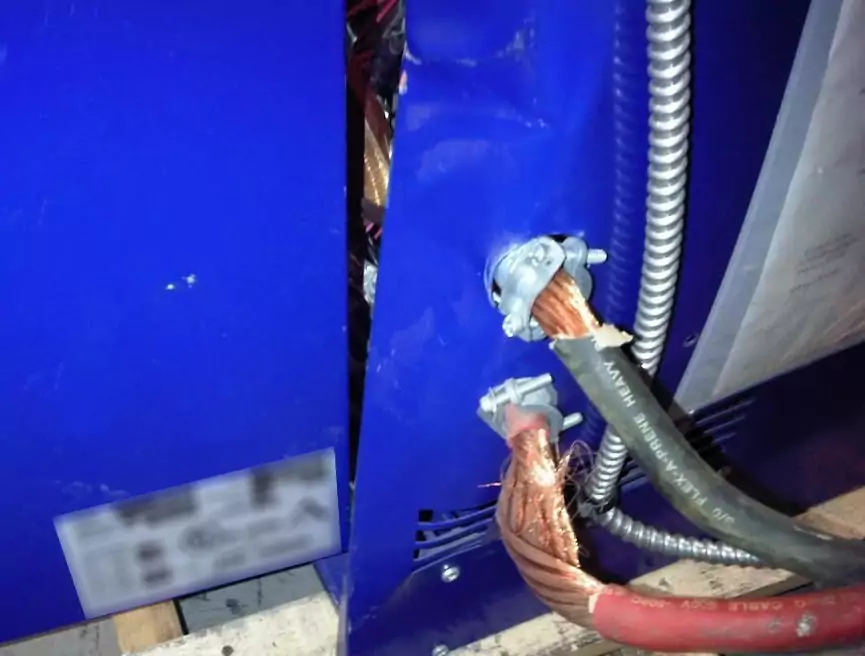
Vorteile des Ladens mit Kabel
- hohe Effizienz
- relativ kostengünstig in der Investitionsphase
- etablierte Technologie
Nachteile des Ladens mit Kabel
- hoher Wartungsaufwand
- schlecht zu automatisieren
- FFZ fehlen im Workflow
- Benötigt große Batterien
- Ladeeinheit benötigt Platz und ist deshalb oft nicht gut in der Anlage verteilbar…
Interessiert an unseren Batterieladetechniken?
Kontaktieren Sie uns!
Kontaktieren Sie uns!
Batterieladegeräte mit Schleifkontakten
Batterieladegeräte mit Schleifkontakten
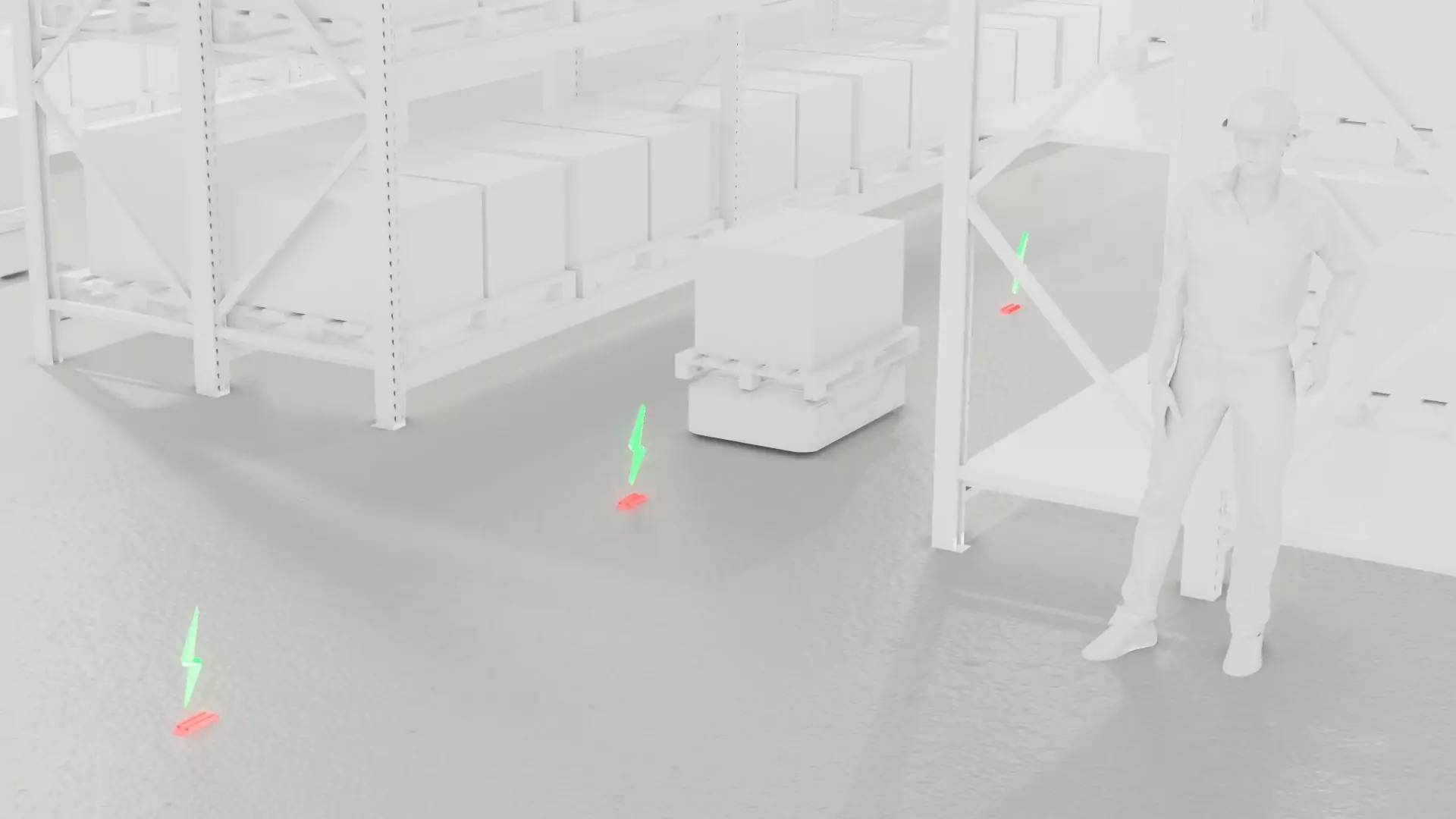
Großer Bill of Material mit Schleifkontakten
Bei der Stromversorgung der Batterie von FTS oder automatisierten FFZ kommen häufig Schleifkontakten zum Einsatz. Hierbei werden stationäre Schleifkontakte in der Lagerumgebung fest verbaut und ein Gegenkontakt an den Fahrzeugen montiert.
Dieses Konzept als FTS Ladegerät ist oft wegen seiner anfänglichen Einfachheit verlockend. Betrachtet man das Gesamtkonzept aus Ansteuerung zum Spannungsfreischalten der Kontakte, mechanischer Absenkvorrichtung und zusätzlich notwendiger Kommunikation für die Ladeprozesssteuerung, nimmt die Komplexität und damit die BOM (Bill of Materials) schnell zu.
