Wireless power transfer:
How does inductive charging work and what advantages does the process offer?
How does inductive charging work and what advantages does the process offer?
Power without a socket. Wireless power transfer (WPT) can be done with lasers or light, but also electromagnetically. Inductive power transfer is widely used to charge the batteries of electrical devices. However, the method is also increasingly used in automated guided vehicles (AGVs). It has clear advantages over other charging processes.
Tesla as a pioneer of wireless power transmission
When it comes to wireless power transfer of electrical energy, Nikola Tesla must be mentioned as a pioneering inventor. He is considered the developer of alternating current. The physicist and electrical engineer developed an alternating current generator and used it for the long-distance transfer of electrical energy. He was engaged in the generation of high-frequency alternating current and applied for numerous patents. After his death in 1943, the International Committee for Weights and Measures honored him. That’s why since 1960, the physical unit for magnetic flux density has been called Tesla.
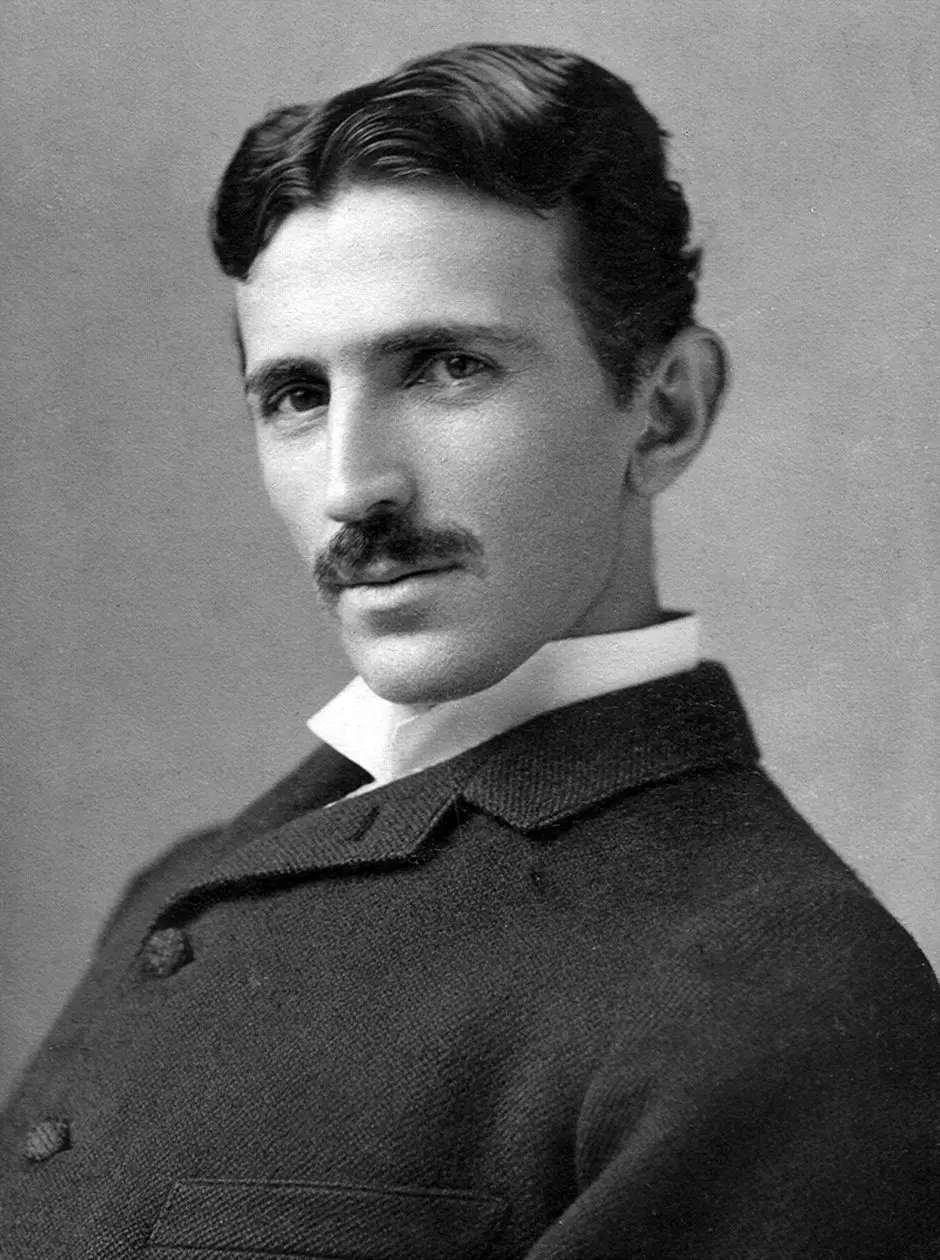
How does wireless energy transfer work?
