Mobile manipulators (MoMa): inductive charging enables simultaneous power supply to the robotic platform (AMR) and cobot
Mobile manipulators (MoMa) are being used increasingly in industrial applications, whether for pick-and-place applications, machine assembly or order picking. The robotics solutions consist of an autonomous mobile robot (AMR) that works as a mobile platform and a collaborative robot (cobot) mounted on it. This makes it possible to automate more complex handling tasks without having to install a stationary robot. However, the performance of the systems has so far been severely limited by non-optimally coordinated energy supplies for both systems.
Why is there not enough power for the platform and the cobot?
A mobile manipulator combines the advantages of AMR and collaborative robots into a versatile tool. It can be used to automate complex physical tasks in an industrial environment that were previously only performed by humans or intelligent assist to perform tasks in shared workspace.
Both the platforms and the arms for manipulation are established technologies that have proven themselves in use in industry. There are numerous suppliers of both mobile robots and robotic arms for numerous applications of cobots to rise the production quality.
A mobile manipulator therefore combines two systems that were originally developed separately. The problem: during the design process, the two technologies are often not considered as a single product and are dimensioned accordingly.
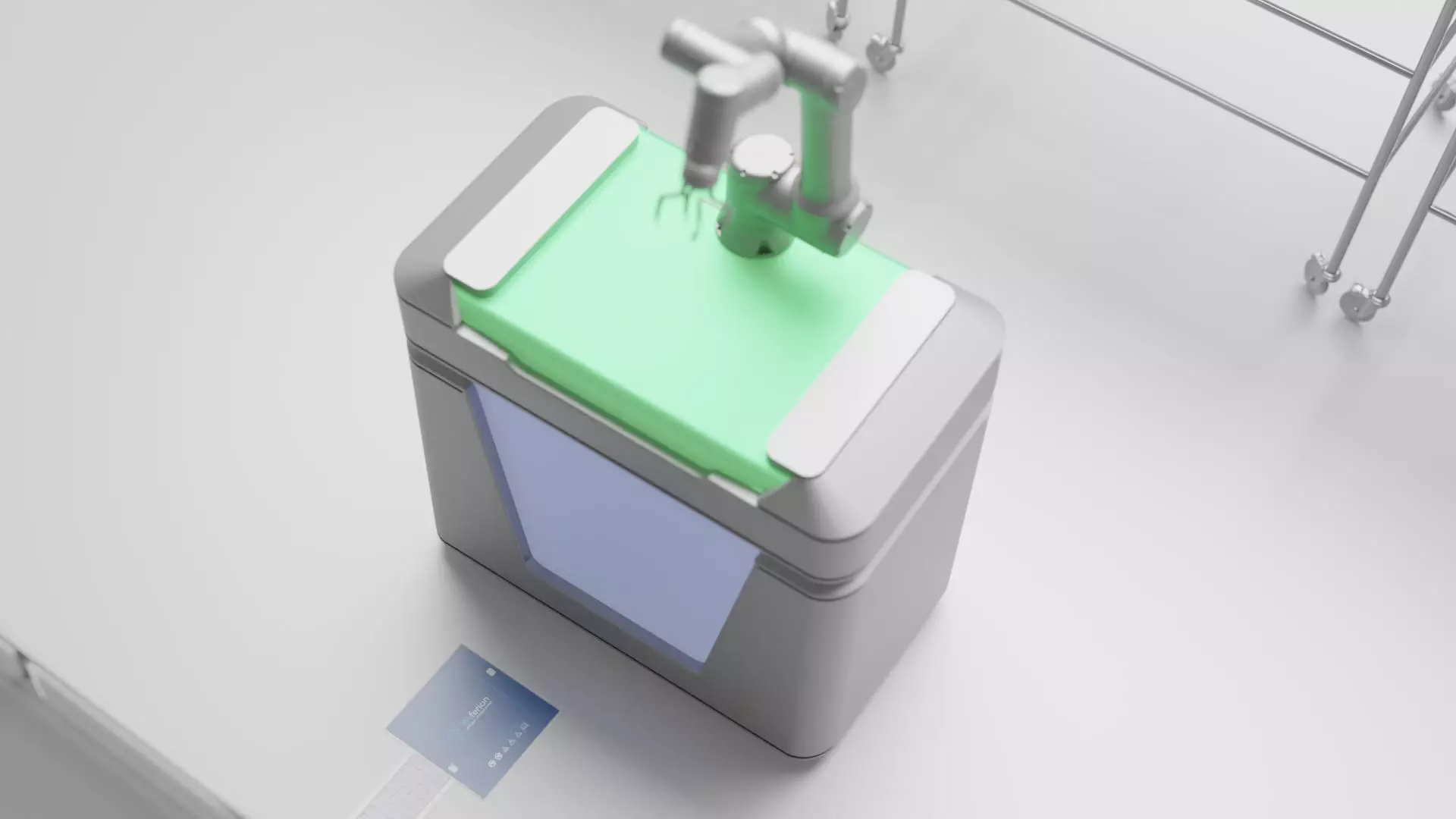
Selected customers and partners with integrated wireless charging at AMR
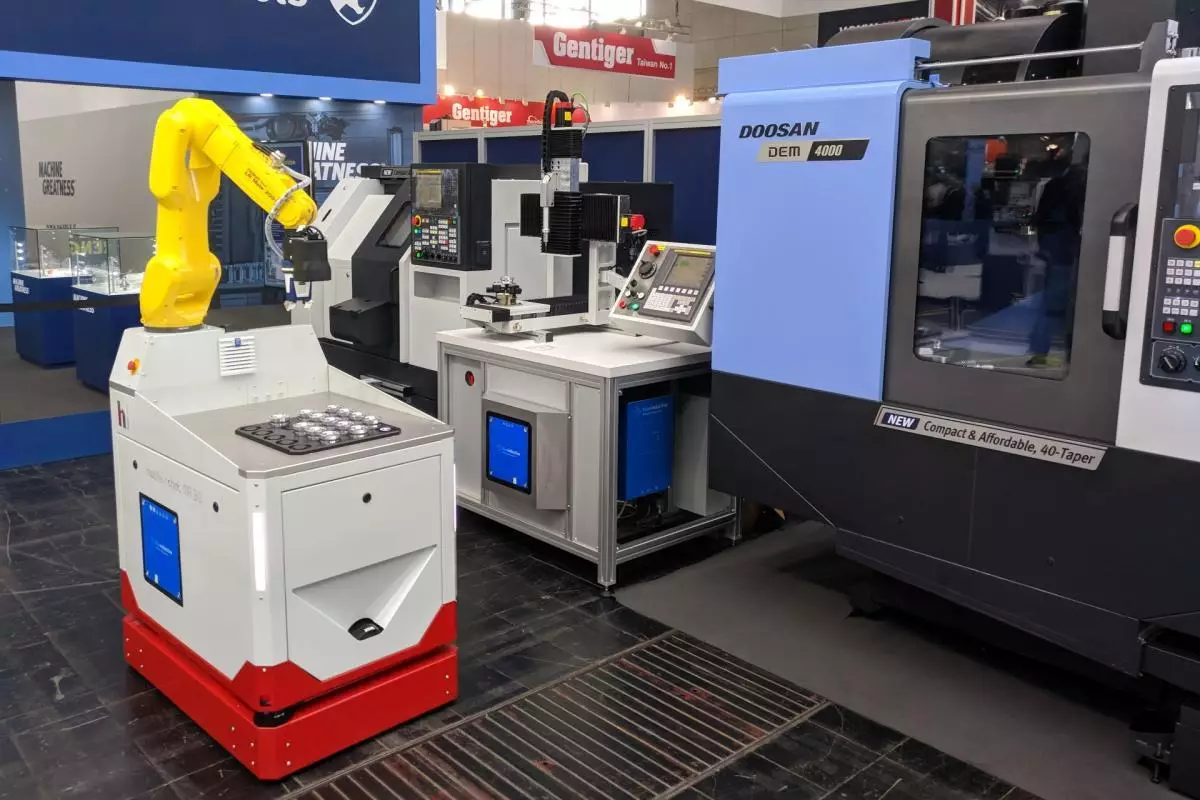
Both the mobile robot and the cobot have their own power system
Both the mobile robot and the cobot have their own energy system. When the arm is mounted on the platform, the energy available in the AMR batteries is limited for longer tasks as the batteries installed in the mobile platform are not designed to supply the cobot. Due to the additional energy demand, the autonomy of the system is severely limited because the charging power is not sufficient for such an energy demand. It even happens that autonomous mobile robots and robotic arms have to be charged separately of each other.
This means 24/7 operation of AMR and cobot is not possible with the AMR available on the market to date and their battery capacity. Considering the high costs of MoMa systems, widespread deployment of mobile manipulators instead of traditional industrial robot is unlikely.
