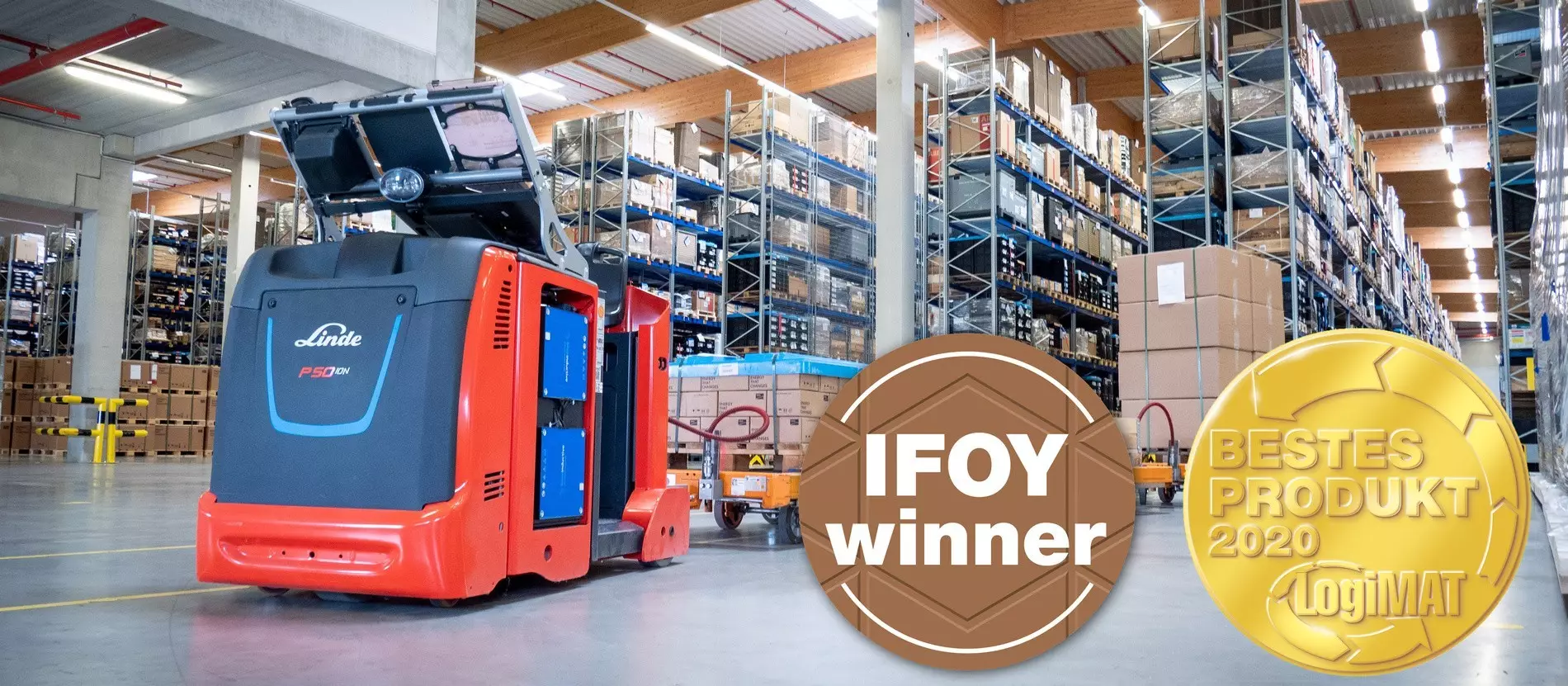
Automatisierte FTS Routenzüge:
Mehr Produktivität durch induktives Laden
Mehr Produktivität durch induktives Laden
Autonome Routenzüge gelten als die wirtschaftlichste und sicherste Lösung für die taktgesteuerte Belieferung von Produktionslinien. Im Vergleich zu anderen Flurförderfahrzeugen wie beispielsweise Gabelstapler erzielt ein automatisierter Routenzug enorme Produktivitätssteigerungen. Gleichzeitig wird durch unterschiedliche Ladungsträger das innerbetriebliche Verkehrsaufkommen minimiert. Sind die Systeme mit einer induktiven Energieversorgung ausgestattet, lässt die Produktivität der Intralogistik weiter maximieren.