During a wireless power transfer, a transmitter unit generates an electric magnetic field. This is created when alternating current flows through the coil of this charging station. Via this magnetic resonance, energy is transported wirelessly from the coil of the energy transmitter to the coil of the energy receiver.
The process is based on the principle of induction. A changing magnetic field induces voltage in a nearby conductor and thus generates electric current. The two coils do not touch each other in the process. The range wireless power is a few millimeters to a few centimeters apart.
Application example Autonomous Guided Vehicles (AGVs): Modern industrial trucks are mainly equipped with powerful lithium-ion batteries. These have to be charged after a certain period of use. The process can be carried out efficiently and fully automatically with sophisticated wireless charging concepts. When an AGV or an autonomous mobile robot (AMR) drives into the electromagnetic field of the transmitter coil with a receiver coil, the electric power transfer process starts. The electronic devices of the power transfer systems don’t have to be continuous wasting energy: in modern systems, like the etaLINK 3000 i.e., the wireless power transmission only starts when the receiver coil is upwards detected with an infrared light in range of the transmitter coil. So safety is guaranteed.
Advantages of near field inductive transfer
- Modern power electronics
- Positioning tolerance
- High efficiency
- More efficiency through wireless charging
High efficiency through modern power electronics
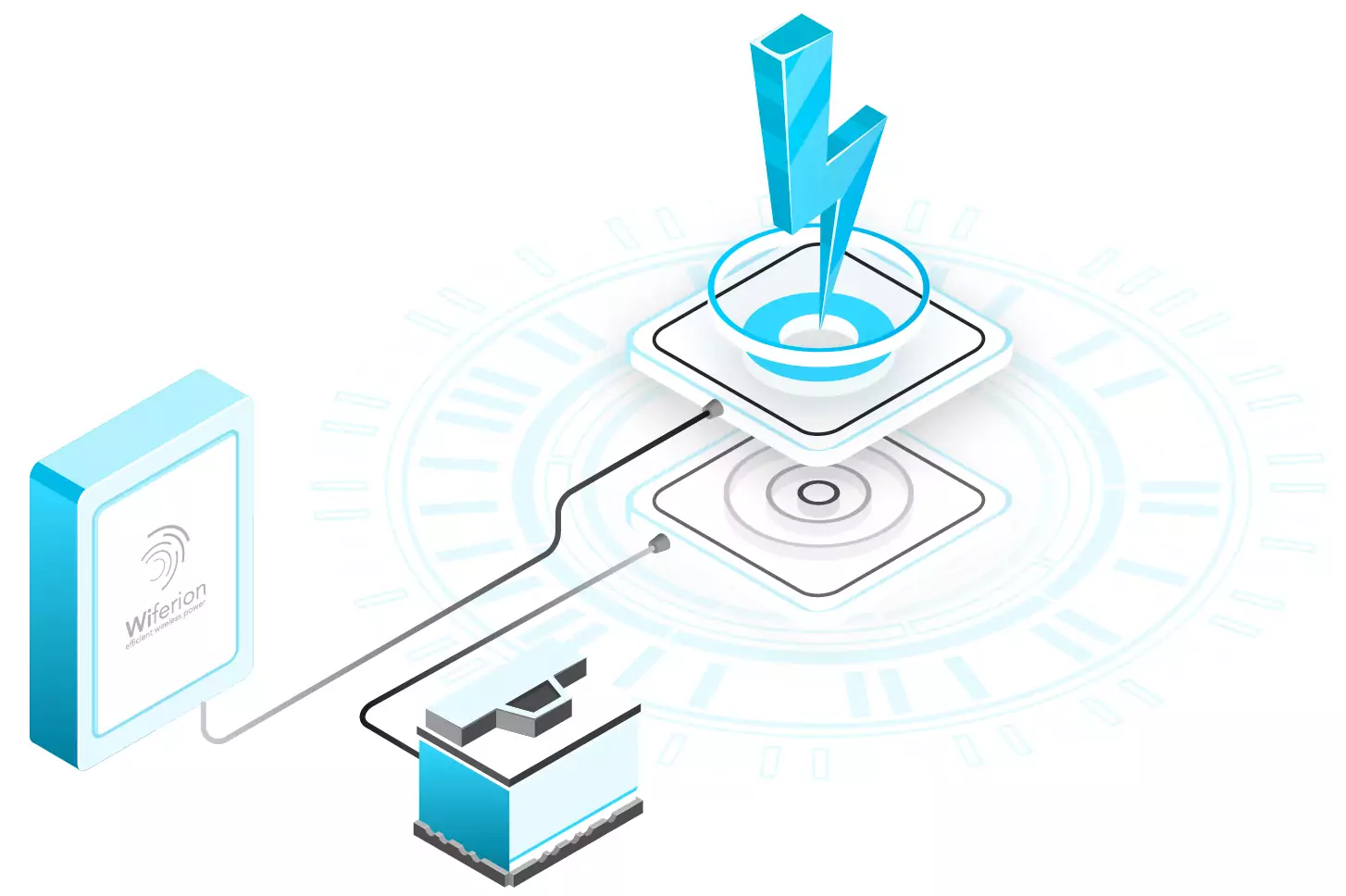
The inductive method of wireless energy transfer shows its superiority above all in the range between 5 watts and several kilowatts. The technology is perfectly suited to bridging an air gap of up to ten centimeters.
In the past, silicon semiconductors were used for current transport. For some years now, more efficient semiconductors have been used, so-called MOSFETS (metal oxide semiconductor field effect transistors). Power electronics thus offer optimum conditions for wireless power transfer. Energy losses can be significantly reduced. In the high-frequency range required for energy transfer, these semiconductors are optimally functional.