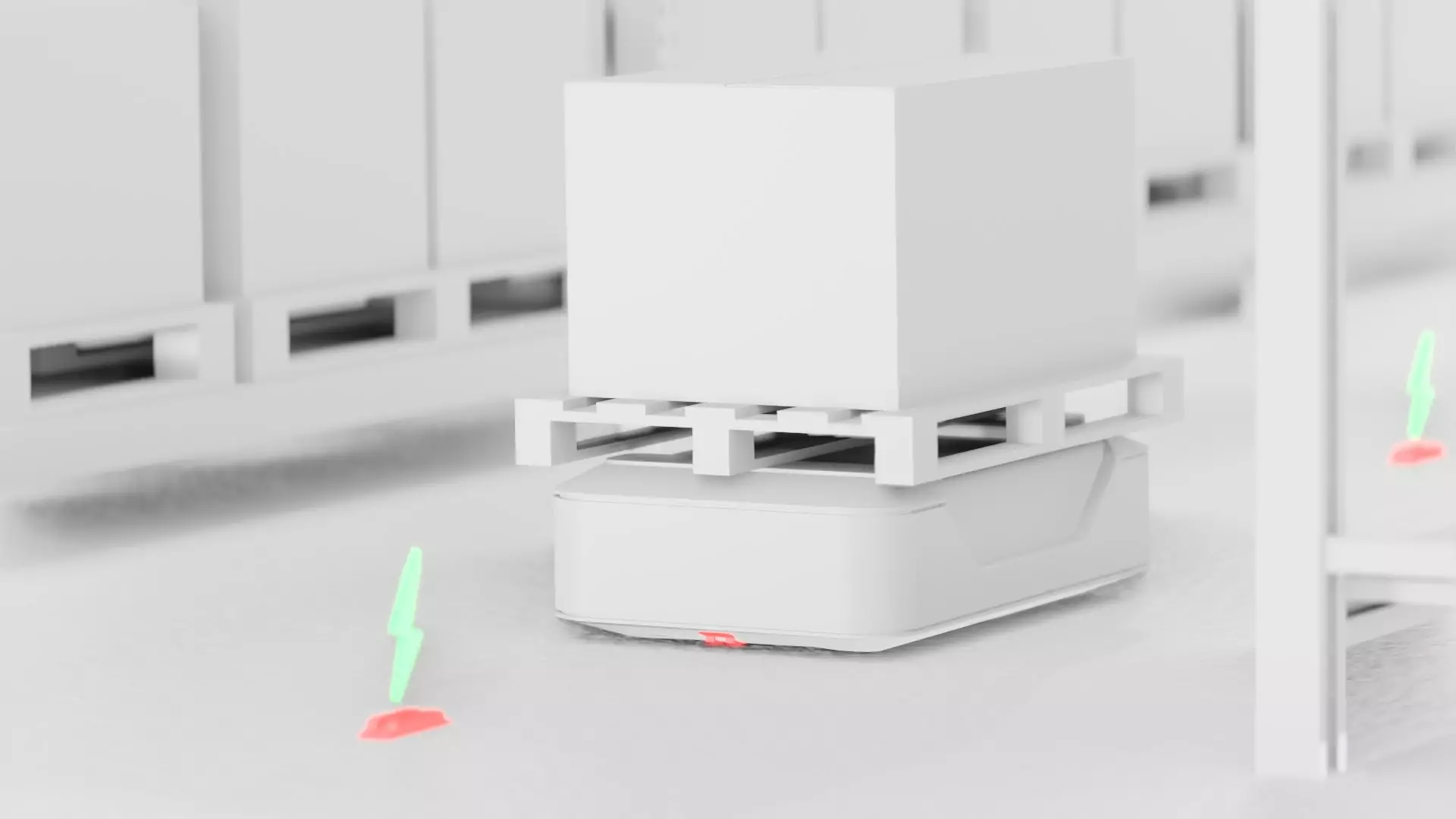
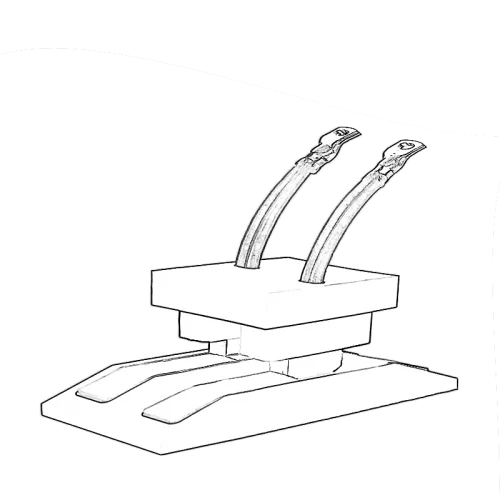
Positionierung bei Ladekontakten muss exakt sein
So führen die Schaltrelais immer wieder zu Problemen. Zum Beispiel bei einer nicht korrekten Ansteuerung oder einem Verkleben der „Kontakte“. Funktioniert das Ladesystem nicht korrekt, kann es nach der Beendigung des Ladeprozesses zu Funkenbildung kommen.
Für die Systemverfügbarkeit ist es außerdem wichtig, dass die Positionierung exakt ausgeführt wird. Wie der Kontaktvorgang aufgebaut wird, entscheidet darüber, ob Oxidschichten vor dem Laden entfernt werden und Einbrandstellen vermieden werden können.
Die Konstruktionen der Ladestationen sind bei höheren Strömen komplex und teuer
Letztlich handelt es sich bei Kontakten um Verschleißteile, was bei einem Opportunity-Ladekonzept zu mehr Aufwänden für Bauteilwechsel führen kann. Durch den kontinuierlichen Abrieb der entsteht Kupferstaub der die Ladestation und die Produktionsumgebung verschmutz. Die feinen Kupferartikel schweben in der Luft und stellen eine Gesundheitsgefährdung für die Mitarbeiter dar, die sich permanent in der Halle aufhalten.
In Produktionslinien sind auf dem Boden montierte Ladekontakte zudem hinderlich und werden aufgrund der Stolpergefahr für Mitarbeiter nicht gerne gesehen. Deshalb wird der Ladepunkt von der Batterieladetechnik mit Schleifkontakten aus Gründen des Arbeitsschutzes nicht in unmittelbarer Nähe der Produktionsbereiche angebracht.
Die Konstruktionen der Ladestationen sind bei höheren Strömen komplex und teuer. Denn große Energieübertragung werden erst durch starke Kontaktkräfte möglich. Diese müssen wiederum von den Ladestationen abgefangen werden. Damit ist ein größerer Wartungsaufwand ist notwendig, um einen reibungslosen Betrieb sicherzustellen. Bei leichten Fahrzeugen entsteht so auch eine Limitierung beim Ladestrom bei allen Arten von Batterien.