Einsatzgebiete des automatisierten Routenzuges
Eine Automatisierung mit dem Routenzug lohnt sich dort, wo Material über eine längere Wegstrecke von der Quelle (Supermarkt) zur Senke befördert werden muss. Sie eignen sich für planbare, standardisierten Intralogistik-Prozesse. Beispielsweise für die just-in-time Versorgung der Produktion und Montage mit Produktionsmitteln. Je nachdem welche Prozesse und Anforderungen bei einem Unternehmen vorliegen, beispielsweise, wenn dieser eine feste Route hat, lässt sich der Routenzug teilweise oder vollständig automatisieren und somit eine höhere Produktivität erzielen.
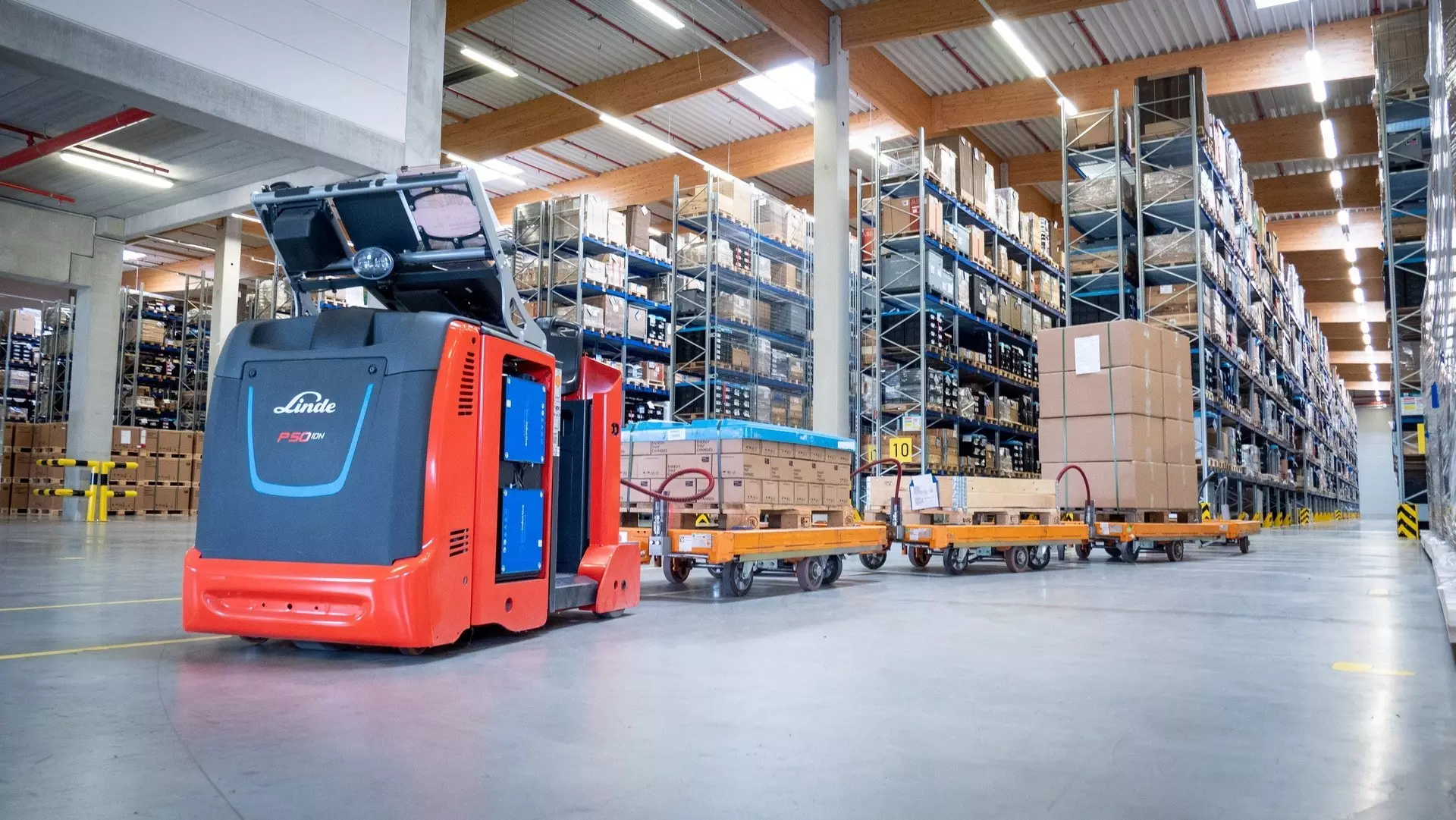
Ausgewählten Kunden und Partnern mit automatisierten Fahrzeugen
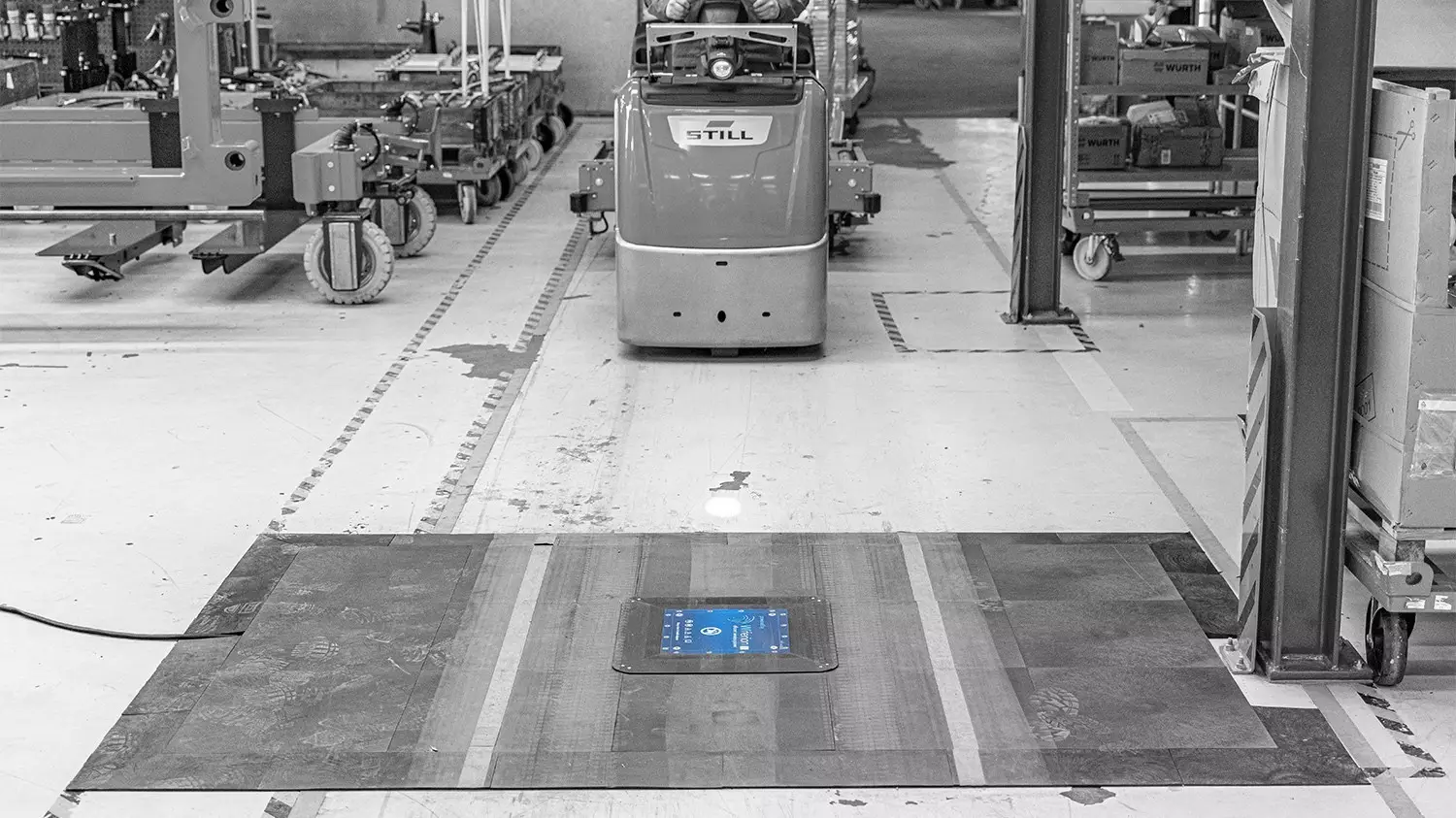
Ein vielfaches der Produktivität
Ein Routenzug besteht aus einem Zugfahrzeug (Schlepper) und mehreren Rahmen (Anhänger), für den Transport der Ladungsträger. Dabei sind die Ladungsträger sehr individuell und je nach Einsatz sehr unterschiedlich. Ist der Einsatz von Routenzügen im horizontale Materialflüsse, dann wird häufig das Transportgut auf schiebbaren Paletten oder Trolleys auf die Anhänger geladen.