As a result, the power electronics in conjunction with the magnetic components achieve a very good efficiency of over 90 percent.
More flexibility due to high positioning tolerance
The high efficiency of the power electronics also allows maximum flexibility in applications. The transmitter and receiver do not have to be positioned in front of each other with millimeter precision to enable the charging process.
In general, the aim is to achieve the best possible coupling between the two coils. If the transmitter coil generates only a low stray field, the energy can be transmitted efficiently. Therefore, even with semiconductors that may be significantly improved in the future, near-field transfer will have an advantage over far-field transmission. This is because the wireless power tranfer is always focused, with optimum efficiency
Wireless power transfer with high efficiency
High efficiency in wireless power transfer can only be realized by efficient power electronics in combination with intelligent software. The etaLINK technology from Wiferion is a good example. It is characterized by optimal operational management, regulation and control of the charging process.
In several steps, the power electronics convert voltage and current from the grid and the battery. The trick in this process is to define the optimum operating points at each conversion stage.
More efficiency through wireless power transfer
From the power grid at the beginning to the consumer, five conversion steps are necessary. In developing the wireless charging system, Wiferion did not just focus on electromagnetic transmission. The focus was on all conversion steps to ensure a highly efficient process. The result is an efficiency of 93 percent.
- At what point do you initiate a switching torque?
- In which operating range does the entire process take place?
- How does one ideally coordinate the individual components of the systems?
Wiferion solves these and other questions with its self-developed power electronics software. The aim is to reduce thermal losses to a minimum throughout the entire charging process. In this way, wireless power transfer leads to maximum economic efficiency.
