Von der Insolvenz zum Technologieführer: In Zeiten wirtschaftlicher Unsicherheit sind Innovation, Know-how und eine klare Vision entscheidend. Eisenmann hat diese Herausforderungen nicht nur gemeistert, sondern sich als Vorreiter in der Lackiertechnologie etabliert. Mit der revolutionären Zusammenarbeit mit Wiferion setzt das Unternehmen im Lackierprozess neue Maßstäbe.
Good Lack: Autonome FTS sorgen für Energieeinsparungen in der Automobilindustrie
Rohbaureinigung, Nahtabdichtung, Tauch- und Decklackierung – damit der Lack nicht abblättert, muss eine Karosserie im Lackierprozess eine Vielzahl von Arbeitsschritten durchlaufen. Da sie erst zum Schluss ihre Reifen erhalten, werden die Metallkarossen in der Regel auf Schlitten gesetzt, die mittels Skid-Fördertechnik von Station zu Station transportiert werden. Ein bekanntes Problem in der Lackierbranche ist die extreme Aufheizung und Abkühlung der Karosserie sowie des Schlittens während des Prozesses, was zu erheblichem Energieverbrauch führt. Dank der innovativen FTS von Eisenmann, die durch die robusten und effizienten etaLINK-Systeme von Wiferion unterstützt werden, gehören diese Herausforderungen der Vergangenheit an.
Vom Schlitten zum autonomen Fahrzeug: Effizienzsteigerung in der Lackiererei
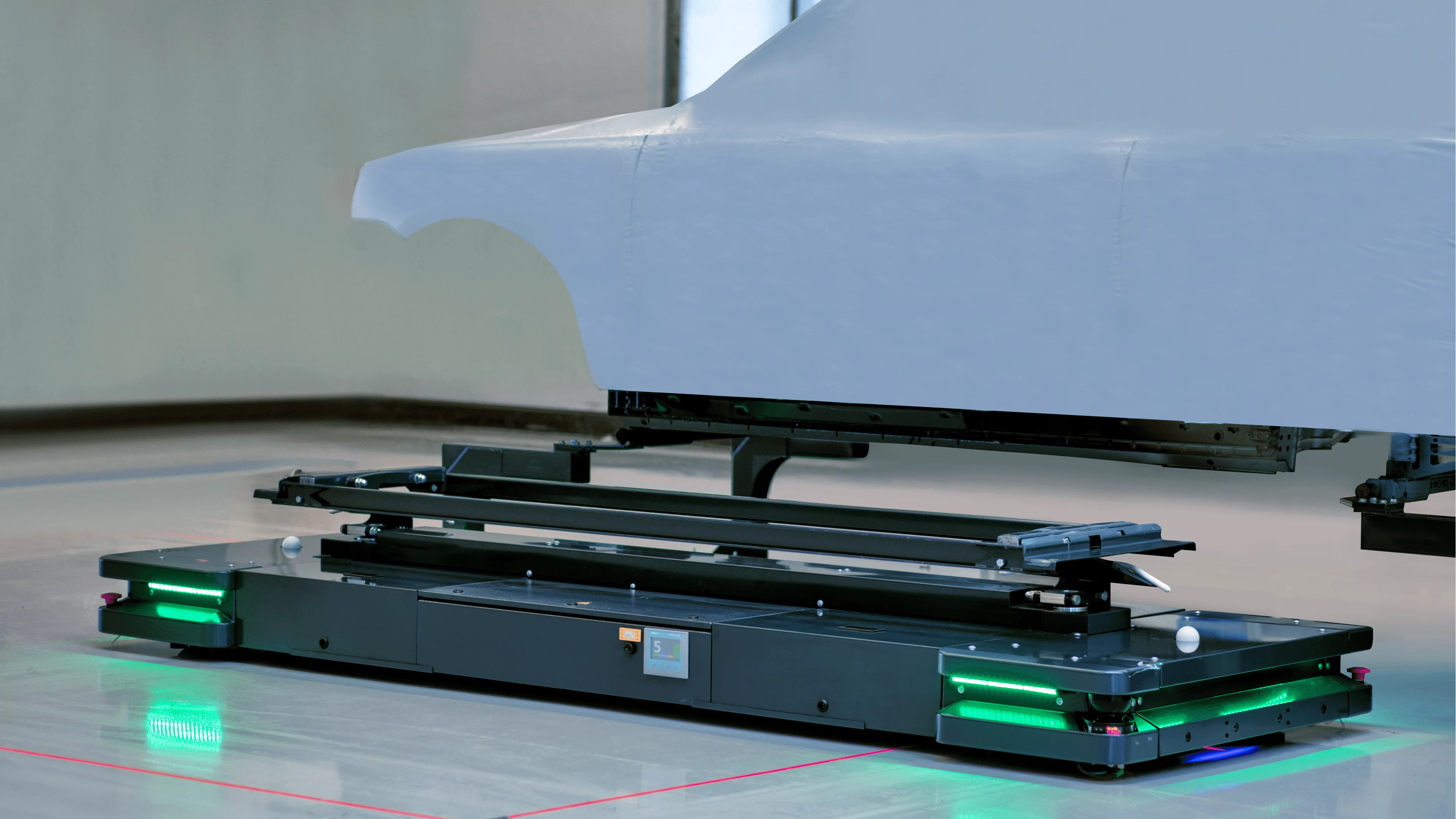
Neben Fördertechnik für die Vorbehandlung (VBH) und für die kathodische Tauchlackierung (KTL) gehören vielseitige Systeme zur Lacktrocknung und -abscheidung sowie Applikationstechnik für das automatisierte Handling zum Portfolio von Eisenmann. Der Spezialist für Lackiererei, der bereits in den 90er Jahren zu den Technologieführern seiner Branche zählte und vor allem die Automobilindustrie beliefert, blickt auf eine langjährige Tradition mit Fahrerlosen Transportsystemen zurück. Im Jahr 2020 begann Eisenmann mit der Planung und Konstruktion eines neuen FTS speziell für den Lackierprozess.