Der Vorteil von einer Routenzug Lösung im Vergleich zum Gabelstapler, ist ein Vielfaches der Produktivität. Da diese automatisiert fahren, decken Sie alle Stationen des Warenflusses ab und sparen somit unnötige Wege zum Lager pro Fahrt.
Fahrerlose Transportsysteme: Wie wird ein Routenzug automatisiert?
Es gibt drei Arten, wie Unternehmen diesen automatisieren können.
- Nur der Fahrbetrieb ist automatisiert
- Nur die Be- und Entladung der Rahmen ist mit angetriebener Rollenbahnen automatisiert
- Kombination aus automatisiertem Fahrbetrieb sowie automatisierter Be- und Entladung
Die erste Variante lohnt sich besonders, wenn zwischen dem innerbetrieblichen Transport große Strecken liegen, die der Fahrer unproduktiv zurücklegt.
Die zweite Variante wird bei großen Gewichten genutzt. Dabei handelt es sich um Gewichte, die einen Fahrer über seine Leistungsgrenze hinaus belasten würden.
Die dritte Variante ist besonders interessant für Unternehmen, die den Routenzug im Drei-Schicht-Einsatz nutzen, da hier hohe Kostenreduktionen erzielt werden können.
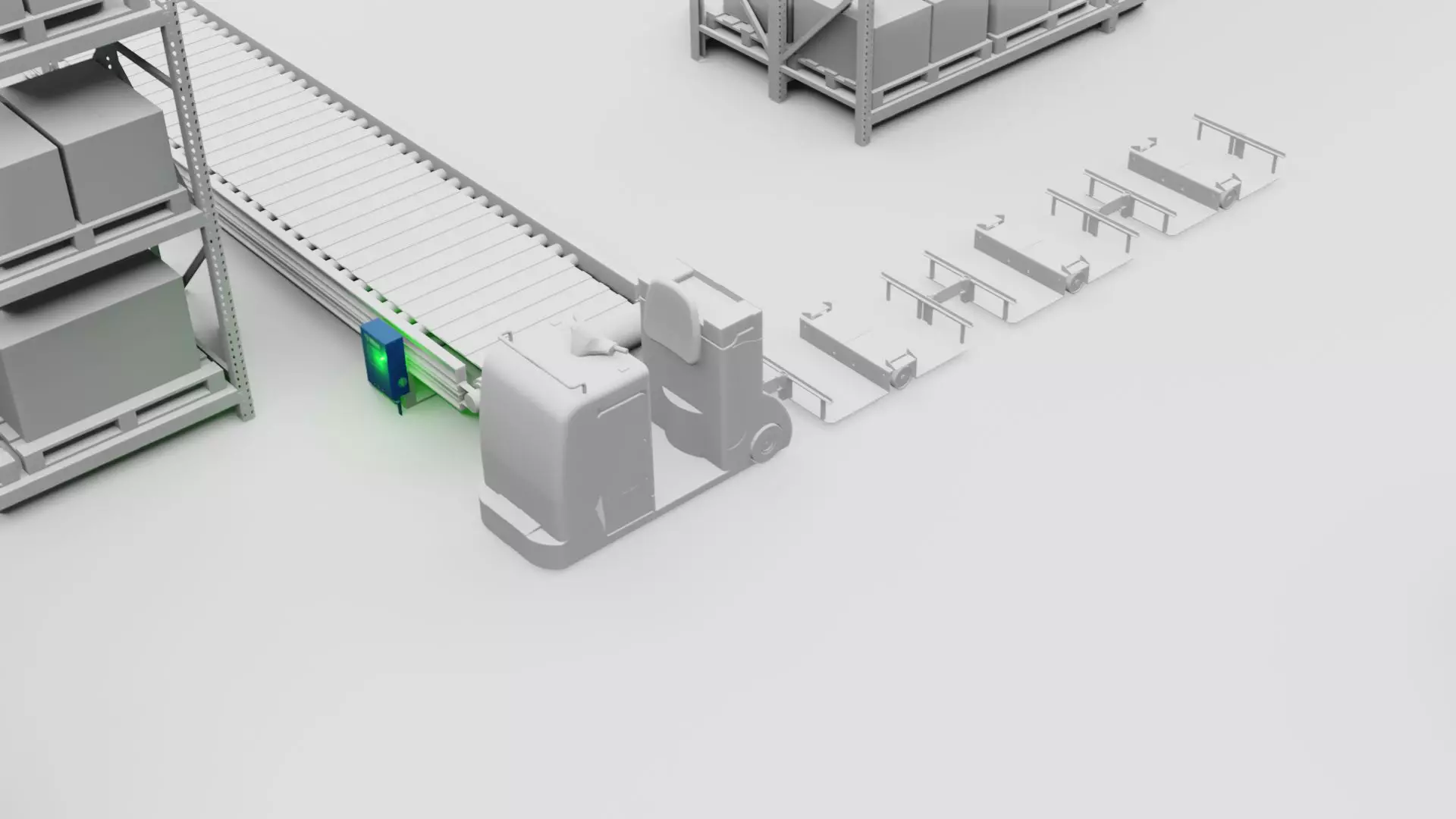
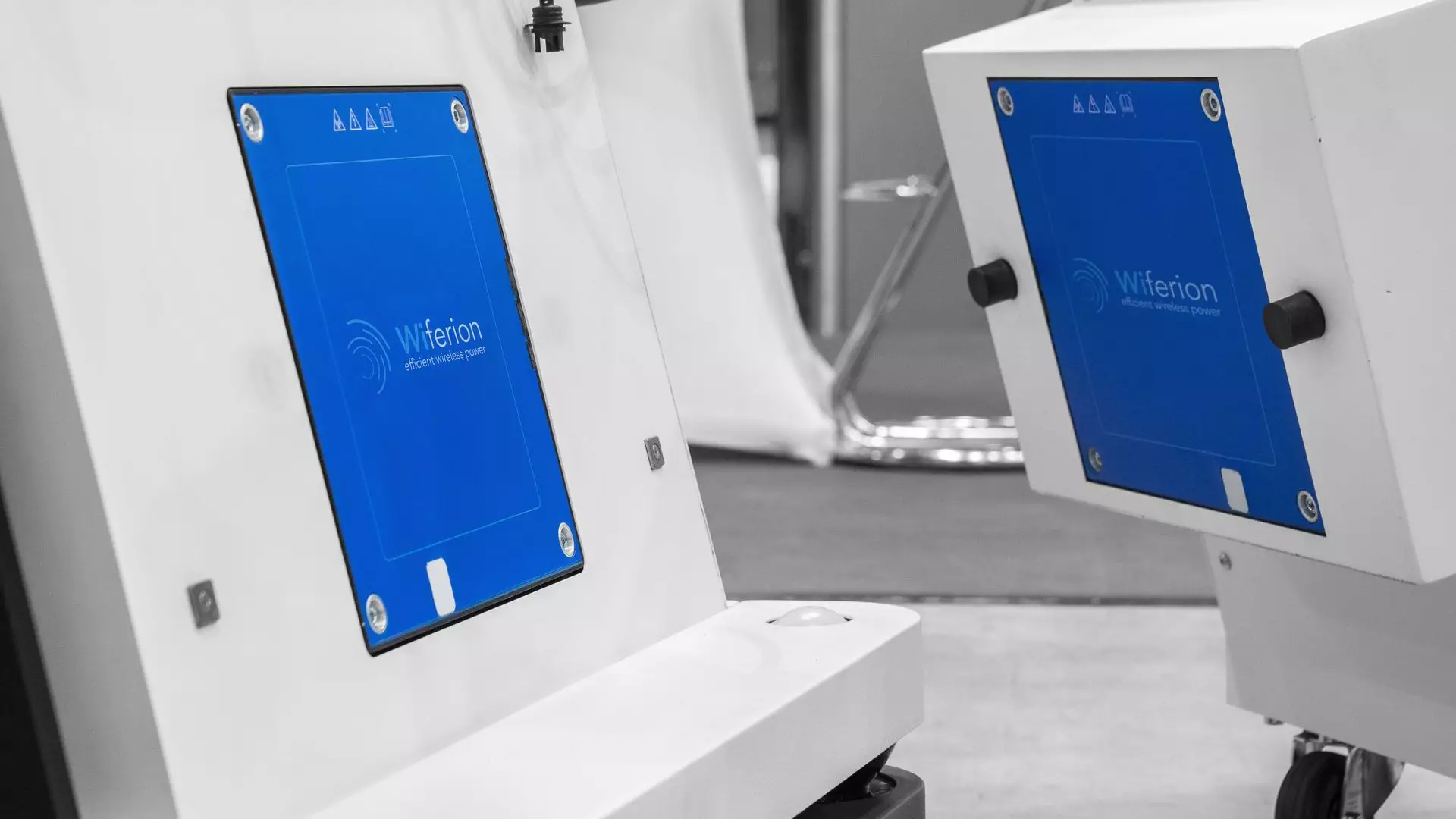
Automatisierte Energieversorgung als Schlüsseltechnologie
Für eine effiziente Logistik ist es entscheidend, dass die vorhandenen Ressourcen bestmöglich eingesetzt werden. Daher ist die induktive Energieversorgung der Routenzug Batterien essenziel. Beim sogenannten „In-Process Charging“ werden induktive Ladestationen an häufig frequentierten Stationen installiert. So lassen sich bereits kurze Stillstandszeiten nutzen, um die Zugfahrzeuge und fahrerlose Transportsysteme mit der Wireless Charging Technologie zu laden. Lange Pausen für das Aufladen der Batterien oder der aufwändige Wechsel der Batterietröge entfallen vollständig. Auch das Fahren zu den Batterieladezonen wird überflüssig.
Im Vergleich zu herkömmlichen Batterieladesystemen mit Schleif- oder Steckverbindungen erhöht das kabellose Laden der Batterien die Produktivität um 30 %.
Zudem steigt durch das Laden ohne Kontakt die Sicherheit. Die Anhänger müssen nicht mehr abgekoppelt werden, damit der Schlepper zur Batterieladestation fahren kann. Aus diesem Grund gibt es keine abgestellte Rahmenelemente im Lagerumfeld mehr, die die logistischen Prozesse und Workflows stören könnten.
Beispiel für einen Routenzug Logistik Loop
mit „In-Process Charging“
mit „In-Process Charging“
Ein klassischer Routenzug Loop mit „In-Process Charging“ beginnt, fahren in der Produktionslogistik, indem der Schlepper autonom zu den Bahnhöfen am Supermarkt fährt. Hier erfolgt die Beladung der Ladungsträger auf die Routenzug Anhänger. Während dieses Vorgangs startet die Energieversorgung der Batterie automatisch in weniger als einer Sekunde.
Erreicht der Schlepper die erste Station, wird Material entladen. Der freigewordenen Rahmen kann an der nächsten Station einen leeren Ladungsträger aufnehmen. Auch hier erhält der automatisierte Routenzug die nächste Dosis Energie.