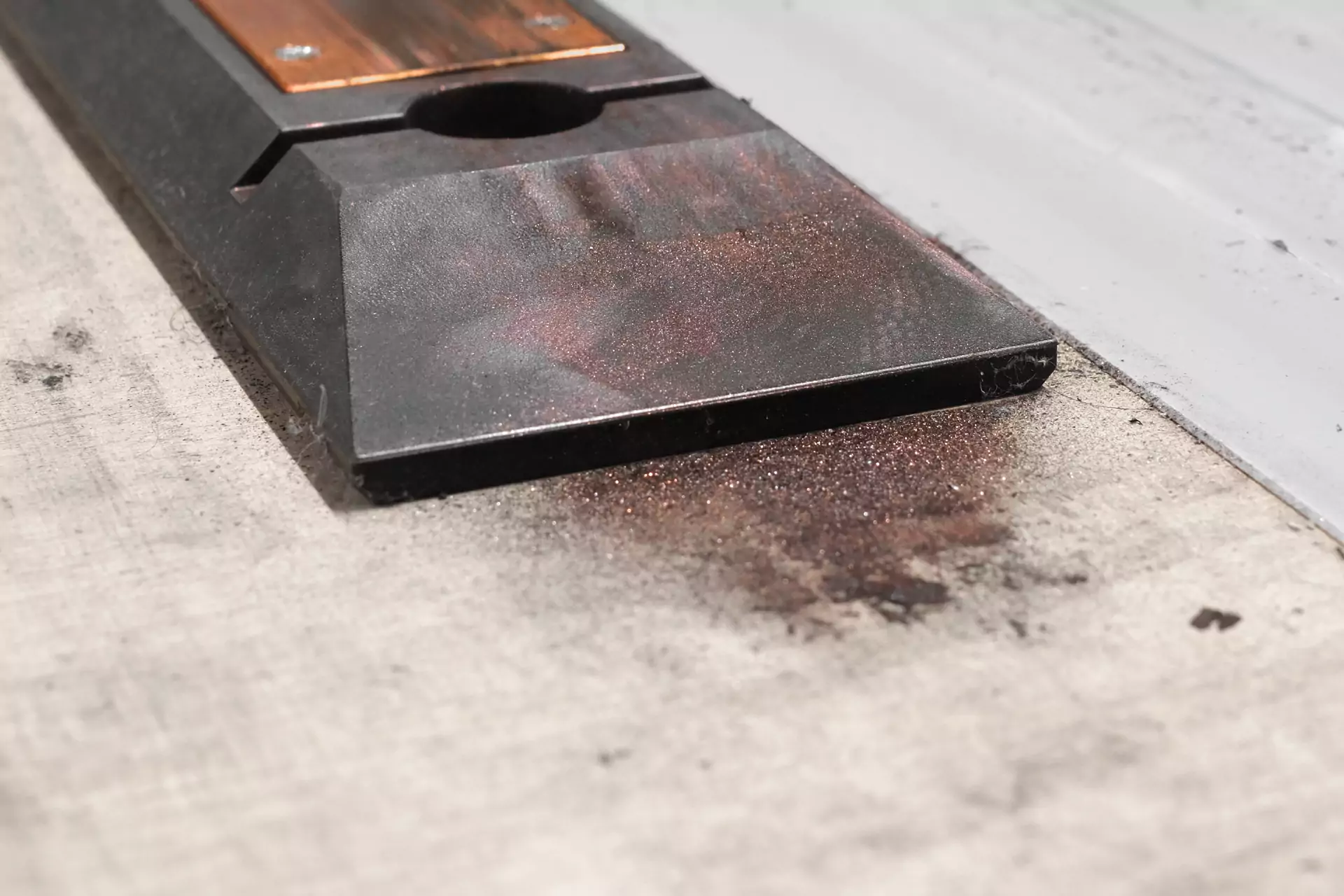
Vorteile des Ladens mit Schleifkontakten
- Automatisierbar
- eingeschränkte Verfügbarkeiten
- Erst Integration einfach
Nachteile des Ladens mit Schleifkontakten
- Wartungsintensiv
- Komplexe Steuerung notwendig
- Eingriffe in die Infrastruktur
- Stolpergefahr für Mitarbeiter
- Abnutzung der Ladekontakte
- FFZ fehlen im Workflow
- Genaue Positionierung nötig
Interessiert an unseren Batterieladetechniken?
Kontaktieren Sie uns!
Kontaktieren Sie uns!
Batterielade Technik mit induktiven Leiterlinien im Boden
Batterieladetechnik mit induktiven Leiterlinien im Boden
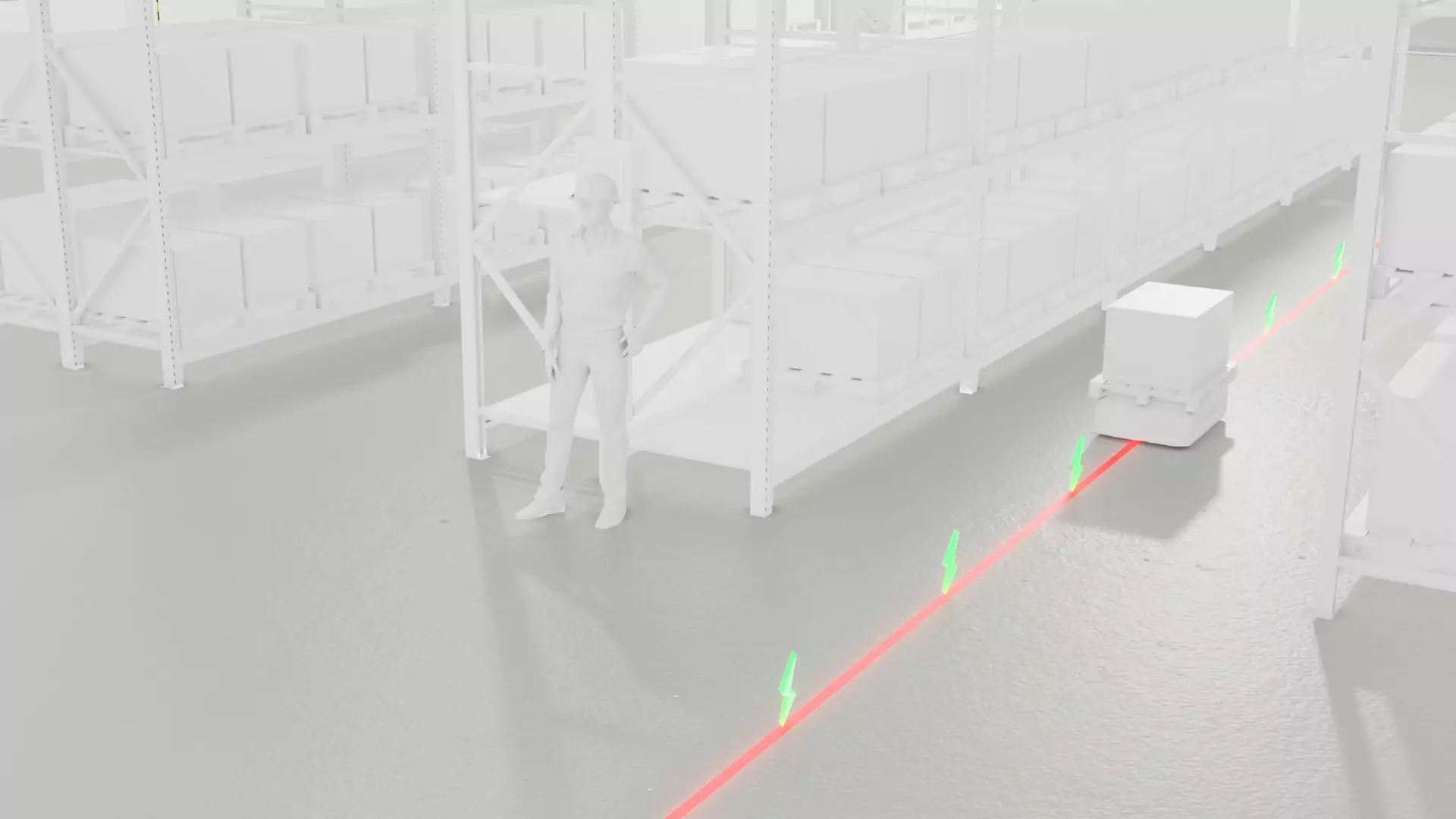
Mit Leiterlinien umfangreiche Eingriffe in die Infrastruktur notwendig
Das Laden der Batterie über Leitliniensysteme ist aufgrund seiner kostenintensiven Komplexität weniger verbreitet als das Laden über Ladekontakte. Bei diesem Industrie Ladegerät bewegen sich automatisierte Fahrzeuge wie FTS auf vorgegebenen Fahrwegen mit integrierten Stromleitern.