Charging concepts must optimally meet the requirements of the industry
Wiferion puts the needs of the customer at the center of its charging concepts. Users want to be able to charge their vehicles easily and without great effort. In addition, the interfaces to the vehicle and power grid must be designed in such a way that a simple and intuitive electrical connection succeeds.
With the etaLINK system, the wireless power transfer begins as soon as the vehicle is on or next to the charging station. The distance between the charging pad and the receiver unit in the vehicle can be up to seven centimeters. Vehicles do not have to travel to fixed battery charging stations and charge during breaks or at the end of shifts. Instead, the solution enables intermediate charging (in-process charging) during the production process. This enables fully automated charging processes and higher vehicle availability.
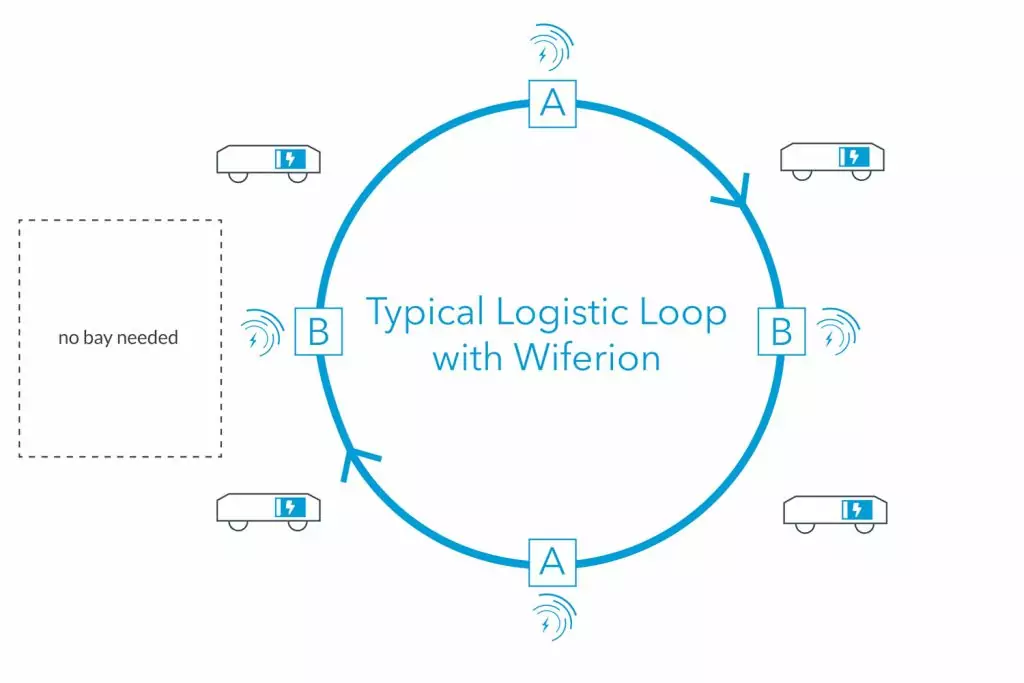
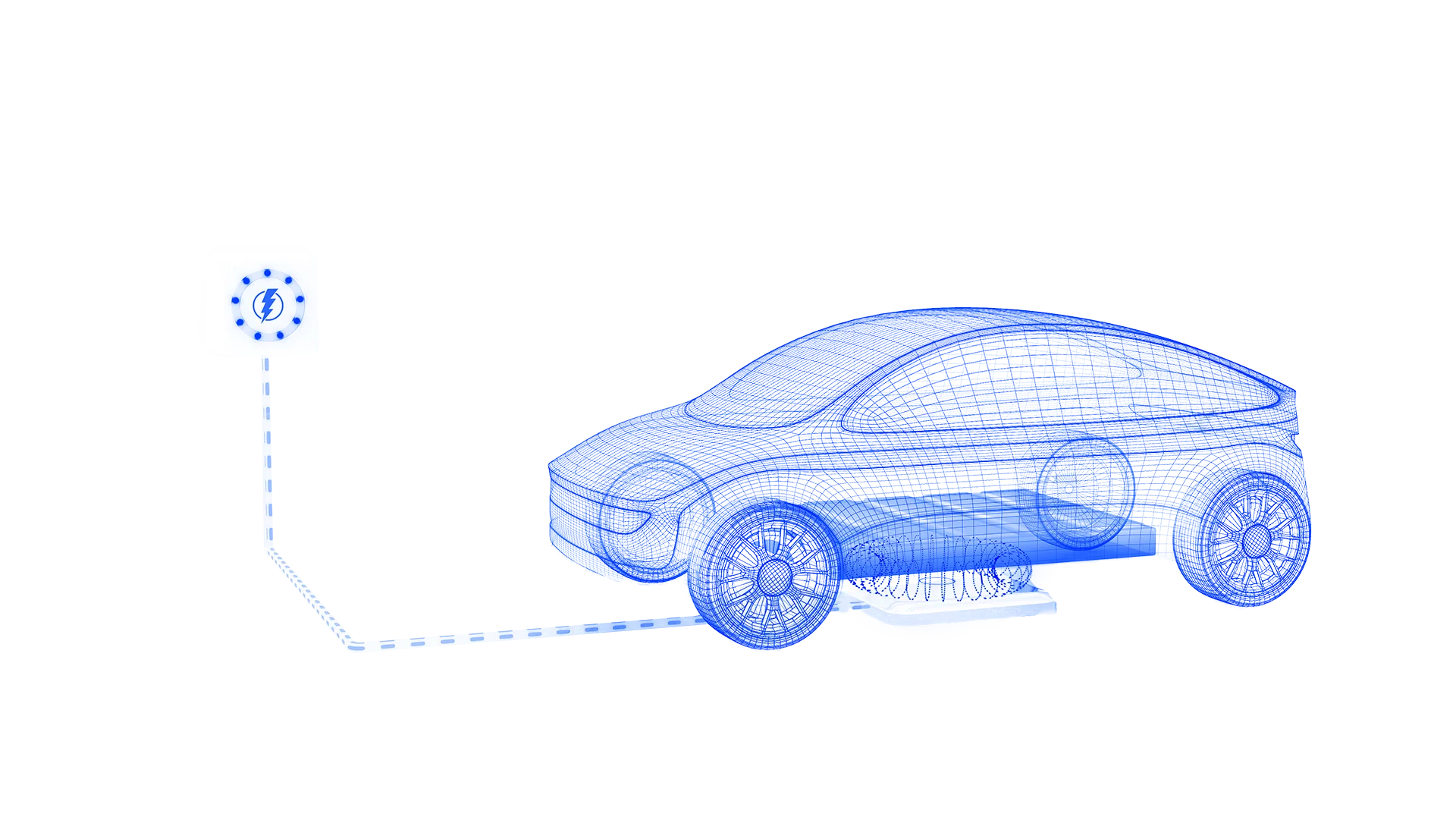
Wireless power transmission for cars
Transmitter and receiver units are also required for wireless energy transmission of high power in e-cars. However, these differ in technical details from the systems and electronics in the industrial sector.
One major difference is the voltage available. While 24 to 80 volts are common in industrial processes, electric vehicle batteries have a nominal voltage of 400 to 800 volts. Thus, to transmit the same power, a significantly higher current flow is required in the industrial sector.
In industry, on the other hand, wireless power transfer is making its way inexorably into production halls. This is the only way to charge AGVs fully automatically and wirelessly. Only «in-process charging» at frequently frequented points can ensure that the vehicles can be used continuously.
Why are wireless power transfer solutions not yet in widespread use in the automotive sector?
Two prerequisites are necessary if inductive charging systems are to be used across the board in the automotive sector:
- the number of e-cars must increase significantly.
- integration into the infrastructure must be improved.
In the industrial sector, charging stations are ideally not installed out of the way, but at suitable locations in the production process. This can be transferred 1:1 to the transport and vehicle sector. It would make sense to install charging points at parking lots, traffic lights or cab stands. These are all frequently visited points.