Sobald autonome FTS Routenzüge alle Stationen der Produktionslinie abgefahren haben, transportieren Sie die leeren Ladungsträger zum Bahnhof. Dort werden diese abgeladen und nehmen neue Ladungsträger oder auch schwere Lasten für die nächste Tour auf. In wird der fahrerlosen Routenzug erneut via „In-Process Charging“ geladen.
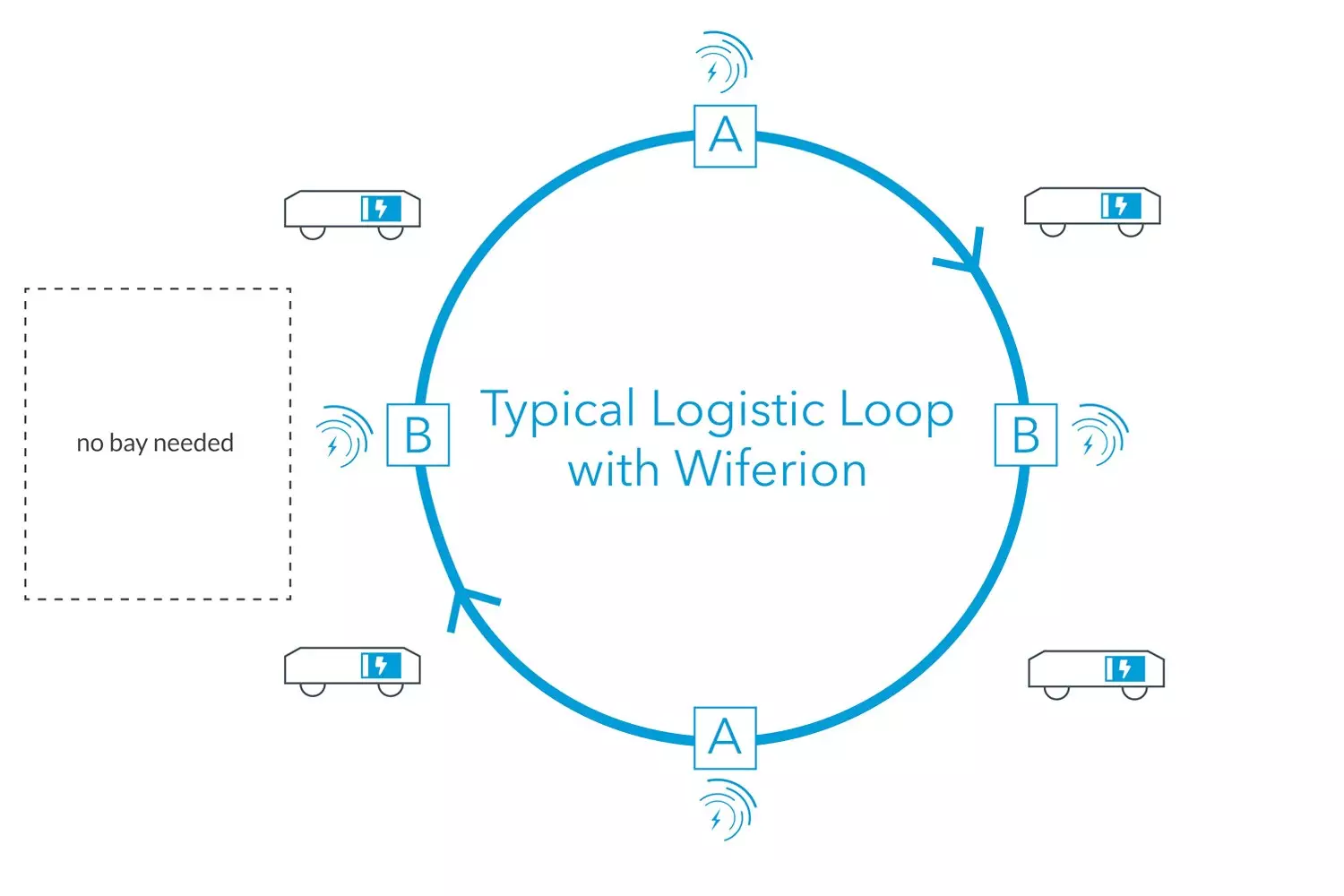