Das Akkus Laden erfolgt induktiv. Allerdings sind umfangreiche Eingriffe in die Infrastruktur nötig, um die Leiter im Boden zu installieren. Das System ist sehr kosten- und wartungsintensiv.
Die Leitungen werden in einer Projektphase in die Anlage integriert und mit Hilfe zusätzlicher Komponenten entlang der Fahrwege auf den Einspeisepunkt abgestimmt und festgelegt. Für die Implementierung sind weitgehende Eingriffe in die Infrastruktur der Gebäudesubstanz notwendig.
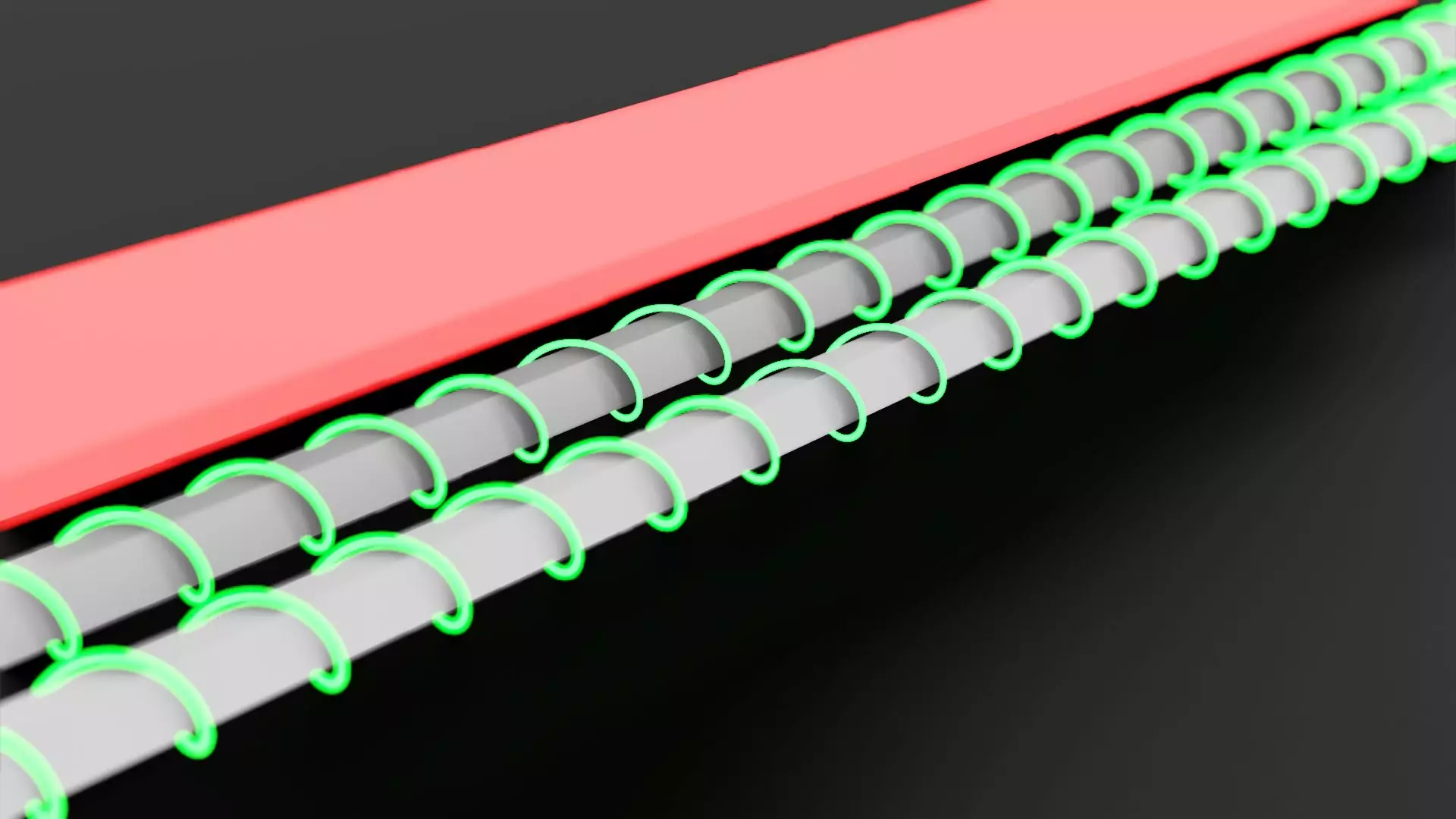
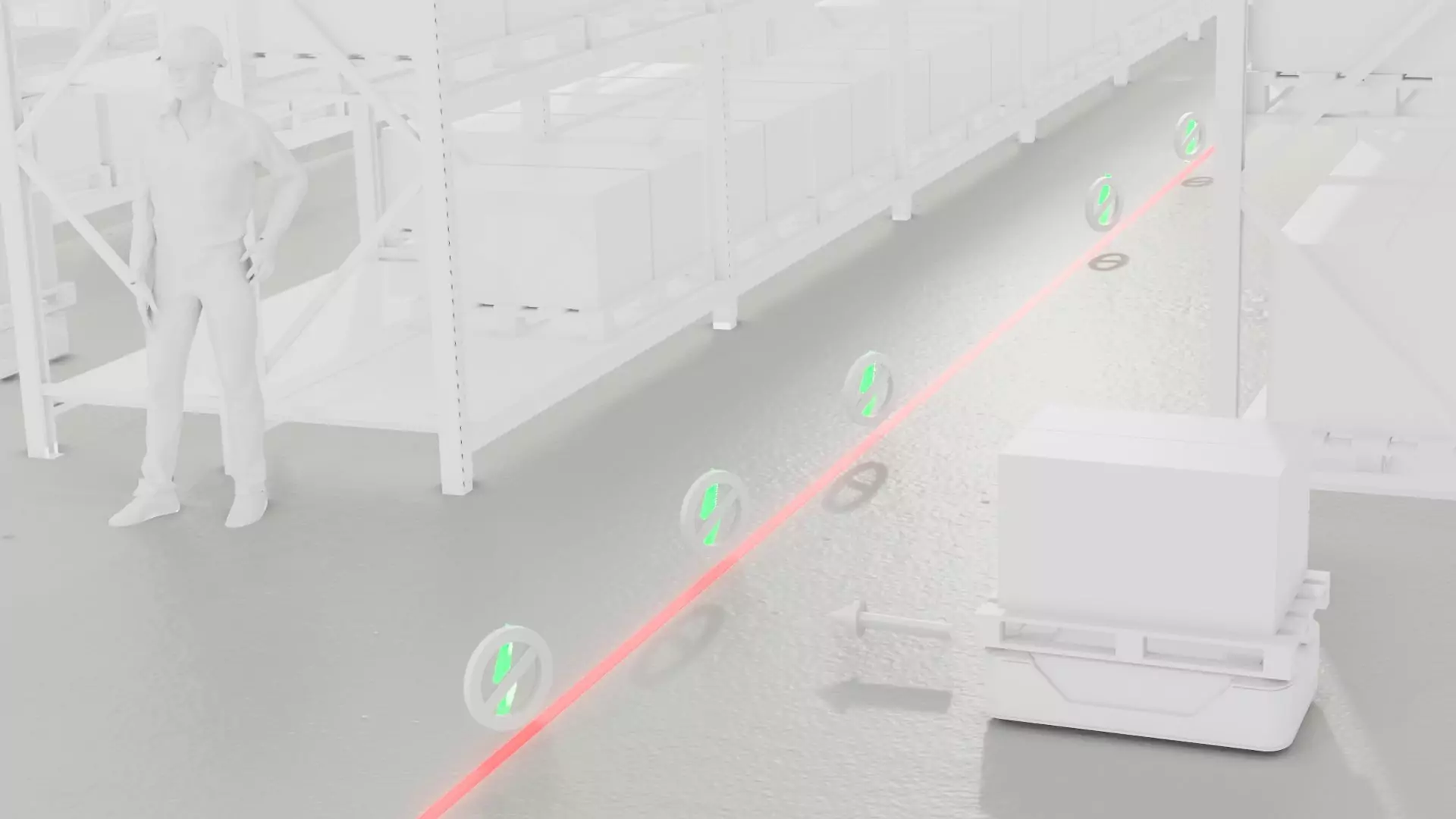
Leiterlinien haben ein durchgehendes Magnetfeld
So muss der Hallenboden aufgefräst werden, damit die Leiterlinien verlegt werden können. Leitliniensysteme sind dadurch sehr unflexibel. Die Fahrtrichtung der FTS ist festgelegt. Nur mit größerem Aufwand lässt sich diese an veränderte Anforderungen anpassen. Jede Fuhrparkerweiterung oder Fahrwegsänderung wird beim Batterie Ladegerätes zur Herausforderung.