Bis zu 200 Grad herrschen an den verschiedenen Stationen des Lackierprozesses. Hinzu kommt der Sprühnebel, der die Karosserie in neuem Glanz erstrahlen lässt. Beides ist eine Herausforderung für die Fördertechnik. Die Lösung: ein ausgeklügeltes Kühlsystem, eine gute Isolierung für das FTS und geschützte Fahrräume.
Mit dem VarioMover bringt Eisenmann das Rad zur Karosse
Neben den speziellen Anforderungen der Lackiererei sollte das FTS weitere Eigenschaften erfüllen. „Wir wollten ein möglichst kompaktes System entwickeln, das auch auf kleinstem und engstem Raum manövrieren kann“, sagt Axel Eipper, Product Management bei Eisenmann. Der VarioMover verfügt über acht angetriebene Räder, die omnidirektional sind, sich also auf der Stelle drehen können. Dadurch ist er in der Lage, auch kompakte Fahrwege zu realisieren. Die Räder können sowohl zum Antreiben als auch zum Lenken verwendet werden. So können auch hohe Lasten bis zu 3,5 Tonnen mit maximaler Beschleunigung und höchster Präzision bewegt werden. Gleichzeitig schützt das Rädersystem den Boden vor hohen Belastungen und dem damit verbundenen Verschleiß.
Großen Wert legte Eisenmann bei der Planung auch auf eine Steuerungstechnik nach Industriestandard. Denn eine Technik, mit der die Instandhaltung des Kunden vertraut ist, erleichtert es ihr, den reibungslosen Betrieb des FTS zu gewährleisten. Da die Steuerung des Fahrzeugs komplett von Siemens stammt, profitiert der Kunde zudem von einer guten und langfristigen Verfügbarkeit von Ersatzteilen. Mit einer Grundbauhöhe von 250 mm, die je nach Funktionalität des FTS mit zusätzlichen Komponenten erweitert werden kann, ist der VarioMover optimal auf die in der Automobilindustrie übliche Transporthöhe von 500 mm ausgelegt.
