Der weltweite Hunger nach Mikrochips steigt rasant an. Um der hohen Nachfrage gerecht zu werden, müssen die Produzenten ihre Fabriken weiter automatisieren. Mit dem aus einem kollaborativen Roboter und einer mobilen Plattform bestehenden KMR iiwa CR bietet KUKA eine sichere und produktivitätssteigernde Automatisierungslösung für den Transport hochempfindlicher Halbleitersubstrate (Wafer). Dank der integrierten, induktiven Ladetechnologie von Wiferion erfüllt das System höchste Anforderungen in puncto Reinheit, Produktivität und Sicherheit.
Automatisierung in der Halbleiterfertigung
Die Halbleiterindustrie boomt. Megatrends wie das Arbeiten von zu Hause, das Wachstum künstlicher Intelligenz und die steigende Nachfrage nach Elektroautos führen dazu, dass die Nachfrage nach Halbleitern weiter stark anzieht. Laut der Unternehmensberatung McKinsey & Company wuchs die Branche allein im Jahr 2021 um 20 %. Die Berater prognostizieren, dass die weltweite Halbleiterindustrie jährlich um 6–8 % wachsen und bis 2030 zu einer Billionen-Dollar-Branche werden wird. Um den riesigen Bedarf an leistungsfähigen Prozessoren zu decken, investieren die Chiphersteller in neue Produktionsstandorte.
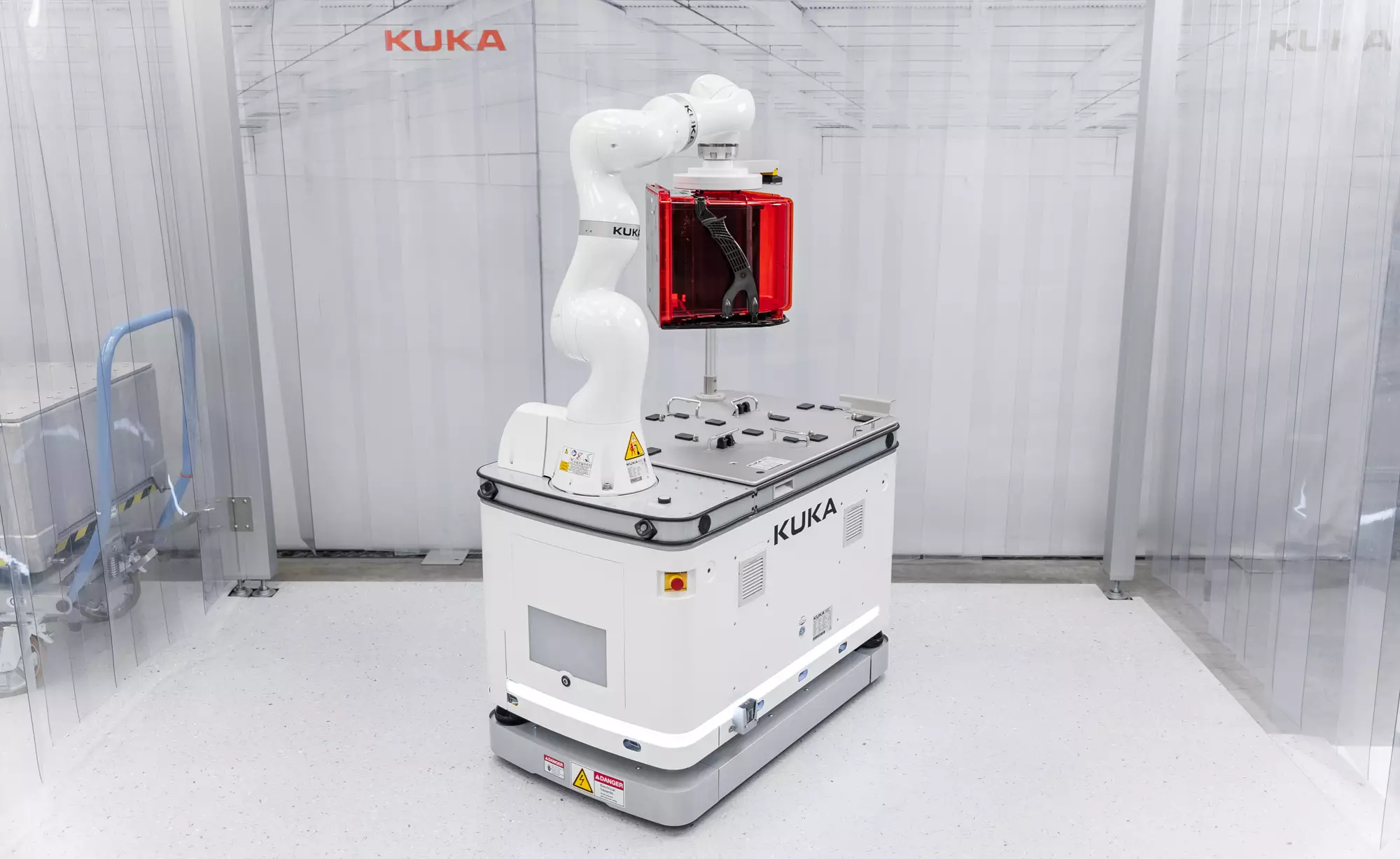
Wafer-Transport ist fehleranfällig
Für eine moderne Chipfabrik sind Investitionskosten von mehreren Milliarden Dollar keine Seltenheit. Entsprechend hoch sind die Erwartungen an die Zuverlässigkeit und Effizienz der Smart Factories.