Our inductive charging technology solves this problem. In the Wiferion Power Box, we have developed an power module that enables simultaneous and efficient energy supply to the robotic arm and platform.
The central energy unit for mobile manipulators
The Wiferion Power Box consists of our etaLINK wireless charging system and etaStORE high-performance batteries. With it, we transmit electrical energy without any contact – quickly, safely and efficiently.
The highlight: the Power Box not only supplies the mounted cobot with energy, but also the mobile platform. The Power Box therefore constitutes the central energy unit for both robot systems.
The battery system can be dimensioned flexibly depending on the energy requirements. The PowerBox can supply a robotic arm reliably with both 24V and 48V. On top of this, the box can be equipped with industry-standard DC/AC converters and can be operated with any type of industrial current with 230V AC or 400AC. This expands the possibilities of manipulation solutions that can be operated on the AMR.
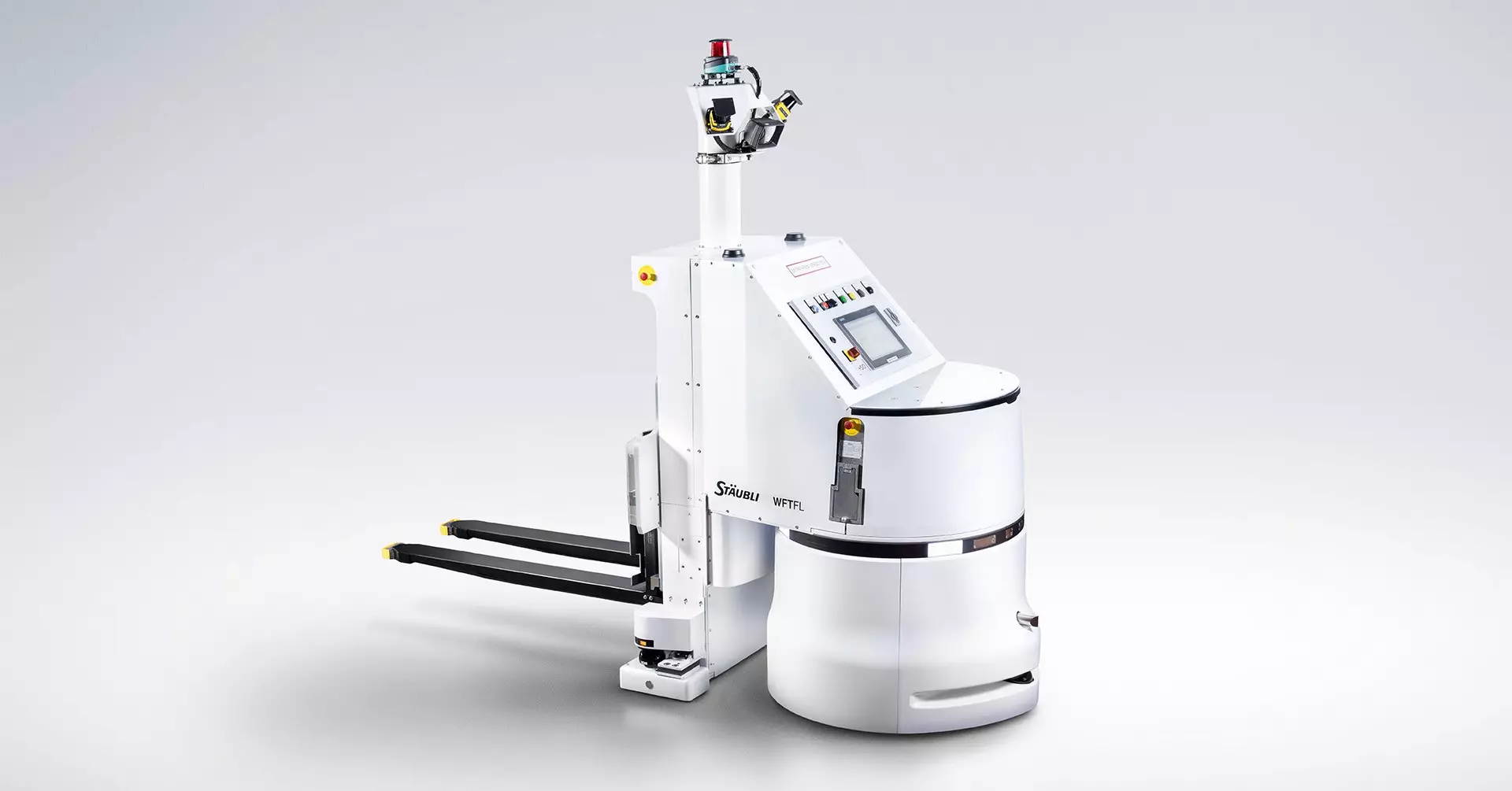
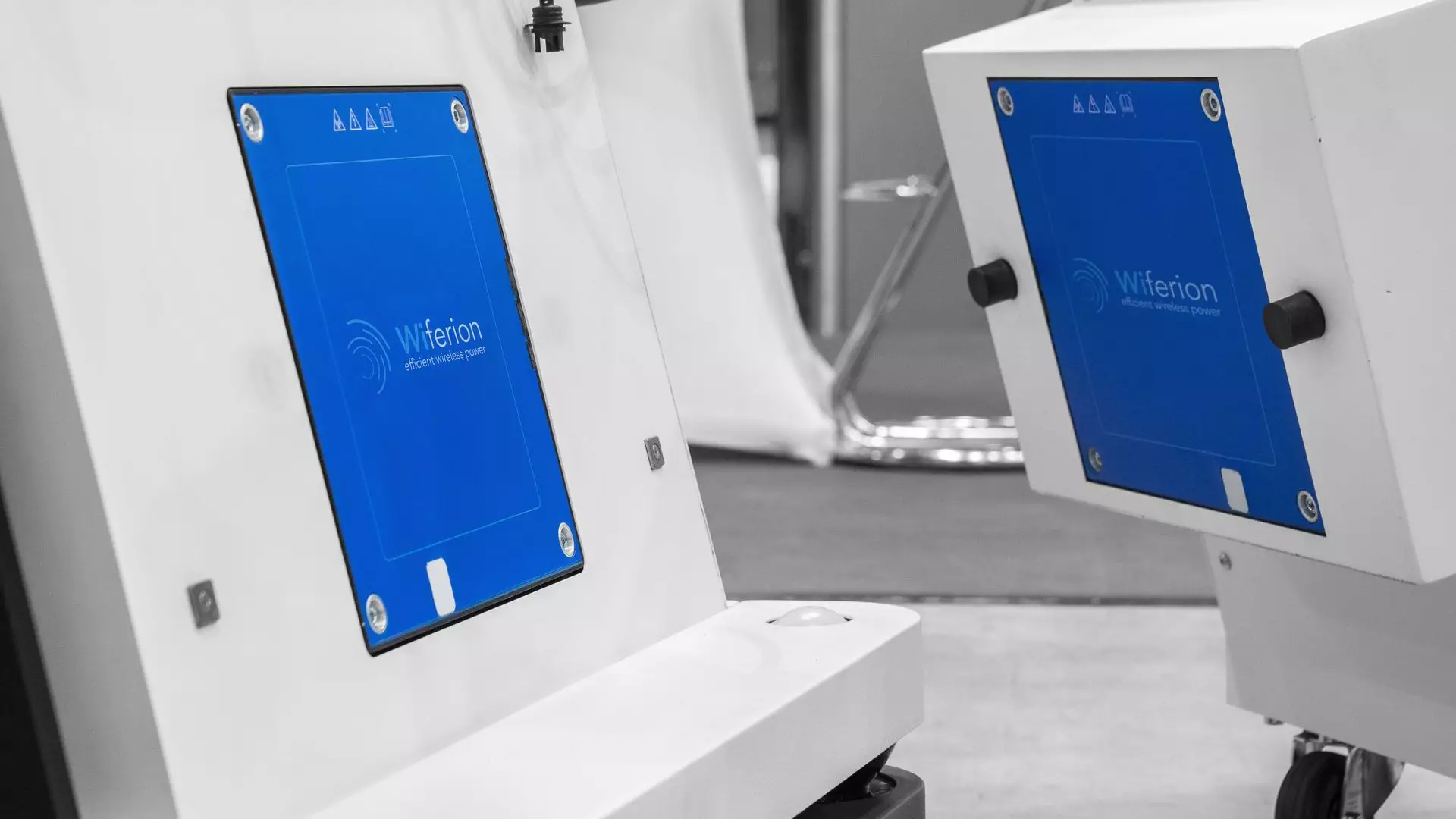
24/7 availability for mobile manipulators
Wireless charging enables automated intermediate charging of the manipulator at pick or work stations and thus 24/7 operation of the system. Our built-in inductive battery charging system does not wear out the components and thus ensures maintenance-free continuous operation. Due to the high positioning tolerance, the factory navigation precision of all common AMR is sufficient to ensure positioning of the autonomous mobile robot at the charging point.