Maßgeschneiderte Technologie für höchste Skalierbarkeit im Lackierprozess
Der VarioMover verfügt über eine patentierte Technologie für die Anwendung in der Automobillackierung. Diese ist mit verschiedenen Schnittstellen ausgestattet und kann nach dem Baukastenprinzip an den kundenspezifischen Anwendungsfall angepasst werden. Mögliche Anwendungen sind der maximal skalierbare Flächenspeicher StoreMover, das prozessintegrierte FTS PaintMover, das speziell im Lackierbereich eingesetzt wird, oder der AssemblyMover für die Endmontage. Insbesondere der StoreMover verfolgt dabei einen innovativen Ansatz. Üblicherweise befinden sich zwischen den einzelnen Fertigungsschritten in der Automobilproduktion Sortier- und Pufferspeicher in Form von Hochregallagern. Diese benötigen jedoch viel Platz und sind teuer im Unterhalt. Mit dem StoreMover wird das Hochregallager durch ein Flächenlager ersetzt. Das FTS ist nur darauf ausgelegt, die Karosserien in diesem passiven Speicher zu verteilen und zum richtigen Zeitpunkt wieder abzuholen, um sie erneut der Produktion zuzuführen.
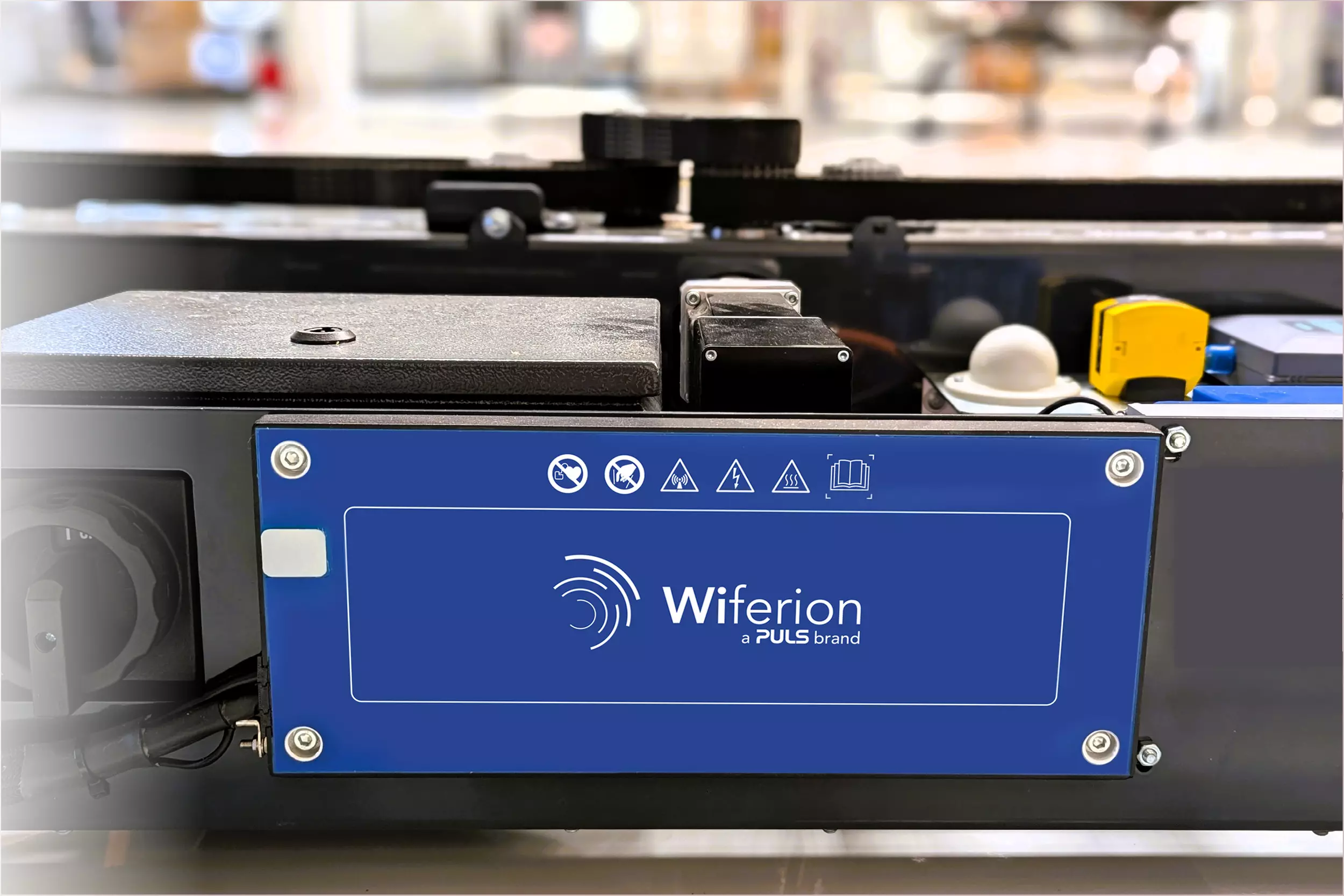
Gezielte Ladung ohne Funkenflug
Eine der gebräuchlichsten Energieübertragungen, die Kontaktaufladung, kam für den Einsatz in der Lackiererei nicht in Frage. Neben dem hohen Aufwand, die Ladekontakte an gut zugänglichen Stellen anzubringen und den erforderlichen Anpressdruck zu gewährleisten, ist vor allem die Gefahr des Funkenflugs in einem so sensiblen Bereich nicht akzeptabel. „Deshalb war von Anfang an klar, dass das System, das wir einsetzen wollten, induktiv arbeiten musste“, sagt Axel Eipper. „Da wir auch die bestehenden