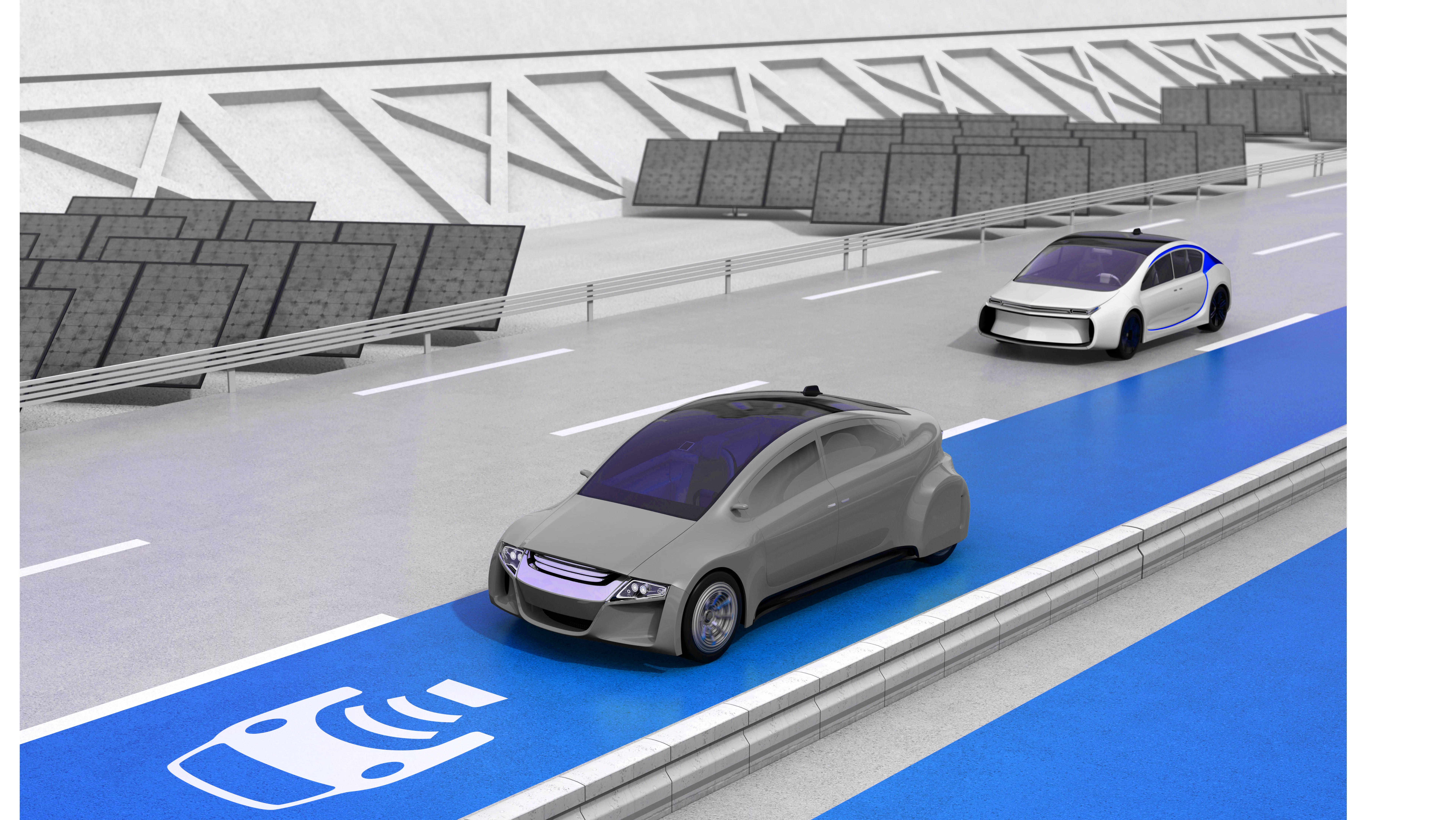
However, there are other aspects to consider in the public sector before the wireless power transfer can be used across the board. For example, special safety precautions would have to be taken. However, in-process charging has the potential to gain importance in the public transport sector in the future. Especially when one considers that autonomous electric cars will also be on the road in the near future.