Only a few seconds can be used for energy supply
Thanks to the contactless design and flexibility, the manipulators are charged while doing their work. With in-process charging, the robot repeatedly receives intermediate charges at frequently visited stations, ensuring that sustainable 24/7 operation is possible. Even the shortest stops of a few seconds can be used for recharging. A stationary charging station is therefore superfluous. The charging points for mobile manipulator systems can be installed quickly and easily and can be repositioned at any time.
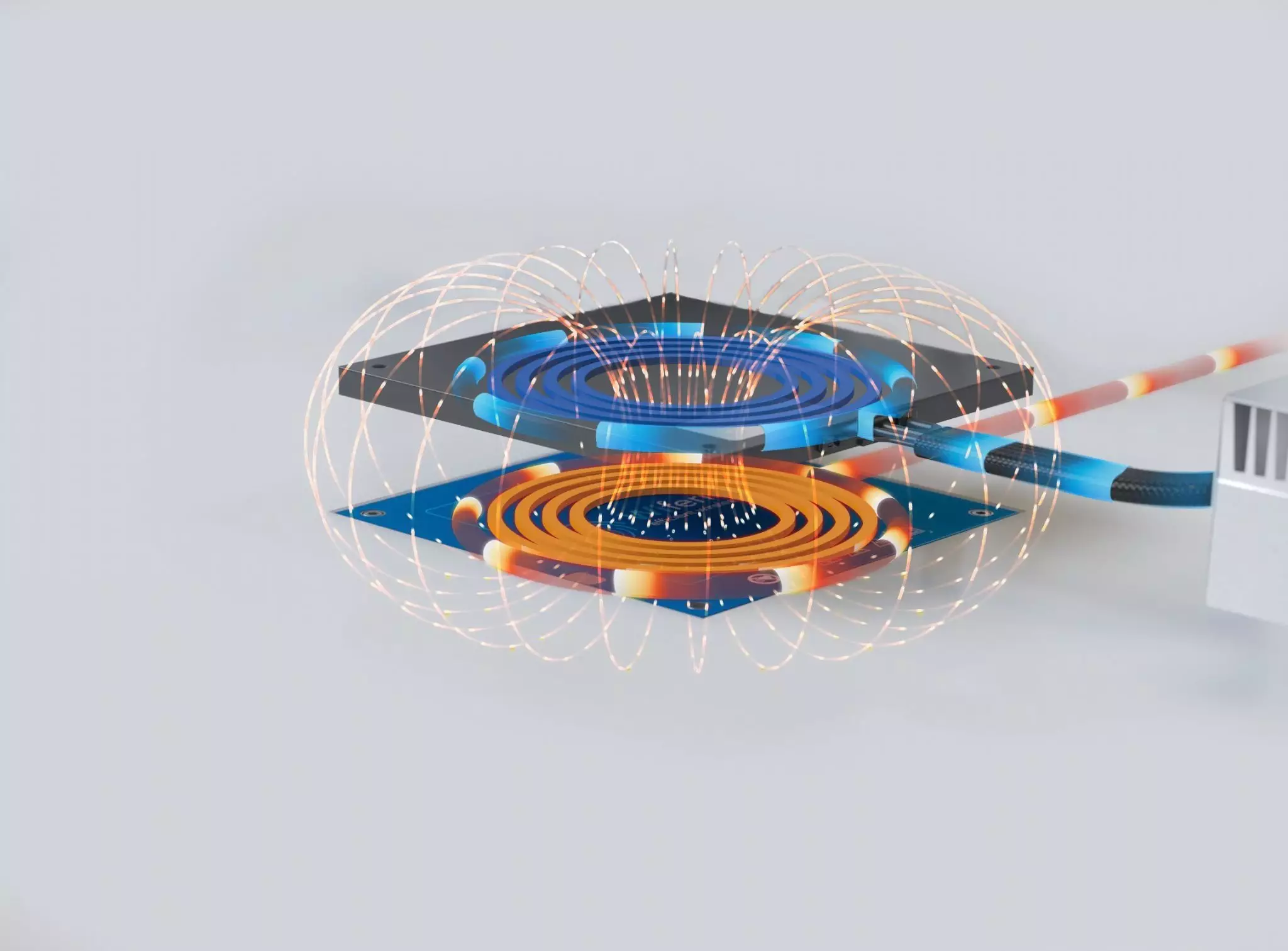