Anlagen ohne großen Aufwand nachrüsten wollten, suchten wir nach einer minimalinvasiven Lösung. Aufwendige Eingriffe in die Bodenstruktur, wie zum Beispiel das Einfräsen von Nuten oder Rillen, wollten wir vermeiden. Darum haben wir uns für die Lösung von Wiferion entschieden.“
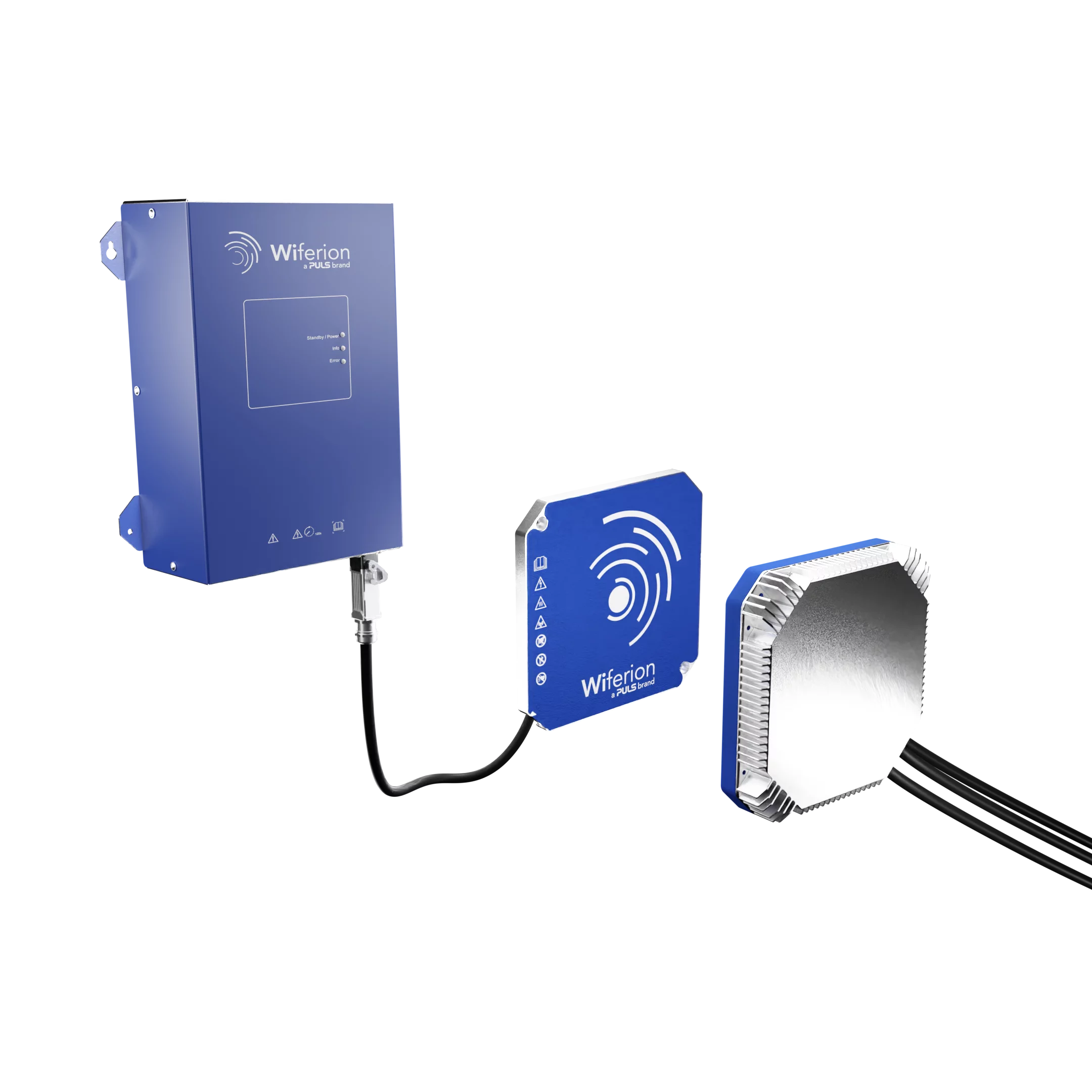
Neben der einfachen Integration in bestehende Infrastrukturen zeichnet sich das etaLink-System von „Wiferion – a PULS brand“ durch seinen hohen Wirkungsgrad aus. „Eine große Sorge unserer Kunden ist, dass die starken elektromagnetischen Felder einen negativen Einfluss auf die Gesundheit ihrer Mitarbeitenden oder auf die Stahlkonstruktion ihrer Produktionsstätten haben könnten“, berichtet Axel Eipper. „Beim Ladesystem von Wiferion wird die Energie jedoch besonders gezielt übertragen, da an der Schnittstelle zwischen aktiver und passiver Antenne eine stark gerichtete Ladekeule entsteht. Dadurch wird deutlich weniger Energie an die Umgebung abgegeben als bei anderen Ladesystemen.“
Auch die hohe Flexibilität der Wiferion-Lösung spricht für sich. etaLINK ist für unterschiedliche Batterieformate und -technologien ausgelegt. Ob LiFePo, Lithium oder Titanat – das induktive Ladesystem ist hochkompatibel. Für Eisenmann spielte auch dieser klare Vorteil eine wichtige Rolle bei der Entscheidung für Wiferion.
Perfekte Ergänzung: Eisenmanns FTS und Wiferions etaLINK
Inzwischen ist das etaLINK-System fester Bestandteil des FTS-Baukastensystems von Eisenmann. In der Regel werden die Ladeplatten in externen Bereichen außerhalb der Lackierstationen eingesetzt. Da es in der Automobilindustrie darauf ankommt, Spitzen abzufangen, sind meistens nicht alle Fahrzeuge gleichzeitig im Einsatz. „Wenn drei Karosserien gleichzeitig fertiggestellt werden, müssen drei FTS für den Weitertransport zur