«In-process charging is an important aspect for us when it comes to further increasing the efficiency of our SOTO robots. Wiferion’s contactless etaLink battery systems can be implemented easily and quickly in any layout and do not require any complex infrastructure.» – Kai Franke, Head of Hardware Development, Magazino
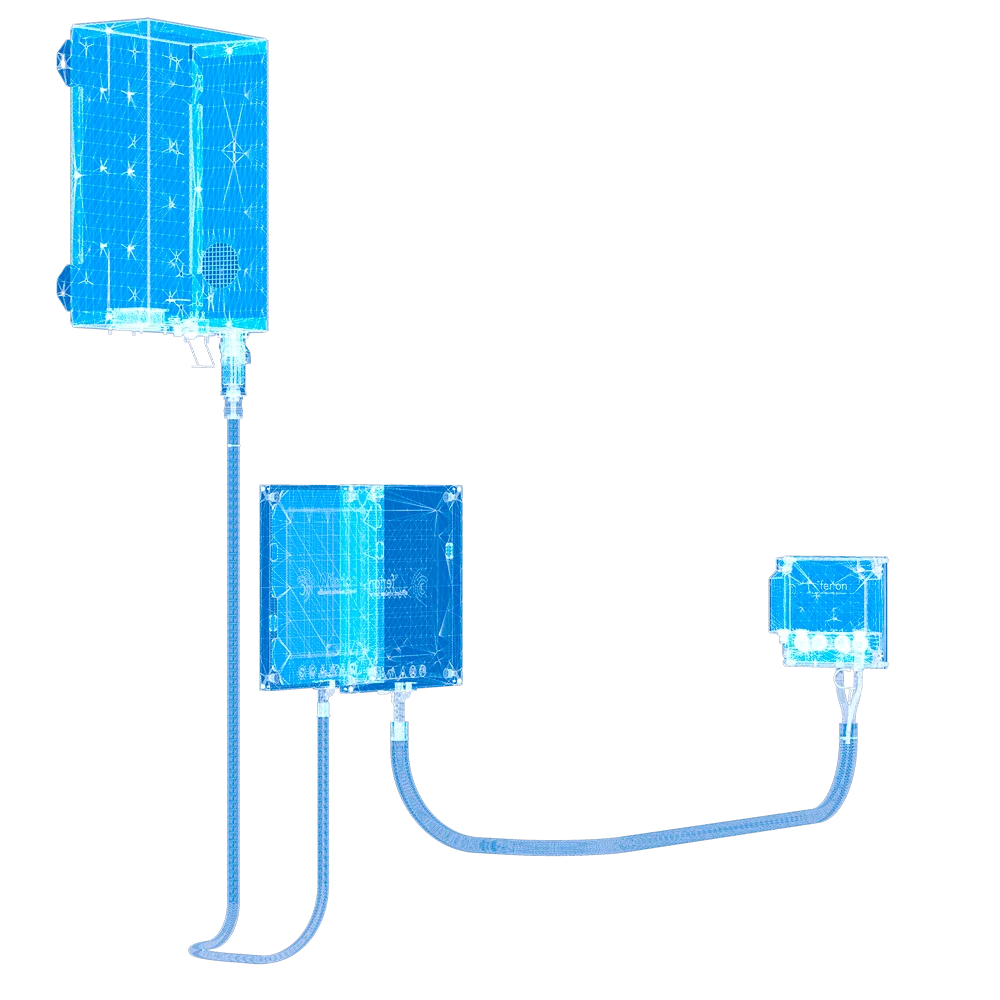
Wireless charging and data transfer
Can data also be transmitted via a magnetic field? In principle, yes. For example, Wiferion uses the inductive point charging system to retrieve data such as energy levels, operating times and vehicle states in real time. The communication interface can be used for any data transfer between the vehicle and stationary electronics. Energy and data basically take the same route, but in different channels. In this way, different communication technologies can be integrated in one device.
However, a legal framework must first be created so that data transfer can take place beyond the industrial sector. This is because the different regulations and standards for radio and electronics still represent a major obstacle.
Selected customers and partners with inductive charging stations
Interested in our wireless power transfer?
Contact us!
Contact us!