Linienleiter erzeugen ein permanentes Magnetfeld. Bei der Installation der Ladegeräte ist eine genaue Analyse der Infrastruktur vor Ort notwendig.
Nur so lassen sich etwaige Wechselwirkungen mit Bodenarmierungen durch die permanenten Magnetfelder um die Leitung ausschließen. Ansonsten entstehen beträchtliche Verluste in der Armierung und der Boden erwärmt sich. Ändern sich die Anforderungen an den Arbeitsprozess oder soll der Fuhrpark erweitert werden, wird eine erneute Projektphase notwendig.
Leiterlinien sind permanent aktiv und es ist keine Kommunikations zwischen den Fahrzeugen möglich
Da die Leiter großflächig verteilt werden, bewegen sich jedoch nicht nur die Fahrzeuge auf den Leitern. Auch Mitarbeiter müssen teilweise während der gesamten Arbeitszeit auf den Leitern im Magnetfeld agieren.
Eine Kommunikation zwischen Leitung und den Komponenten im Fahrzeug ist systembedingt nicht möglich. Deswegen müssen die Leitungsströme zu jedem Zeitpunkt aufrechterhalten werden, was die Effizienz der Ladegeräte limitiert.
Bei Systemen mit diskontinuierlichen induktiven Strecken sind jedoch selten alle Fahrzeuge auf dem Streckenabschnitt. Die Einspeiseleistung ist meist stark überdimensioniert und die Leitersysteme sind permanent aktiv. Je nach Auslegung und Einsatzanzahl der Fahrzeuge bewegen sich gute Leitliniensysteme in einem Gesamtwirkungsgrad von rund 60%.
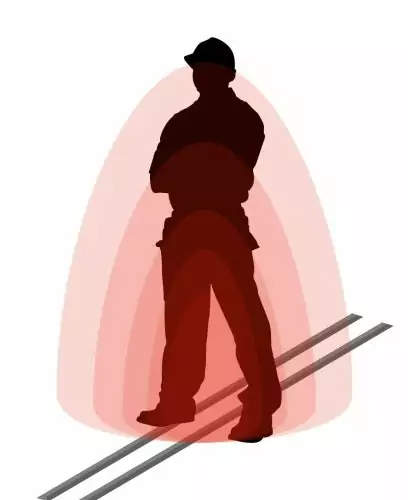
Vorteile des Ladens mit induktiven Leiterlinien
- Automatisierter Ladevorgang
Nachteile des Ladens mit induktiven Leiterlinien
- Kostenintensiv
- Aufwändige Planung und Realisierung
- Schlechter Wirkungsgrad
- Unflexibel
- Eingriffe in Infrastruktur notwendig
- Nicht ungefährlich für einige Randgruppen
Interessiert an unseren Batterieladetechniken?
Kontaktieren Sie uns!
Kontaktieren Sie uns!
Induktive Punkt Ladegeräte
Induktive Punkt Ladegeräte
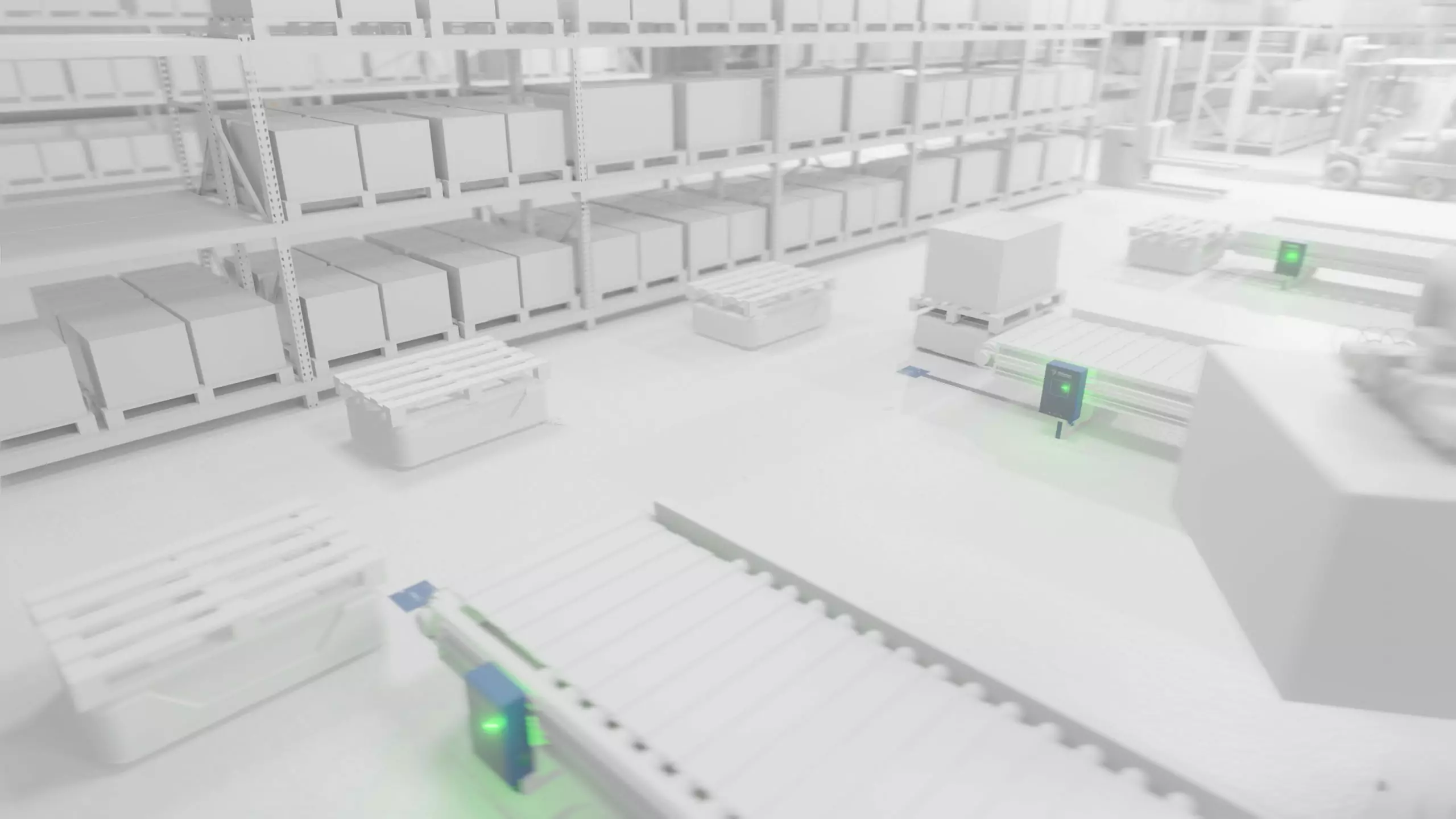
Ein neuer Ansatz für das Batterien laden von Flurförderzeugen sind induktive Punktladesysteme. Diese werden aufgrund ihrer zahlreichen Vorteile für die Stromversorgung von Flurförderzeugen und FTS immer beliebter. Dabei wird nach dem Prinzip der magnetischen Induktion Energie automatisch, hocheffizient und kontaktlos übertragen.