Bis aus einem Roh-Wafer ein Mikrochip wird, sind oft mehrere 1.000 Arbeitsschritte in einer aufwendig gesicherten Reinraumumgebung erforderlich. Je nach Bauteil vergehen so rund drei Monate, bis der Wafer die 24/7-getaktete Produktion verlässt. Daher spielen die Transportsysteme und die Steuerung der Anlage und der Prozesse eine entscheidende Rolle für den Erfolg von solchen Megafabriken. Einzelne Schritte der Produktion sind bereits sehr gut und auf hohem Qualitätsniveau automatisiert.
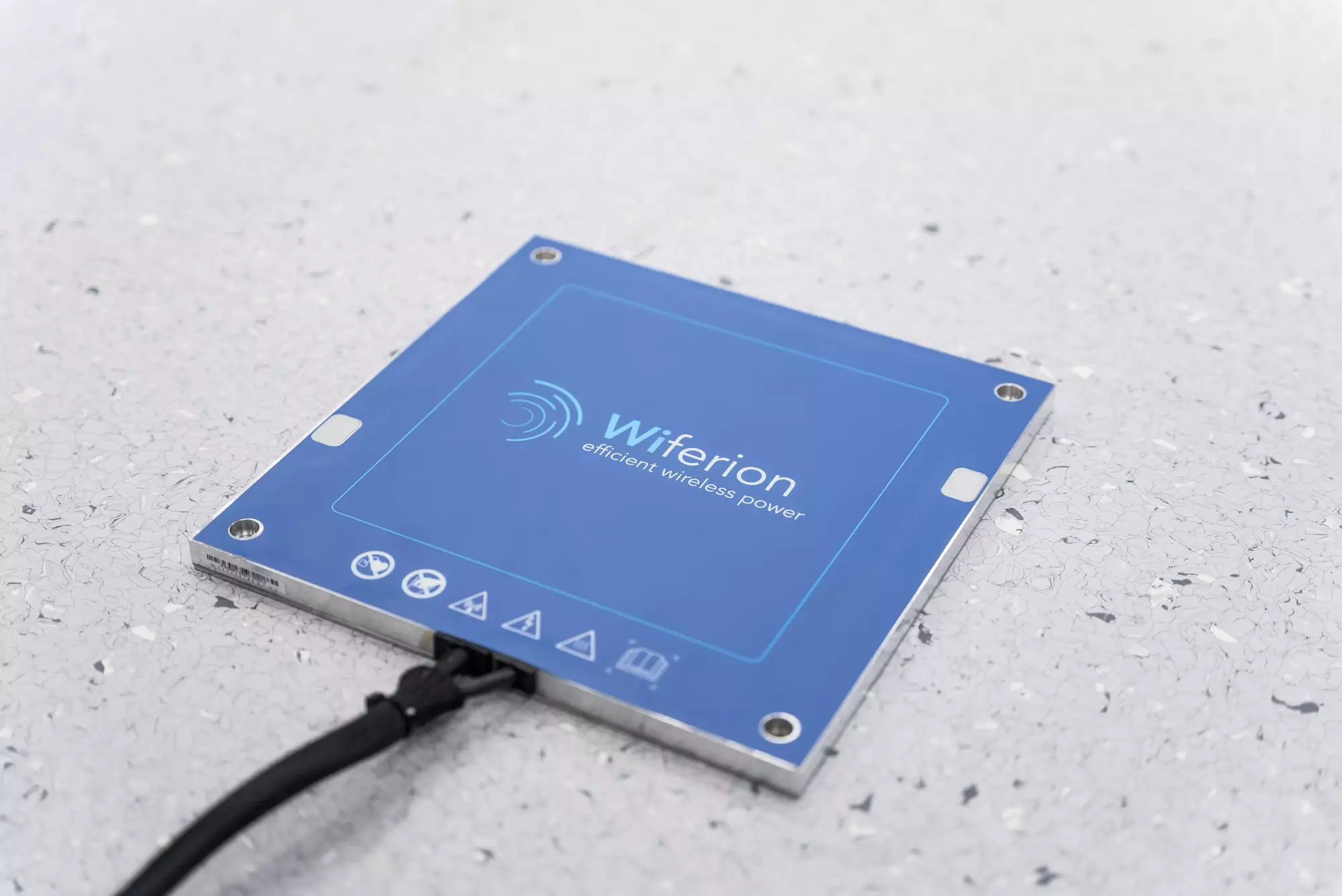
Wireless Charging für höchste Reinheitsanforderung
Eine Ausnahme bildete bislang der Transport der Halbleitersubstrate von einer Arbeitsstation zur nächsten. Besonders in älteren Produktionsstätten werden die Wafer überwiegend manuell von einem Mitarbeiter in sogenannten Wafer-Kassetten aus einer Bearbeitungsmaschine entnommen und mit einem Wagen zum nächsten Prozessschritt gebracht. Dabei ist der Prozess fehleranfällig. Fällt einem Mitarbeiter ein bruchempfindlicher Wafer herunter oder legt er aus Versehen die falsche Kassette in eine Bearbeitungsmaschine, sind schnell fünfstellige Beträge verloren. Eine Automatisierung der Handling- und Transportprozesse mit mobilen Manipulatorrobotern verringert das Schadensrisiko auf ein Minimum. Mit dem KMR iiwa CR hat KUKA einen mobilen Cobot für die sichere Handhabung von empfindlichen Bauteilen wie Wafern im Portfolio, der aufgrund seiner induktiven Ladetechnologie auch höchste Reinheitsanforderungen erfüllt.