Verfügung stehen, auch wenn uns von der Kapazität her eines reichen würde“, sagt Axel Eipper. „Das führt dazu, dass wir meistens zu viele FTS haben, die wir in der Wartezeit problemlos beladen können.“ Auf Kundenwunsch integriert Eisenmann die Ladestationen von Wiferion aber auch an strategisch sinnvollen Knotenpunkten entlang der Prozessstationen, um das Laden während des Betriebs zu ermöglichen. Hierfür bieten sich Stellen an, an denen die FTS für einen Ladungswechsel anhalten.
„Wir konnten unsere Kunden bereits von dieser innovativen Technologie überzeugen“, sagt Axel Eipper. „Erste Projekte befinden sich daher derzeit in der Realisierungsphase. Weitere vielversprechende Projekte sind bereits in Planung. All das zeigt, dass etaLINK die perfekte Ergänzung für unser FTS-Angebot ist. Gemeinsam mit Wiferion bieten wir der Automobilindustrie nicht nur einen aktuellen Mehrwert, sondern ebnen auch den Weg für zukünftige Innovationen im Lackierprozess. Die Weiterentwicklung unserer Technologien wird die Produktionsprozesse kontinuierlich optimieren und nachhaltiger gestalten.“
Alle Lösungen lassen sich vollständig in bestehende Fertigungsprozesse integrieren und auch nachträglich an veränderte Kapazitäts- und Produktionsanforderungen anpassen. Damit bietet die Technologie ein Höchstmaß an Flexibilität und Skalierbarkeit in der modernen Lackiererei.
Eine besondere Herausforderung für Eisenmann stellte jedoch die Suche nach einer geeigneten Ladestruktur dar.