Vollautomatisches Laden der Fahrzeug Batterie
Anstatt zu einer festen Batterieadestation zu fahren, werden die Fahrzeuge beim sogenannten „In-Process-Charging“ während ihres Workflows an häufig frequentierten Punkten im Lagert vollautomatisch zwischengeladen. Die Fahrzeuge können so ihre Transportaufgaben im 24/7-Dauerbetrieb erledigen, ohne die logistischen Prozesse für Ladepausen abzubrechen. Hierdurch entfallen unproduktive Stillstandzeiten, weshalb sich die Verfügbarkeiten von FTS, AMR und FFZ um bis zu 30 % erhöhen.
Sobald ein Fahrzeug das Ladepad eines induktiven Punktladegeräts erreicht hat, beginnt der Ladevorgang automatisch innerhalb 1 Sekunde. Somit ist das gesamte System in kürzester Zeit betriebsbereit. Dabei ist es egal, ob es sich um einen Stapler, mobilen Roboter oder fahrerloses Transportsystem handelt. Auch der Hersteller oder die verbaute Batterie spielen keine Rolle, solange die Fahrzeuge über eine Empfangselektronik verfügen.
Eine Ladestation kann unterschiedliche Batterietypen, wie z.b.
- Gel Batterien
- AGM Batterien
- Lithium Batterien
und viele mehr, mit 24 bis 48 Volt bedienen. Die Ladekennlinie am Fahrzeug ist frei programmierbar und passt sich dynamisch den jeweiligen Batteriestatus an. Somit sind alle Batterien geeignet.
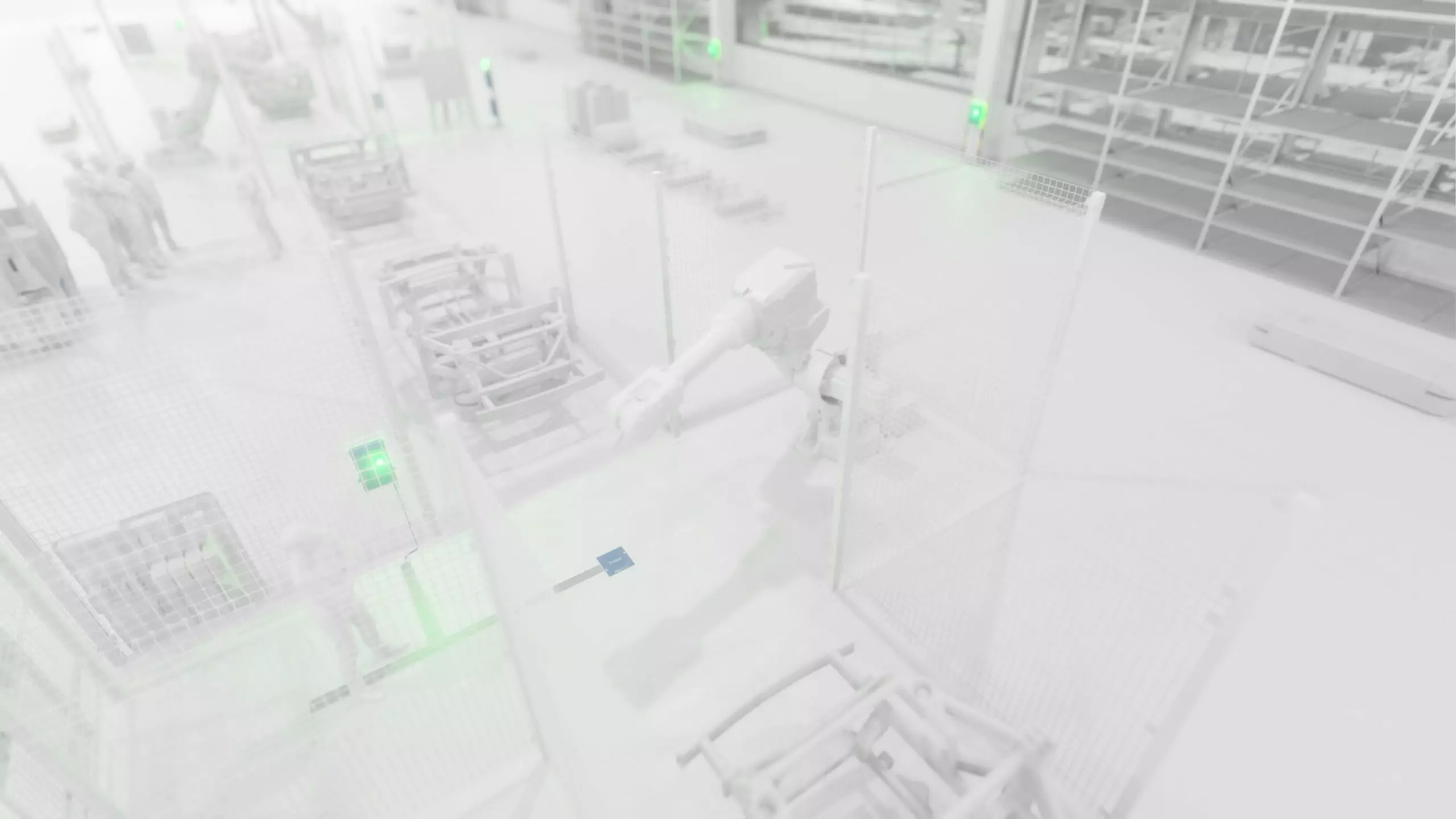
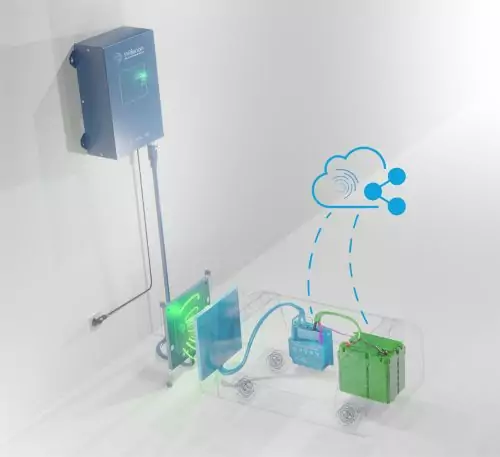
Einfache Installation und Integration der induktiven Ladegeräte
Industrielle Induktive Ladegeräte wie die des deutschen Herstellers Wiferion bestehen aus einer Wallbox und einem Ladepad, das sich flexibel an geeigneten Stellen im Logistik- und Produktionsumfeld installieren lässt. Im Fahrzeug wird die Empfangselektronik mit Empfängerspule, mobiler Ladeeinheit und Energiespeicher verbaut.