Mobiler Cobot von KUKA für den Reinraum mit induktivem Laden
Der KMR iiwa CR ist eine Kombination aus einem Reinraum-Cobot und einer mobilen Roboter Plattform. Der patentierte Greifer des Roboters ist speziell für Handlingapplikationen in Reinraumumgebungen konzipiert. Dank innovativer Navigationssoftware operiert der KMR iiwa CR autonom im Raum, be- und entlädt die Wafer-Kassetten selbstständig und bringt sie zur nächsten Arbeitsstation. Und das unter Einhaltung strenger Klasse ISO 3-Reinraumbedingungen. Die mobilen Industrie KUKA Roboter sind dafür ausgelegt, in Umgebungen, die sauberer als ein OP-Saal sein müssen, ihre Arbeit und ihre mechanischen Bewegungen zuverlässig zu verrichten.
Minimale Partikelgenerierung bei höchster Produktivität
Für die Einhaltung der ISO-Klasse 3 ist unter anderem die Energieversorgung des KMR iiwa CR ein zentrales Feature. „Für eine anspruchsvolle Reinraumumgebung sind herkömmliche Batterieladesysteme mit Schleifkontakten nicht geeignet“, erklärt Jakob Brandl, Portfolio Manager Mobility bei KUKA. „Bei jedem Ladevorgang entsteht Kupferabrieb. Die Partikel verteilen sich in der Produktionsumgebung und können im Extremfall die wertvollen Wafer beschädigen.“ KUKA verwendet daher das induktive Batterieladesystem etaLINK 3000 von Wiferion. Die Energieübertragung im Reinraum erfolgt dabei berührungslos und kabellos. Damit gewährleistet KUKA einen Ladeprozess mit minimalster Partikelgenerierung.
Alter Prozess sehr fehleranfällig
Darüber hinaus ermöglicht die Ladetechnologie, die Produktion ohne Unterbrechungen für das Laden der Batterie aufrechtzuerhalten. „Wir laden unseren Cobot via „In-Process-Charging“. Dabei fährt der Roboter während des Pick-and-Place-Prozesses über eine Ladestation und wird im Prozess geladen – ohne jeglichen Zeitverlust“, erklärt Pascal Caprano, Head of Industry Management Concept Engineering bei KUKA. Die Ladepunkte lassen sich beispielsweise vor den Bearbeitungsmaschinen anbringen. Die Energieversorgung startet dann automatisch, wenn der KMR iiwa CR die Wafer-Kassetten einlegt und entnimmt.
KUKA steigert Prozesssicherheit
Auch in puncto Sicherheit setzt der Cobot dank der induktiven Stromübertragung neue Maßstäbe. Während herkömmliche Kontaktladeplatten mehrere Zentimeter auf dem Boden aufbauen, damit die Energieversorgung trotz Bodenfreiheit eines Roboters funktioniert, sind die Ladeplatten von Wiferion sehr flach und lassen sich ebenerdig im Boden versenken. „Wir eliminieren damit Stolperfallen für die Mitarbeiter im Reinraum“, zeigt Jakob Brandl die Vorteile des Systems auf. Zudem entfällt die Wartung aufgrund von abgebrochenen oder verunreinigten Kontakten. „Im Ergebnis steigern wir damit die Prozesssicherheit der gesamten Produktion.“
„Unser Roboter steht nur wenige Minuten, um eine Handlingaufgabe durchzuführen. Für uns ist es immens wichtig, dass wir in dieser kurzen Zeit hohe Ladeströme abrufen können“, sagt Pascal Caprano. Das etaLINK-System überträgt den Strom mit 3 kW und bis zu 60 V Ladespannung. „Damit bietet uns Wiferion die ideale Lösung für einen effizienten 24/7-Betrieb des Systems.“
Fazit
Die Anforderungen an eine intelligente Automatisierung im Reinraum sind hoch. Mit dem KMR iiwa CR bietet KUKA eine sichere und produktivitätssteigernde Automatisierungslösung für Handling- und Transportprozesse in der Halbleiterproduktion. Die integrierte induktive Ladetechnologie von Wiferion erhöht die Prozesssicherheit und ermöglicht einen 24/7-Betrieb des Systems. Aus diesem Grund wird KUKA die Ladetechnologie auch bei Nachfolgemodellen serienmäßig integrieren.