Vorteile induktiver Punktladegeräte gegenüber herkömmlicher Batterieladetechnik
Was induktive Batterieladegeräte auszeichnet: Sie verbrauchen nur dann Strom, wenn die Ladevorgänge stattfinden. Der Wirkungsgrad induktiver Schnellladesysteme liegt bei bis zu 93 % (Wiferion etaLINK). Damit ist der Wirkungsgrad genau so effizient wie der der besten kabelgebundenen Ladegeräte und deutlich höher als die Wirkungsgrade der Leitliniensysteme.
Das Laden erfolgt vollautomatisch ohne Kontakt. Der Ladeprozess kann dabei von der Batterie bestimmt werden, dadurch wird sie immer im optimalen Arbeitspunkt betrieben (z.b. bei Be- und Entladestationen) und ungewollte Abschaltungen wie z. B. durch Übertemperatur der Batterie werden vermieden. Somit sind auch unterschiedliche Spannungen am gleichen Ladegerät problemlos umsetzbar.
Im Gegensatz zu Batterieladegeräten mit Steck- oder Schleifverbindungen werden daher keine extra Bereiche benötigt, in denen die Batterie von FFZ geladen wird. Außerdem sind die Fahrzeuge kontinuierlich produktiv und mit wertschöpfenden Aufgaben beschäftigt.
Sehen Sie hier, wie SMA Solar Technology AG Ihre FFZ mit dem Induktiven Ladesystem retrofittet hat.
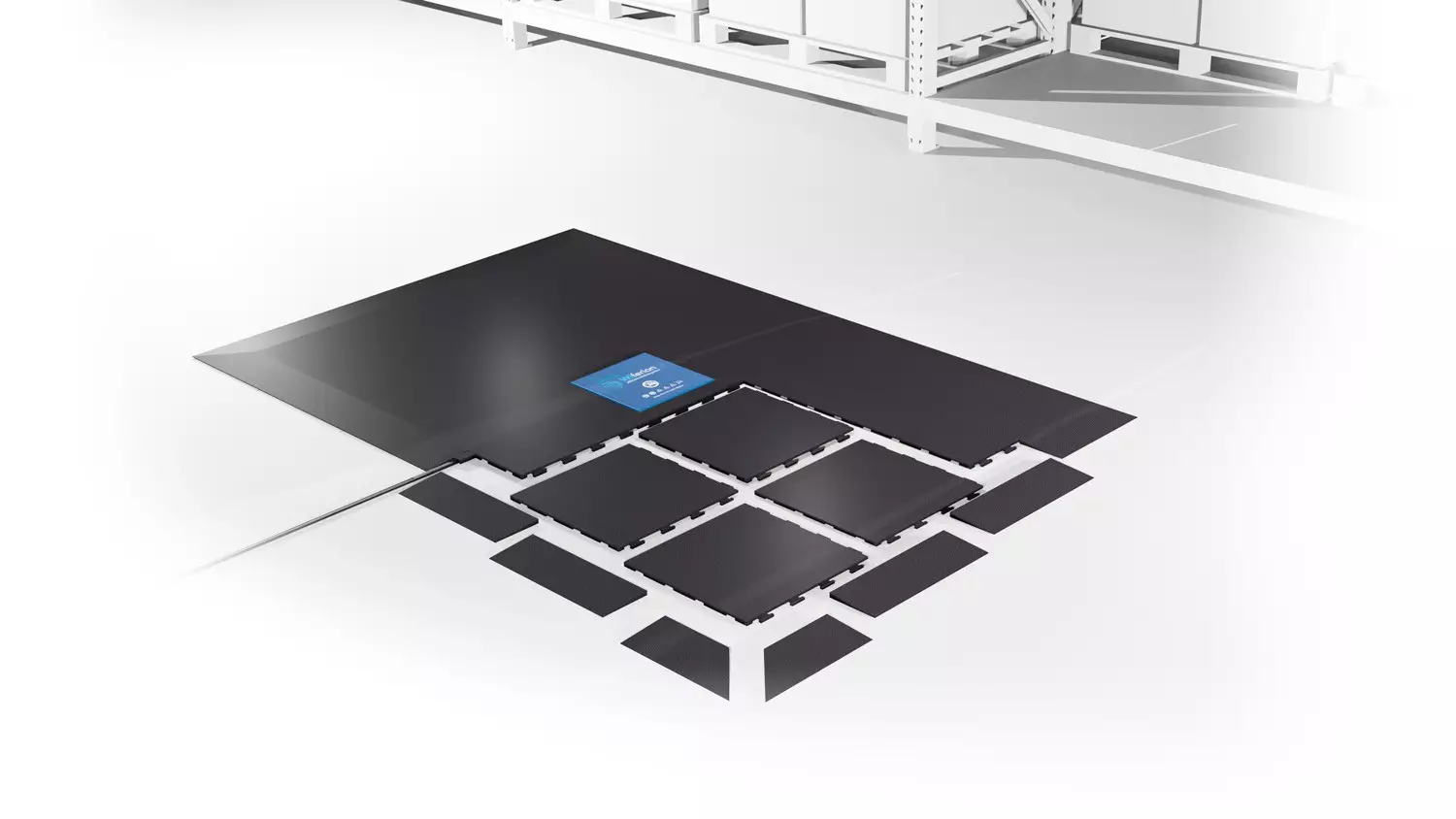
Vertikale oder horizontale Installation der induktiven Ladepads
Da ein induktives Ladegerät ohne mechanische Schleifkontakte auskommt, ist es praktisch wartungsfrei. Probleme der herkömmlichen Ladeprozesse mit oxidierten Steckern oder gebrochenen Kabeln gehören der Vergangenheit an.
Die Komponenten sind nur über das Magnetfeld miteinander verbunden und daher für den langjährigen Dauereinsatz geeignet.
Induktive Punktladesysteme lassen sich einfach bedienen und nahezu überall installieren – an Wänden, auf dem Boden, auf Fahrwegen, an Abstellplätzen oder Be- und Entladestationen.
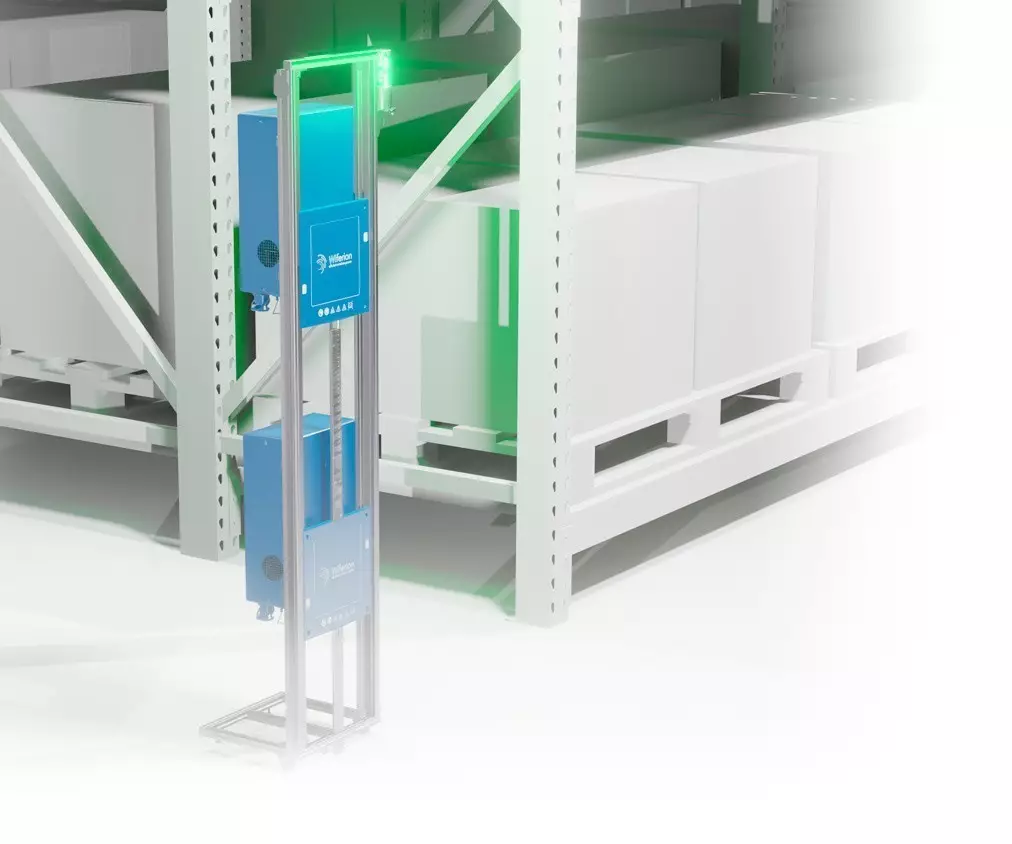
Sicherheit und Zuverlässigkeit erhöht sich mit kontaktlosem, induktiven Punkt Ladesystemen
Für Ladesysteme mit Steck- und Schleifverbindungen müssen immer wieder aufwändige Peripheriebeschaltungen und Schutzeinrichtungen installiert werden, um die Sicherheit für Mitarbeiter und Anlagen zu gewährleisten. Da es bei einem induktiven Ladegerät keine offenen Kontakte gibt, steigt die Arbeitssicherheit enorm an.
Zudem ist die Batterieladetechnik wetterfest. Die Umgebungsbedingungen haben keinen Einfluss auf die Funktionsweise. Feuchtigkeit, Dreck oder Staub können dem System nichts anhaben. Es handelt sich um ein eingekapseltes System mit IP 65 Zertifizierung. So wird erstmalig auch die Stromversorgung von Fahrzeugen im Außenbereich möglich.
Bei herkömmlichen Systemen kann die Integration in Lagerabläufe oft Wochen oder sogar Monate dauern. Für die Implementierung einer Automatisierung mit der Wireless Charging-Technologie wie der von Wiferion dagegen sind bei den meisten Einsätzen keine aufwändigen Infrastrukturmaßnahmen erforderlich
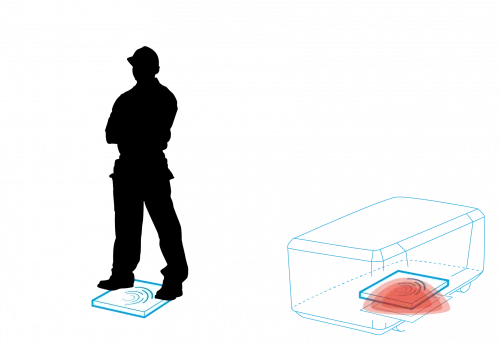
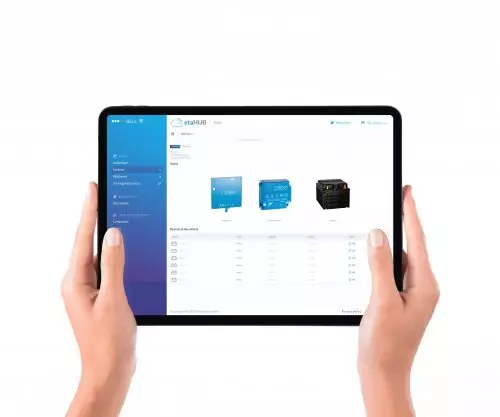
Flexibel Integrieren und Livedaten des Fahrzeugs jederzeit auslesen
Die Automatisierungslösung mit den modularen Batterieladegeräten lässt sich schnell an Veränderungen im Ablauf oder neue Anforderungen anpassen. Ladeeinheit und Empfängerspule können innerhalb kürzester Zeit am Fahrzeug installiert werden. Da mobile Elektronik und Empfängerspule getrennte Bauteile sind, lassen sich zahlreiche Anbringungsvarianten realisieren.
Im Gegensatz zur herkömmlichen Batterielade Technik bieten induktive Punktladesysteme erstmals die Möglichkeit, alle relevanten Live-Informationen der Batterie Ladung auszuwerten. Mithilfe einer integrierten CAN-Schnittstelle können Daten wie Energielevel, Betriebszeiten und Fahrzeugzustände in Echtzeit abgerufen werden. Die Prozesssicherheit lässt sich so um ein Vielfaches steigern und entladene Batterien gehören der Vergangenheit an.
Induktive Batterieladegeräte mit Punkt Ladung sind im Vergleich zu kabelgebundenen Ladelösungen in der Anschaffung teurer. Diese Kosten amortisieren sich jedoch aufgrund der vielen Vorteile schnell. Gegenüber den mit Eingriffen in die Infrastruktur verbundenen Lösungen mit Schleifkontakten und Leiterlinien, sind die Punktladesystem deutlich günstiger.
Interessiert an unseren Batterieladetechniken?
Kontaktieren Sie uns!
Kontaktieren Sie uns!
Häufig gestellte Fragen zur Batterieladetechnik
Welches FTS Ladegerät ist das beste?
Egal ob mit Kabel, Schleifkontakt, Leiterlinie oder Punktladung – bevor Sie sich für ein Batterieladegerät entscheiden, sollten Sie alle verfügbaren Lösungen prüfen. Jedes System hat seine Vor- und Nachteile. Auf Basis Ihrer konkreten Anforderungen bieten erfahrene Energieexperten wie Wiferion eine umfassende Beratung an.
Welches Ladegerät eignet sich für LiFePO4 und LFP Batterie (Lithium-Eisenphosphat)?
Induktive Batterieladesysteme sind generell für allen Batterietypen geeignet. Da Lithium-basierte Batterien für ein kurzfristiges Zwischenladen mit hohen Strömen ausgelegt sind, ist die kontaktlose Batterieladetechnik perfekt für die effiziente Stromübertragung geeignet.